The **sand casting process** is a foundational method in the manufacturing industry, particularly valued for its versatility and cost-effectiveness. This technique involves creating metal components by casting molten metal into sand molds. Over the years, the process has become widely adopted in diverse industries, including automotive, due to the multitude of benefits it offers over other manufacturing techniques.
One of the primary **benefits of sand casting** is its ability to handle complex shapes and sizes that other casting methods may find challenging. This makes it particularly suitable for producing parts like the automotive transmission system, where precision engineering and efficiency are paramount. The materials used in sand casting are predominantly silica sand, clay, and water, which are molded around a pattern of the desired shape, creating a negative impression to house the molten metal. The sand casting materials are key to ensuring the quality of the final product, providing the necessary durability and stability.
However, like any other industrial process, sand casting is not without its challenges. **Sand casting defects**, such as shrinkage, porosity, and surface imperfections, can occur, but with advanced techniques and vigilant quality control, such issues can be minimized. Understanding **how sand casting works** allows manufacturers to optimize the process, ensuring that components such as the cutting-edge automotive transmission system are crafted with precision. This precision is crucial in automotive applications, where the seamless integration of parts can significantly impact performance and fuel efficiency.
When comparing **sand casting vs metal casting**, the former stands out for its economical nature, especially in producing small-batch items or prototypes. Additionally, the sand casting techniques have evolved substantially, allowing for enhanced accuracy and surface finish, making it a viable alternative for parts previously restricted to metal casting methods. This adaptability is a testament to the sand casting process's enduring relevance in industries focused on innovation and efficiency. Types of sand casting include green sand casting, dry sand casting, and shell mold casting, each offering unique benefits depending on the specific requirements of the product.
In conclusion, the sand casting process continues to play a significant role in the production of vital components such as automotive transmission systems. This process not only supports the demand for high-quality, durable parts but also aligns with the industry's pursuit of balancing power and economy through advanced technology. As manufacturers strive for excellence, the incorporation of modern **sand casting techniques** enhances their ability to deliver sophisticated and functional products, embodying the future of automotive technology.
Sand Casting Process: Benefits and Techniques
Get Latest Price >
Label | Value |
---|---|
Brand | LS Custom Parts Manufacturers |
Customization Service | Metal Casting, Sand Casting, Low Pressure Casting, High Pressure Casting, Investment Casting |
Drawing format | 2D/(PDF/CAD)、3D(IGES/STEP/GLB) |
Material Capabilities | Aluminum、Brass、Bronze、Copper、Hardened Metals、Precious Metals、Stainless Steel、Alloys、TPR |
Sample | Free |
Supply Ability | 100000 Pieces Per Day |
Surface Finish | Customized Finishing |
Thickness | Customized Thickness |
Type | Broaching/Drilling/Etching / Chemical Machining/Laser Machining/Milling/Turning/Wire EDM/Rapid Prototyping/Other Machining Services |
Services | CNC Machining,Metal Casting,Injection Molding,Sheet Metal Fabrication,Rapid Prototyping,3D Printing |
Contact
Ready to start your next project with LS Manufacturing?
Contact us today to learn more about our services and how we can help you achieve your goals.
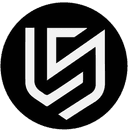
Rapid lead times starting from just 1 business day.
ISO 9001,ISO 14001,IATF 16949 and AS9100D Certification.
Over 100 materials available, with 50+ surface finish options.
Cost-effective mass production.
Order as low as 1 piece.