The **sand casting process** is a cornerstone in the manufacturing world, renowned for its versatility and efficiency in creating complex metal parts. As industries evolve, the demand for precision-engineered components continues to rise, making the sand casting technique an indispensable tool in the production of high-quality industrial components. This process involves creating a mold, primarily from sand, that forms the intricate shapes of the desired metal component.
A key advantage of the sand casting process is its ability to accommodate complex designs with ease. Whether utilized in sand casting foundries or smaller workshops, this technique enables the creation of finely detailed and robust components. Notably, sand casting molds are excellent for producing components like the cylindrical component described in the product information — designed meticulously for precision and reliability. Such components are highly suitable for dynamic environments, given their sturdy construction and polished surfaces that ensure minimal friction.
Sand casting materials, commonly sand and a binding agent, are fundamental to producing molds capable of withstanding the intense heat and pressure involved in metal casting. This makes the mold durable and reusable, optimizing production in manufacturing. Another benefit is the process’s cost-effectiveness, particularly in low to medium volume productions, stemming from the low cost of materials and simplicity of the technology used.
Despite the myriad benefits, the sand casting process is not without its challenges. Sand casting defects can sometimes occur, such as unwanted voids or imperfections within the final product due to improper mold preparation or handling. However, these potential issues are often anticipated and mitigated through meticulous quality control measures and advanced techniques used in modern sand casting applications.
The applications of sand casting are vast, spanning sectors from industrial machinery to consumer electronics, as evidenced by the strategically designed cylindrical component that seamlessly integrates with other parts. Such versatility highlights the transformative capabilities of this process in producing essential components across diverse industries.
Ultimately, the advantages of sand casting — including its adaptability, material efficiency, and ability to produce high-quality metal components — underscore its enduring presence in modern manufacturing. As technology advances, the sand casting technique continues to evolve, leveraging innovations that further enhance its applications and outcomes in the competitive landscape of production.
The Sand Casting Process: Techniques, Materials, and Applications
Get Latest Price >
Label | Value |
---|---|
Brand | LS Custom Parts Manufacturers |
Customization Service | Metal Casting, Sand Casting, Low Pressure Casting, High Pressure Casting, Investment Casting |
Drawing format | 2D/(PDF/CAD)、3D(IGES/STEP/GLB) |
Material Capabilities | Aluminum、Brass、Bronze、Copper、Hardened Metals、Precious Metals、Stainless Steel、Alloys、TPR |
Sample | Free |
Supply Ability | 100000 Pieces Per Day |
Surface Finish | Customized Finishing |
Thickness | Customized Thickness |
Type | Broaching/Drilling/Etching / Chemical Machining/Laser Machining/Milling/Turning/Wire EDM/Rapid Prototyping/Other Machining Services |
Services | CNC Machining,Metal Casting,Injection Molding,Sheet Metal Fabrication,Rapid Prototyping,3D Printing |
Find Similar Products
Contact
Ready to start your next project with LS Manufacturing?
Contact us today to learn more about our services and how we can help you achieve your goals.
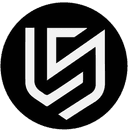
Rapid lead times starting from just 1 business day.
ISO 9001,ISO 14001,IATF 16949 and AS9100D Certification.
Over 100 materials available, with 50+ surface finish options.
Cost-effective mass production.
Order as low as 1 piece.
People who viewed this also viewed
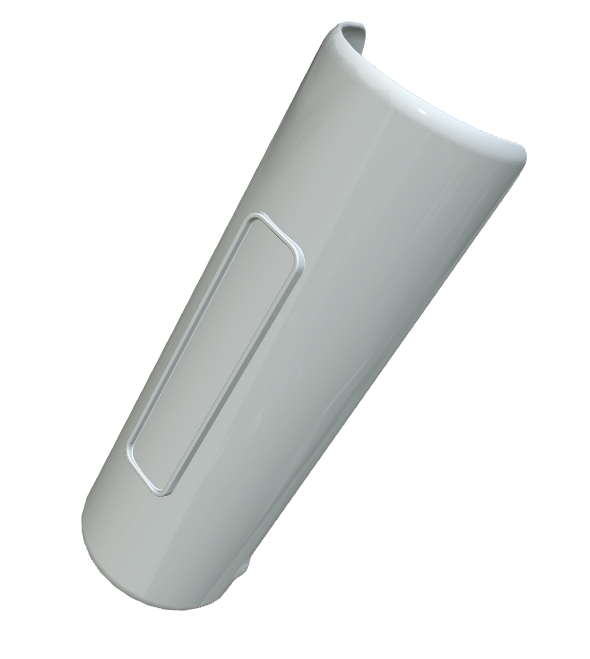
Sand Casting Process: Benefits and Techniques
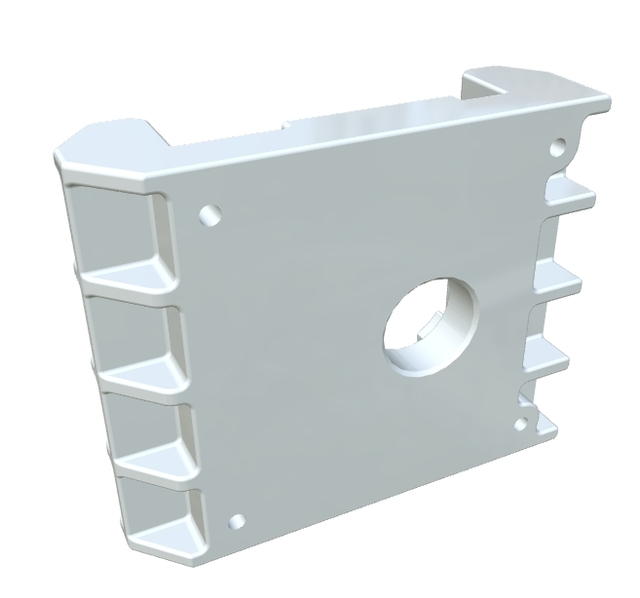
Sand Casting Techniques: Modern Methods for Complex Designs
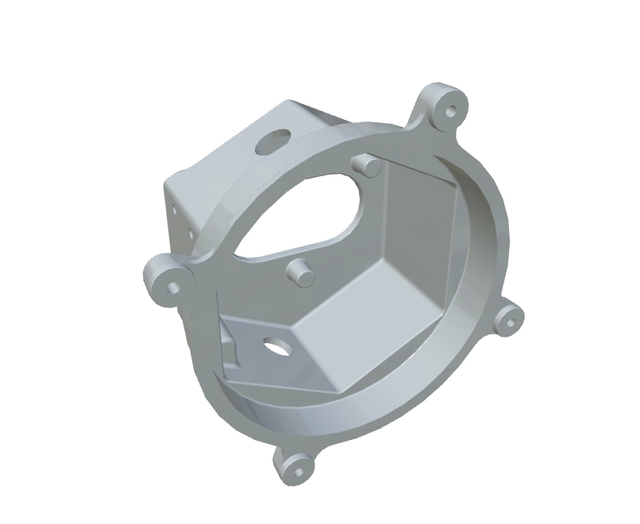
Casting Agency: Essential Services for Entertainment
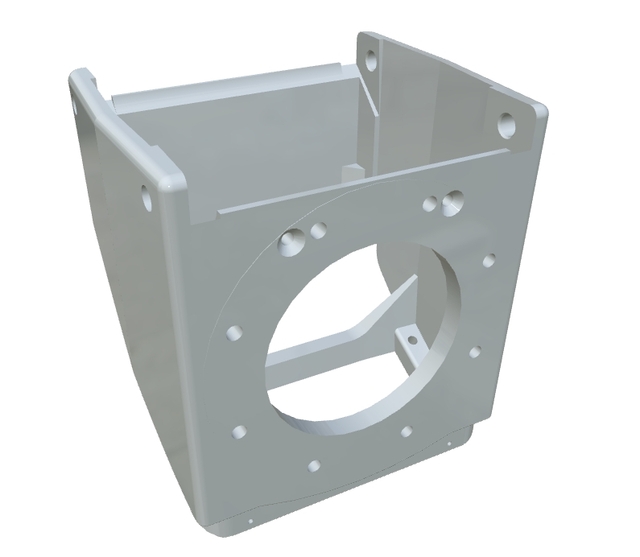
Expert Casting Services for Precision Components
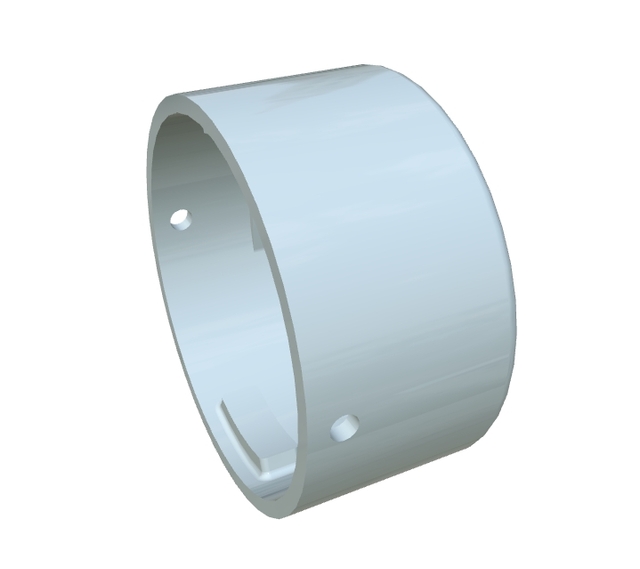
The Sand Casting Process: Techniques, Materials, and Applications
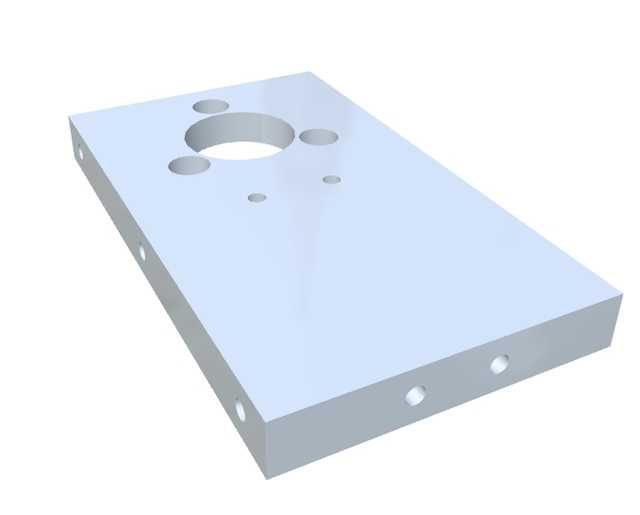
The Sand Casting Process: Advantages & Techniques Unveiled
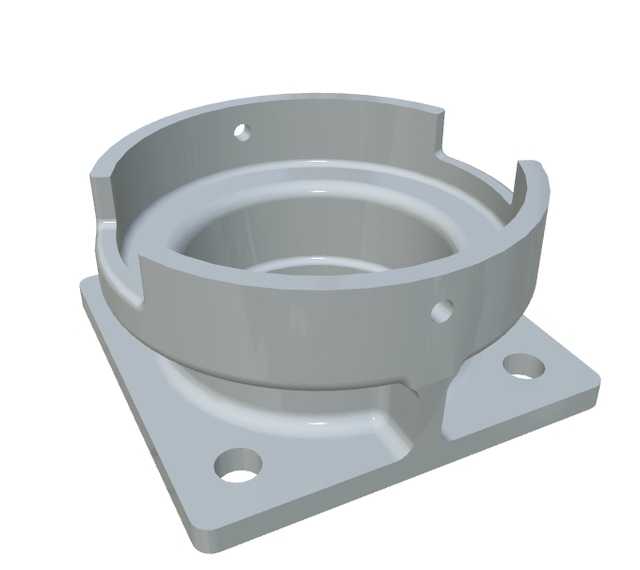
Mastering Sand Casting Techniques for Innovative Solutions
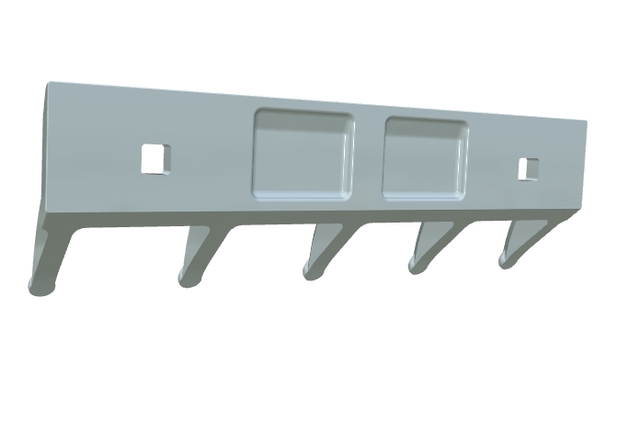
Exploring the Versatile Sand Casting Process in Modern Manufacturing