The injection molding process is a highly sophisticated manufacturing technique used to produce a wide array of products ranging from small components to large complex items. This process involves injecting molten material into a mold cavity to create the desired shape. The use of high-quality injection molding materials is crucial, as it determines the strength and durability of the final product.
In recent years, custom injection molding has become increasingly popular due to the growing demand for specialized and unique components in various industries. Custom injection molding services offer advantages such as flexibility in design, efficiency in production, and cost-effectiveness. Companies specializing in these services work closely with clients to tailor their components to meet specific requirements, accommodating both small-scale and large-scale production needs.
Injection molding manufacturers play a vital role in the production of formidable and innovative products. They utilize both thermoplastic injection molding and thermoset injection molding processes, depending on the nature of the material and the intended application. Thermoplastic injection molding is widely used due to its recyclability and versatility in manufacturing robust and flexible components. On the other hand, thermoset injection molding is preferred when creating items that require heat resistance and structural integrity.
A core component of the injection molding setup is the injection molding machine itself, which is designed to handle various materials and guarantees high-precision output. These machines are constantly evolving, integrating cutting-edge technology to ensure efficiency and quality in every production cycle. The choice of the appropriate machine depends on the type of material to be molded and the desired properties of the finished product.
One groundbreaking product developed using the injection molding process is the Multi-Layered Engineering Block, an innovative solution in modular construction technology. These blocks are precision-engineered, showcasing multiple layers that are interwoven with advanced fastening systems. Such innovative design allows for seamless integration with various components, making it perfect for industrial applications and modern architectural projects.
Each engineering block is crafted from high-grade materials which ensure durability and resilience, even under extreme conditions. This product is particularly remarkable because of its strategically placed holes that facilitate easy assembly and enhance its functional properties. The varying shades of metallic finishes not only offer a modern aesthetic appeal but also signify different structural or functional characteristics.
In both industry and architecture, the Multi-Layered Engineering Block sets a new standard, streamlining assembly processes while offering unmatched strength and flexibility. Whether utilized in constructing complex machinery or shaping architectural facades, this novel product is designed to expand the potential of contemporary design and engineering.
In conclusion, the various facets of the injection molding process, including the diverse materials, advanced molding techniques, and state-of-the-art machinery, contribute significantly to the production of high-quality and innovative products. The Multi-Layered Engineering Block exemplifies how this process can be harnessed to deliver components that not only fulfill functional requirements but also push the boundaries of modern design.
Understanding the Injection Molding Process for Innovation
Get Latest Price >
Label | Value |
---|---|
Brand | LS Custom Parts Manufacturers |
Customization Service | Injection Molding, Plastic Injection Molding, Plastic Injection Molds, Insert Molding, Overmolding |
Drawing format | 2D/(PDF/CAD)、3D(IGES/STEP/GLB) |
Material Capabilities | Aluminum、Brass、Bronze、Copper、Hardened Metals、Precious Metals、Stainless Steel、Alloys、TPR |
Sample | Free |
Supply Ability | 100000 Pieces Per Day |
Surface Finish | Customized Finishing |
Thickness | Customized Thickness |
Type | Broaching/Drilling/Etching / Chemical Machining/Laser Machining/Milling/Turning/Wire EDM/Rapid Prototyping/Other Machining Services |
Services | CNC Machining,Metal Casting,Injection Molding,Sheet Metal Fabrication,Rapid Prototyping,3D Printing |
Contact
Ready to start your next project with LS Manufacturing?
Contact us today to learn more about our services and how we can help you achieve your goals.
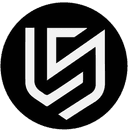
Rapid lead times starting from just 1 business day.
ISO 9001,ISO 14001,IATF 16949 and AS9100D Certification.
Over 100 materials available, with 50+ surface finish options.
Cost-effective mass production.
Order as low as 1 piece.