The metal casting process is a manufacturing method in which molten metal is poured into a mold to create a desired shape. This technique has been pivotal in shaping numerous industries by allowing for the mass production of intricate and high-precision components. Various metal casting techniques have been developed over the years to cater to different industrial needs, including investment casting, sand casting, and die casting.
Investment casting, often referred to as lost-wax casting, involves creating a wax pattern which is coated in a ceramic material. Once the ceramic is hardened, the wax is melted away, leaving a hollow form ready for the metal to be cast. This method is particularly valued in producing components that require tight tolerances and a smooth finish, making it ideal for specialized parts in industries such as aerospace and medical devices.
Sand casting is one of the oldest and most versatile metal casting techniques. It involves creating a mold out of sand, into which the molten metal is poured. Its adaptability allows it to handle small to large scale production runs, and its cost-effectiveness makes it a preferred choice for metal foundry services across the globe. On the other hand, die casting involves injecting molten metal under high pressure into a mold cavity, which is excellent for producing large volumes of small to medium-sized parts with excellent surface finishes and dimensional accuracy.
Metal casting companies today strive to innovate and improve the metal casting process to increase efficiency and meet the growing demands of modern engineering practices. For instance, aluminum casting is gaining popularity due to aluminum’s light weight, excellent corrosion resistance, and high thermal and electrical conductivity. These properties make it a preferred material for components in industries such as automotive and electronics.
Introducing a new precision-engineered circular component underscores the timeless value of the metal casting process. Crafted from durable materials with a sleek, metallic finish, it's designed for high-performance applications. Its round structure ensures compatibility with various mechanical systems, minimizing resistance while maximizing efficiency. Strategic placement of holes allows for seamless integration and secure fastening, which is essential for use in complex machinery or advanced construction projects. Innovators looking for reliability and excellence in their designs will find this component an invaluable part of their toolkit.
In summary, whether you are a seasoned engineer or a company utilizing metal foundry services to produce innovative products, the metal casting process remains integral to achieving remarkable results in manufacturing. By choosing the appropriate casting techniques, such as investment, sand, or die casting, you can ensure the production of high-quality components that meet the specific requirements of your industry.
Mastering the Metal Casting Process: Techniques and Innovations
Get Latest Price >
Label | Value |
---|---|
Brand | LS Custom Parts Manufacturers |
Customization Service | Metal Casting, Sand Casting, Low Pressure Casting, High Pressure Casting, Investment Casting |
Drawing format | 2D/(PDF/CAD)、3D(IGES/STEP/GLB) |
Material Capabilities | Aluminum、Brass、Bronze、Copper、Hardened Metals、Precious Metals、Stainless Steel、Alloys、TPR |
Sample | Free |
Supply Ability | 100000 Pieces Per Day |
Surface Finish | Customized Finishing |
Thickness | Customized Thickness |
Type | Broaching/Drilling/Etching / Chemical Machining/Laser Machining/Milling/Turning/Wire EDM/Rapid Prototyping/Other Machining Services |
Services | CNC Machining,Metal Casting,Injection Molding,Sheet Metal Fabrication,Rapid Prototyping,3D Printing |
Find Similar Products
Contact
Ready to start your next project with LS Manufacturing?
Contact us today to learn more about our services and how we can help you achieve your goals.
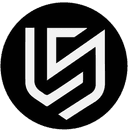
Rapid lead times starting from just 1 business day.
ISO 9001,ISO 14001,IATF 16949 and AS9100D Certification.
Over 100 materials available, with 50+ surface finish options.
Cost-effective mass production.
Order as low as 1 piece.
People who viewed this also viewed
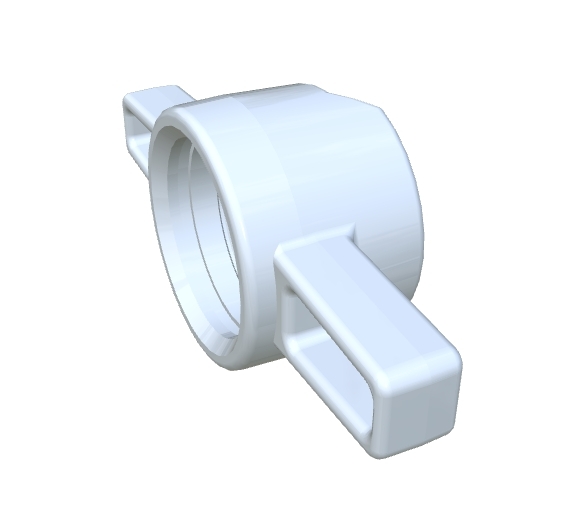
Exploring Metal Casting Techniques for CNC Precision
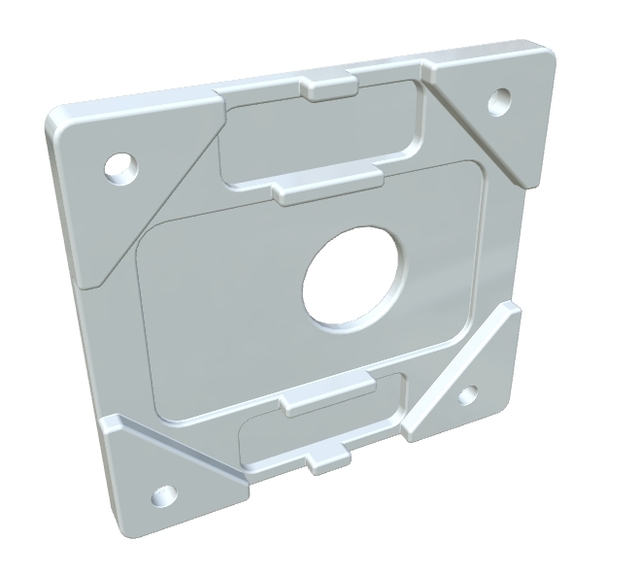
Investment Casting Benefits: Unlocking Precision & Durability
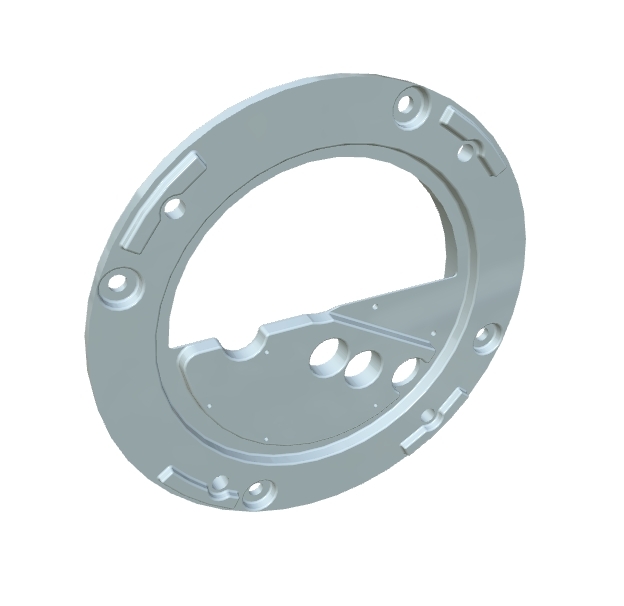
Investment Casting Process for Precision Engineering
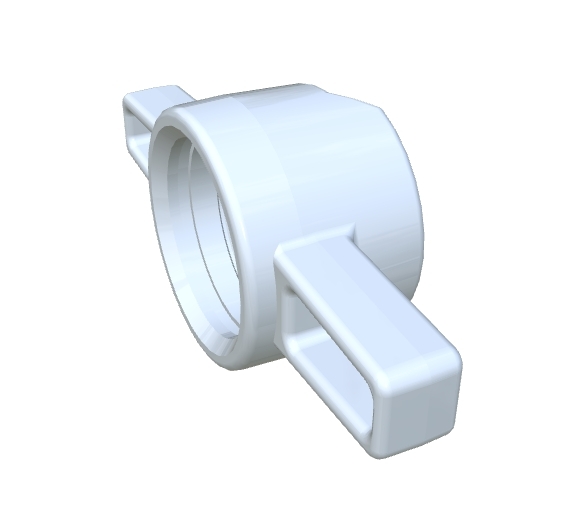
Understanding the Investment Casting Process: Techniques and Benefits
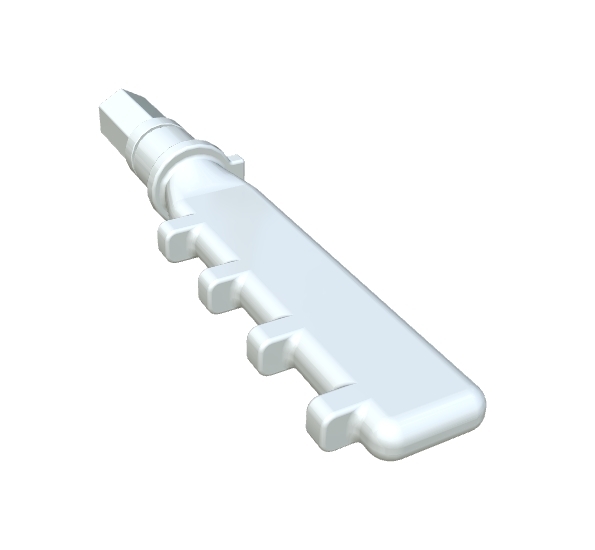
Investment Casting: Techniques and Modern Applications
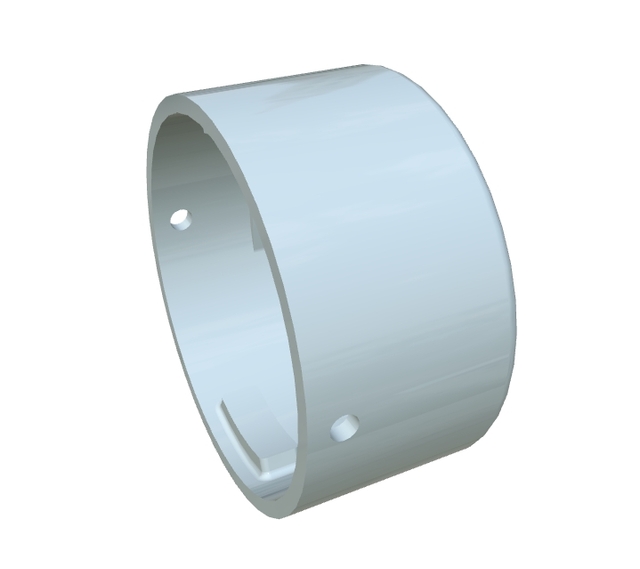
The Investment Casting Process: Precision & Advantage
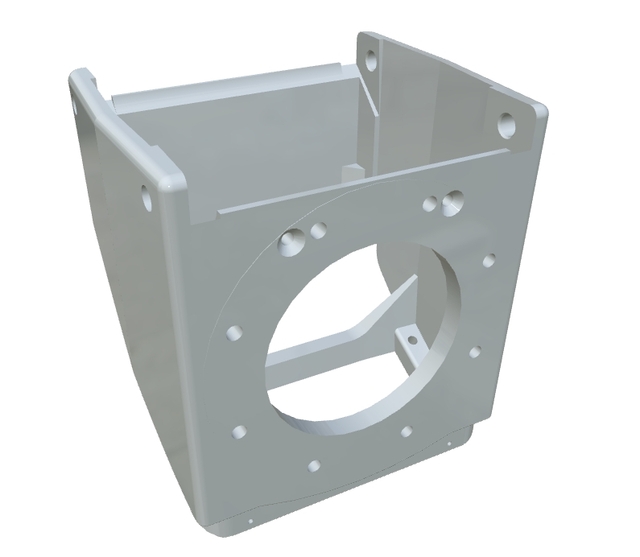
Investment Casting Process: Precision & Advantages
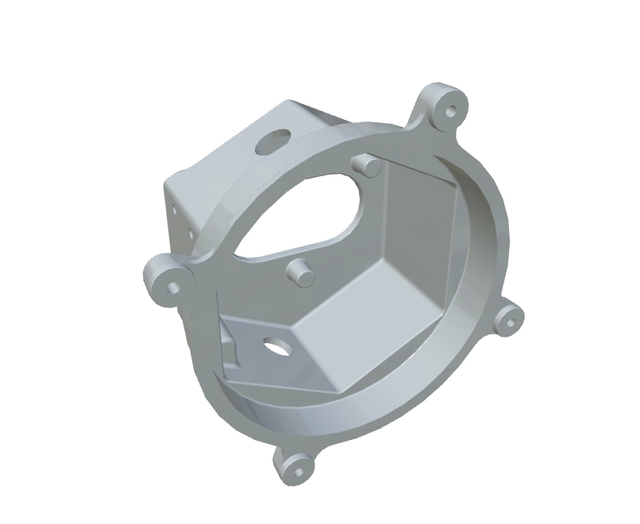
Understanding the Investment Casting Process and Its Advantages
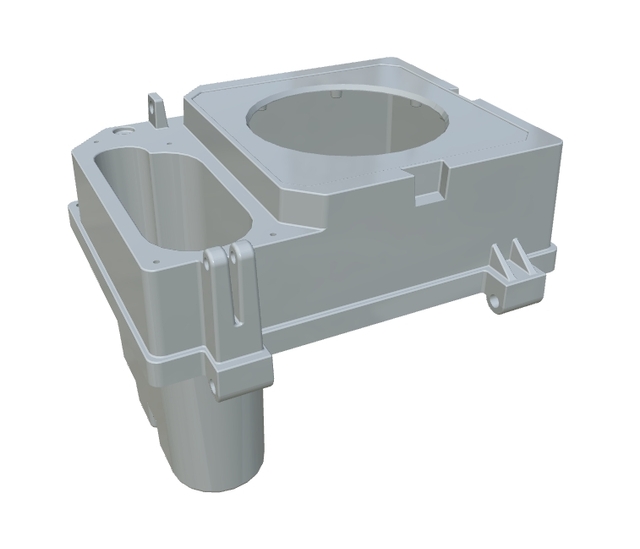
Investment Casting Manufacturers: Precision & Innovation
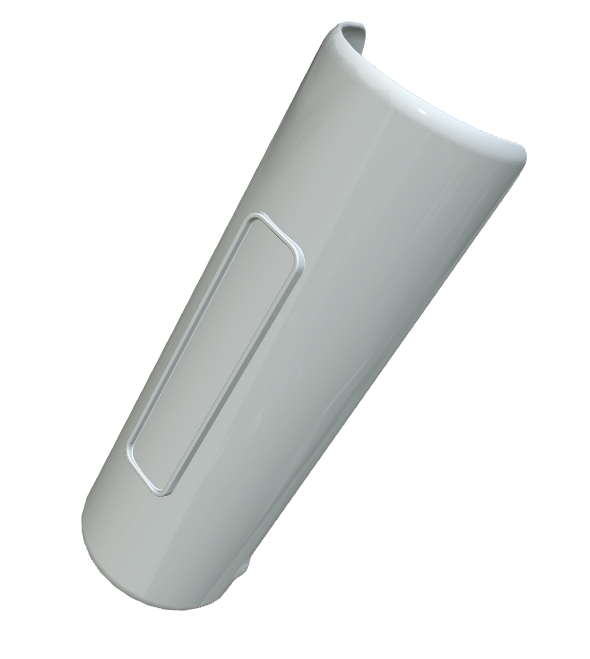
Sand Casting Process: Benefits and Techniques