The **sand casting process** is one of the most widely used metal casting methods in the manufacturing industry today. It involves creating a mold from a sand mixture and pouring molten metal into the mold to form a desired shape. This process is cherished for its versatility and flexibility, accommodating a variety of metals and mold designs, making it a preferred technique in the industry.
Understanding **what is sand casting** is essential for those looking to leverage its potential benefits in manufacturing. Essentially, it begins with the mixing of sand with a bonding agent to create a mold. Patterns of the desired shape are formed in the sand, leaving a cavity in which the molten metal is poured. Once the metal solidifies, the sand is broken away, revealing the final product. This simplicity in method allows for a high degree of customization, which is a significant advantage of sand casting.
There are different **sand casting techniques** available depending on the requirements of the project. Some common techniques include green sand casting, dry sand casting, and resin sand casting. The choice of technique can impact both the texture and quality of the final product. Despite its numerous advantages, such as versatility and low cost, there are **sand casting disadvantages** to consider, including limited precision and potential for defects, which must be managed carefully.
The versatility of sand casting allows it to be used in various **sand casting applications**. It's ideal for producing everything from simple components to intricate designs seen in automotive parts, machinery, and even home goods like the Multi-Hook Wall Organizer. By utilizing durable materials and innovative design, products like these can capitalize on the strengths of sand casting to deliver functional yet elegant solutions for modern problems.
When considering the **sand casting materials**, virtually any type of metal that can be melted can potentially be used in sand casting, offering incredible versatility. Materials like iron, steel, aluminum, and copper alloys are commonly used, each providing different **sand casting advantages** depending on the specific needs, such as strength, weight, or corrosion resistance.
For companies looking to produce high-quality, functional items, understanding the types of sand casting can offer a significant competitive advantage. Whether it's creating sleek products like the Multi-Hook Wall Organizer, which perfectly embodies style and functionality, or more industrial applications, leveraging the sand casting process can help in producing precise, reliable products that meet consumer and market demands alike.
In summary, the sand casting process continues to be a cornerstone in manufacturing due to its adaptability and efficiency. While weighing the pros and cons through **sand casting techniques** is important, its flexibility in material use and application keeps it a popular choice among various industries, providing essential support in the creation of both everyday and specialized products.
Exploring the Versatile Sand Casting Process in Modern Manufacturing
Get Latest Price >
Label | Value |
---|---|
Brand | LS Custom Parts Manufacturers |
Customization Service | Metal Casting, Sand Casting, Low Pressure Casting, High Pressure Casting, Investment Casting |
Drawing format | 2D/(PDF/CAD)、3D(IGES/STEP/GLB) |
Material Capabilities | Aluminum、Brass、Bronze、Copper、Hardened Metals、Precious Metals、Stainless Steel、Alloys、TPR |
Sample | Free |
Supply Ability | 100000 Pieces Per Day |
Surface Finish | Customized Finishing |
Thickness | Customized Thickness |
Type | Broaching/Drilling/Etching / Chemical Machining/Laser Machining/Milling/Turning/Wire EDM/Rapid Prototyping/Other Machining Services |
Services | CNC Machining,Metal Casting,Injection Molding,Sheet Metal Fabrication,Rapid Prototyping,3D Printing |
Find Similar Products
Contact
Ready to start your next project with LS Manufacturing?
Contact us today to learn more about our services and how we can help you achieve your goals.
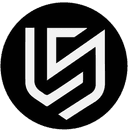
Rapid lead times starting from just 1 business day.
ISO 9001,ISO 14001,IATF 16949 and AS9100D Certification.
Over 100 materials available, with 50+ surface finish options.
Cost-effective mass production.
Order as low as 1 piece.
People who viewed this also viewed
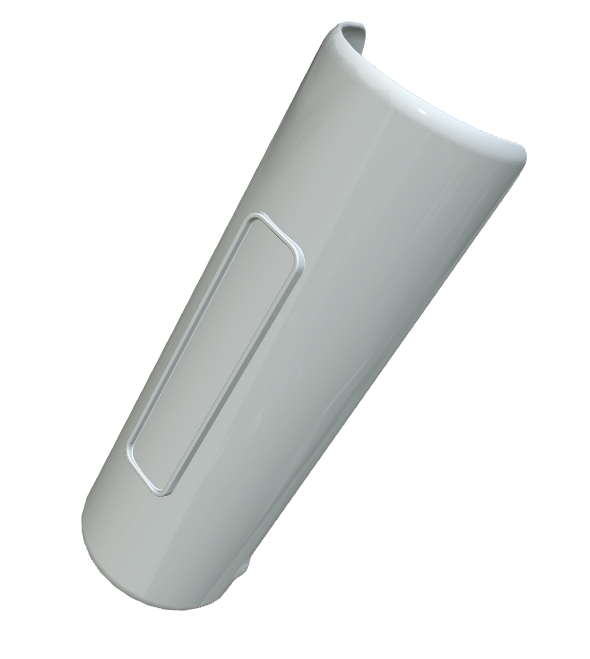
Sand Casting Process: Benefits and Techniques
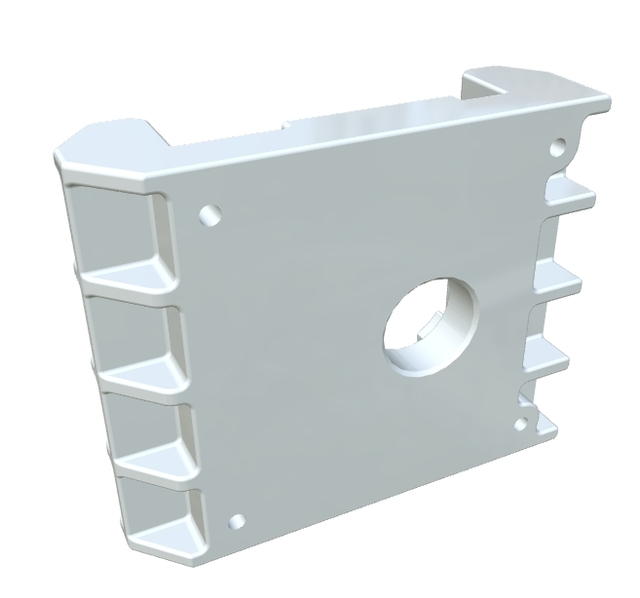
Sand Casting Techniques: Modern Methods for Complex Designs
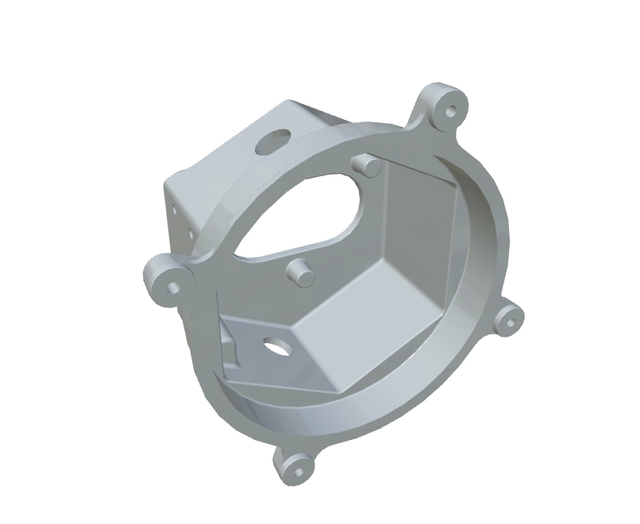
Casting Agency: Essential Services for Entertainment
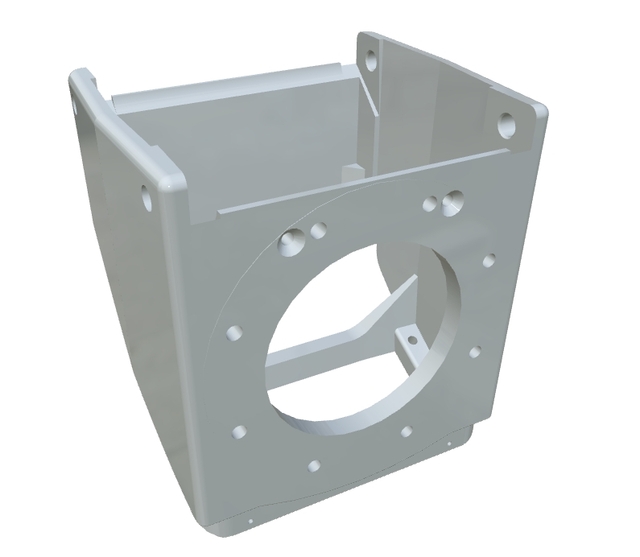
Expert Casting Services for Precision Components
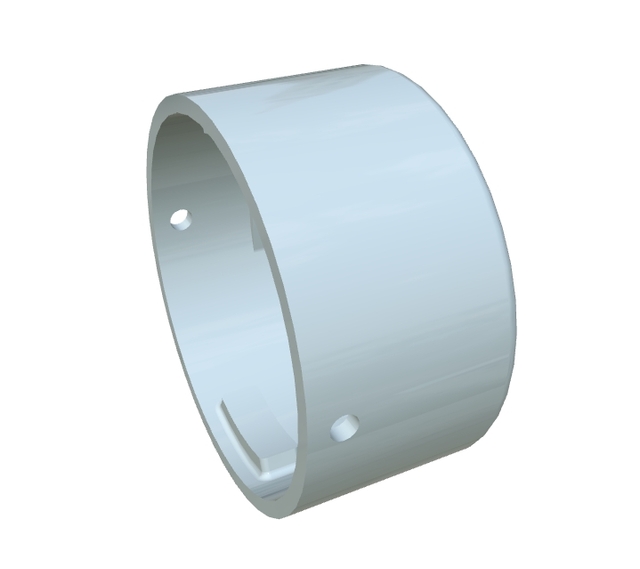
The Sand Casting Process: Techniques, Materials, and Applications
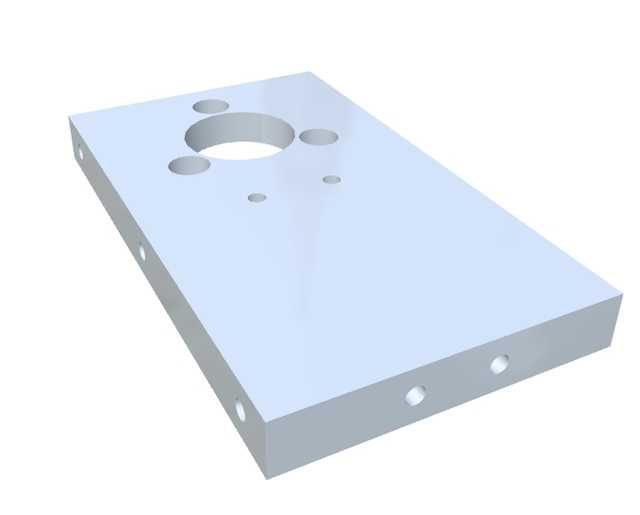
The Sand Casting Process: Advantages & Techniques Unveiled
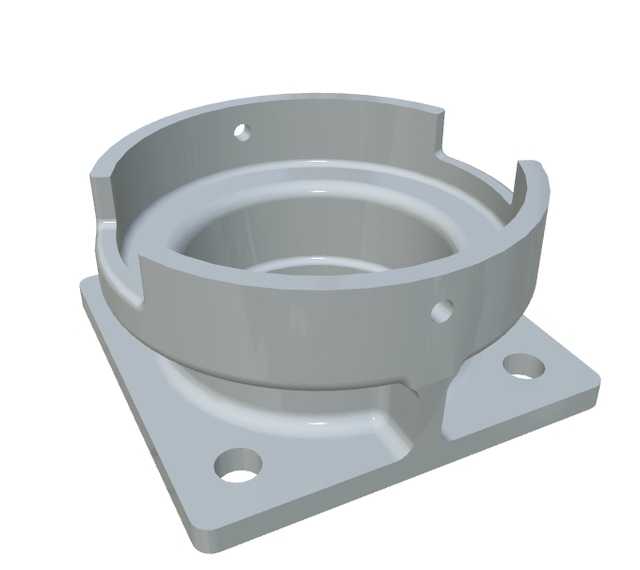
Mastering Sand Casting Techniques for Innovative Solutions
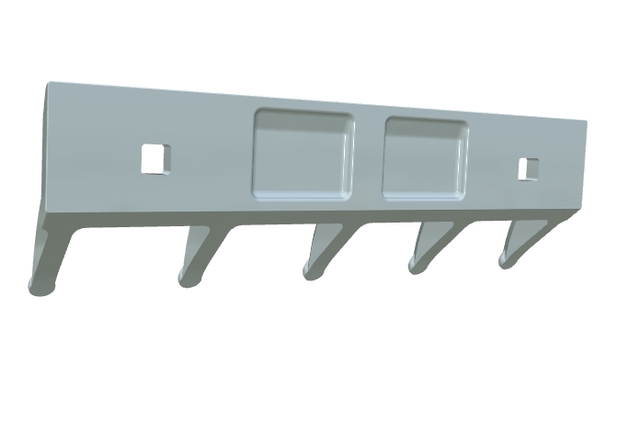
Exploring the Versatile Sand Casting Process in Modern Manufacturing