The **injection molding process** is a cornerstone in the world of manufacturing, revolutionizing how products are designed and produced. This process, essential to creating a wide array of **injection molded parts**, is known for its ability to produce complex shapes with high precision. At its core, the injection molding process involves heating a thermoplastic material until it becomes molten, then injecting it into a mold where it cools and solidifies into the desired shape.
One of the vital components in the injection molding process is the **injection molding machine**. These machines play a crucial role in the efficiency and quality of the manufacturing process. They are designed to handle high volumes with precision, making them indispensable in industries ranging from automotive to consumer electronics. The capability to produce consistent results with minimal waste makes them an invaluable asset in **plastic injection molding**.
When it comes to **injection molding design**, companies emphasize on creativity and innovation. A well-thought-out design is crucial for optimizing the production process, reducing cost, and ensuring the end product's functionality and aesthetics. One burgeoning trend is **custom injection molding**, which allows companies to tailor products specifically to meet unique consumer needs or project requirements. This customization is facilitated by advancements in design software and machine capabilities, offering immense flexibility to manufacturers.
In the realm of modern architecture and construction, products such as the newly introduced **metal channel bracket**, highlight the versatility of components created through injection molding. This bracket, crafted from high-grade steel, showcases a robust design with precise cuts and geometric contours. Its open channel design allows it to adapt seamlessly into various applications, whether it is to support structural elements or enclose electrical and mechanical installations.
Moreover, the bracket's polished finish not only bolsters its strength but also enhances its aesthetic appeal, making it a fitting choice for contemporary projects. It is engineered for easy installation, offering compatibility with a diverse range of materials. Such products underline the importance of functional design and the role of **injection molding manufacturing** in creating solutions that are both practical and aesthetically pleasing.
**Injection molding companies** are pivotal in driving innovation and efficiency in this space. By continually investing in technology and refining the injection molding process, these companies ensure they stay ahead in a competitive market. As the demand for precise, durable, and stylish components grows, the role of injection molding in delivering high-quality outcomes will only become more pronounced.
The Injection Molding Process: Innovations and Applications
Get Latest Price >
Label | Value |
---|---|
Brand | LS Custom Parts Manufacturers |
Customization Service | Injection Molding, Plastic Injection Molding, Plastic Injection Molds, Insert Molding, Overmolding |
Drawing format | 2D/(PDF/CAD)、3D(IGES/STEP/GLB) |
Material Capabilities | Aluminum、Brass、Bronze、Copper、Hardened Metals、Precious Metals、Stainless Steel、Alloys、TPR |
Sample | Free |
Supply Ability | 100000 Pieces Per Day |
Surface Finish | Customized Finishing |
Thickness | Customized Thickness |
Type | Broaching/Drilling/Etching / Chemical Machining/Laser Machining/Milling/Turning/Wire EDM/Rapid Prototyping/Other Machining Services |
Services | CNC Machining,Metal Casting,Injection Molding,Sheet Metal Fabrication,Rapid Prototyping,3D Printing |
Find Similar Products
Contact
Ready to start your next project with LS Manufacturing?
Contact us today to learn more about our services and how we can help you achieve your goals.
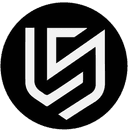
Rapid lead times starting from just 1 business day.
ISO 9001,ISO 14001,IATF 16949 and AS9100D Certification.
Over 100 materials available, with 50+ surface finish options.
Cost-effective mass production.
Order as low as 1 piece.
People who viewed this also viewed
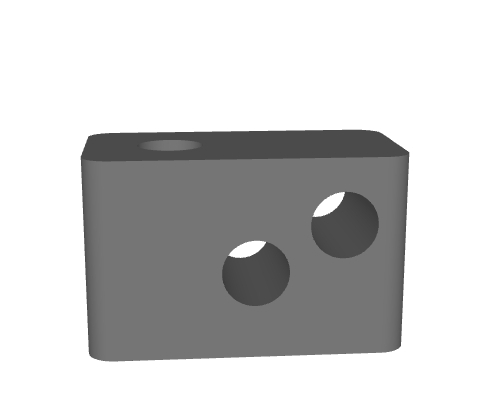
CNC Machining: Precision Innovations in Automotive Parts

Mastering the Overmolding Process for Superior Design
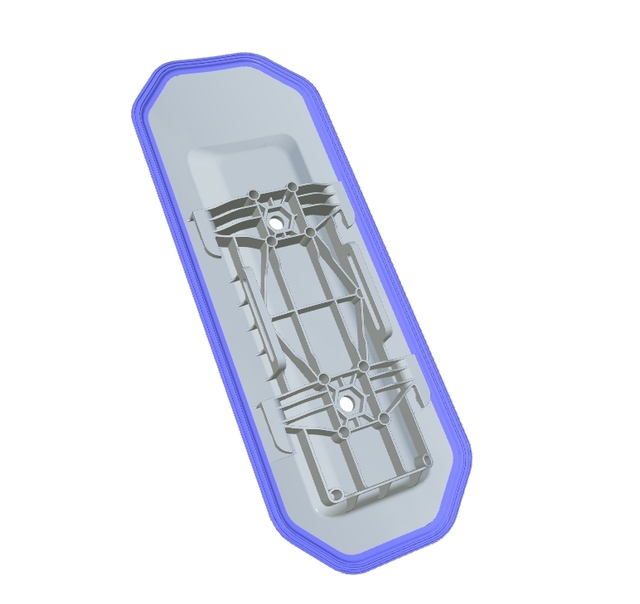
Overmolding Process: Revolutionizing Material Technology
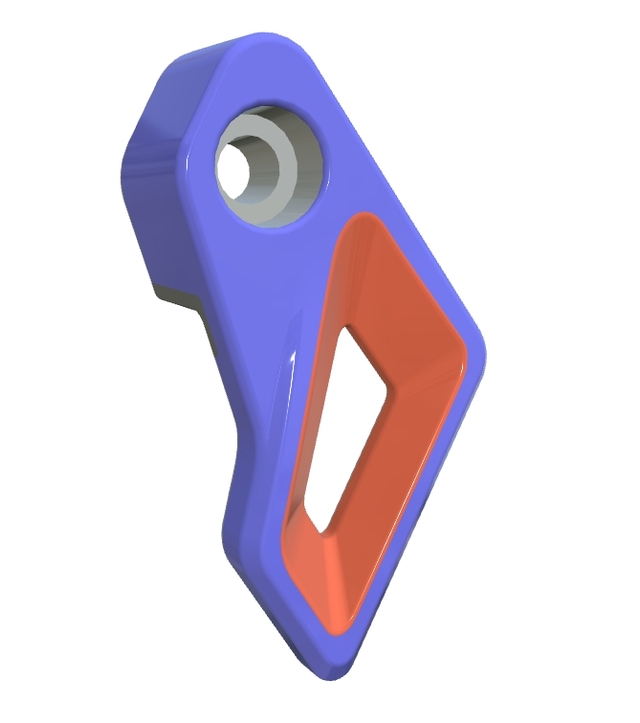
Overmolding Innovations: Unveiling the HexAlign Bracket
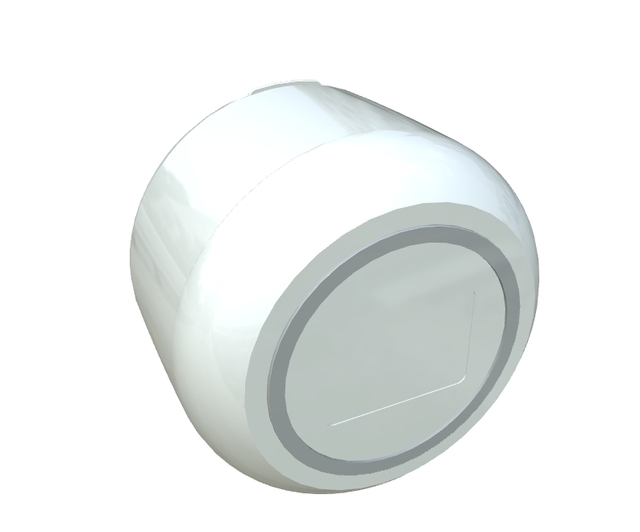
Overmolding Techniques: Revolutionizing Smart Lock Design
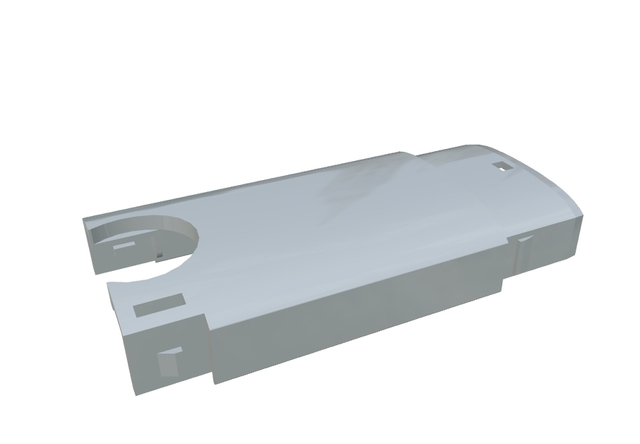
Unlocking the Overmolding Process: Techniques & Benefits
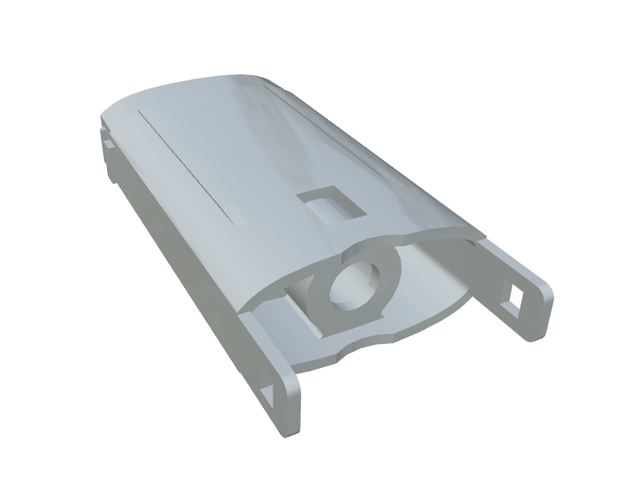
Mastering the Overmolding Process for Enhanced Products
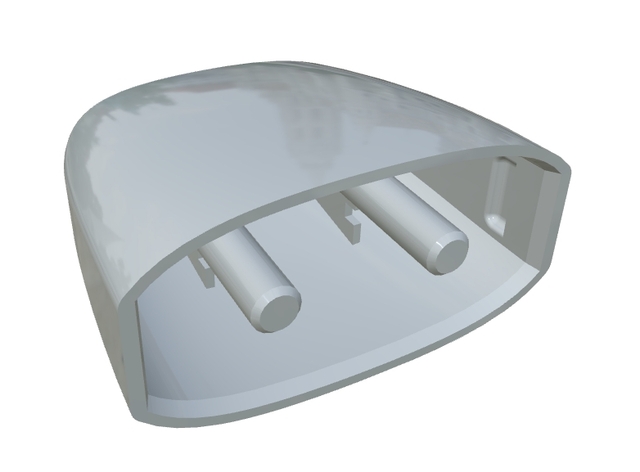
Overmolding Process: Techniques, Materials & Applications
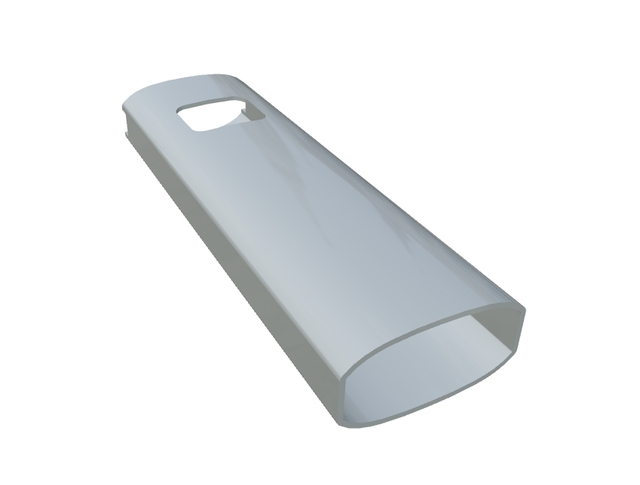
Exploring Advanced Overmolding Techniques in Modern Manufacturing
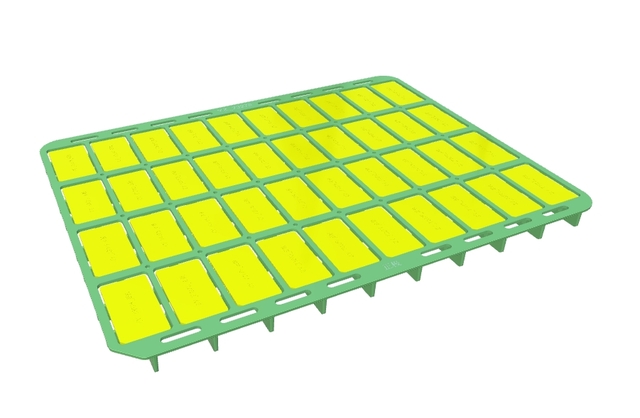
Understanding the Insert Molding Process: Advantages and Applications