밀링은 다양한 모양을 만들 수 있고 다양한 재료에 적합한 주요 처리 기술입니다. 작동 방법은 부품에서 과도한 재료를 제거하는 것입니다. 밀링에서 페이스 밀링과 주변 밀링 사이의 선택은 프로세스 효율성에 큰 영향을 미칩니다. 올바른 것을 선택하면 전체 처리 프로세스와 제어 비용에 걸쳐 높은 정밀도를 달성 할 수 있습니다. 다음으로, 우리는 자신의 처리 요구에 따라 가장 적합한 밀링 프로세스를 선택하는 데 도움이되는이 두 처리 방법의 차이점에 대해 자세히 설명합니다.
.페이스 밀링이란 무엇입니까?
얼굴 밀링은 밀링 커터의 끝면의 최첨단 를 사용하는 밀링 과정입니다. 실제 생산에서는 주로 공작 기계 워크 벤치, 평평한 플레이트 및베이스와 같은 더 큰 평면을 처리하는 데 사용됩니다. 페이스 밀링은 절단력이 대부분 축 방향을 따라 전달된다는 명백한 특징을 가지고 있습니다. 효율적인 거칠거나 미세한 마무리에 관계없이 할 수 있습니다.
페이스 밀링의 주요 특징
- 도구 유형 : 얼굴 밀링 커터를 사용합니다.
- 절단 방법 : 메인 절단은 끝면 절단 가장자리에 의해 수행됩니다. 이 방법은 특히 큰 평면의 처리에 적합합니다.
- 처리 장점 : 재료를 빠르게 제거하고 공작물 표면을 매우 평평하게 처리 할 수 있습니다.
- 적용 가능한 재료 : 강철 재료 , 주철, Alminum alloy alloy and and and Comploate allominum 재료. 가공.
얼굴 밀링은 어떻게 작동합니까?
페이스 밀링의 기본 워크 플로우
- 도구 설치 : 밀링 머신의 스핀들에 얼굴 밀링 커터를 설치하고 도구가 단단히 설치되어 회전 할 때 흔들리지 않도록하십시오.
- 공작물 고정 : 공작물을 워크 벤치에서 단단히 처리 할 공작물을 처리하는 동안 공작물이 움직이지 않도록하여 처리 정확도를 보장합니다.
- 절단 모션 : ① ① ① 핀들 회전 (절단 동작) : 밀링 커터는 고속으로 회전하고 끝면의 블레이드가 공작물을 자르기 시작합니다. feed 모션 (x/y/z 축 운동) : 공작물 또는 도구는 사전 설정 경로를 따라 이동하여 전체 표면을 천천히 덮을 수 있습니다.
- 칩 형성 : 블레이드가 공작물 재료를 자르면 칩이 생성 되고이 칩은 처리 영역에서 배출됩니다.
- 표면 형성 : 여러 공구 경로 또는 다른 미세 밀링의 처리를 통해 평평하고 부드러운 처리 표면을 마지막에 얻을 수 있습니다 .
페이스 밀링의 절단 방법
<테이블 스타일 = "Border-Collapse : 붕괴; 너비 : 100%; 경계 색상 : #000000;" Border = "1">주변 밀링이란 무엇입니까?
.주변 밀링의 주요 특징
- 도구 유형 : 엔드 밀, 원통형 밀링 커터 등 사용을 사용하며 절단 가장자리는 도구의 둘레에 분포됩니다.
- 절단 방법 : 원주 절단 가장자리는 메인 커팅을 수행하며 윤곽 및 측면 벽 처리에 적합합니다.
- 처리 장점 : 고정밀 윤곽과 우수한 표면 품질 (RA 0.4 ~ 1.6μm)을 얻을 수 있습니다.
- 적용 가능한 재료 : 스틸, 알루미늄 합금, 티타늄 합금, 복합 재료 등
주변 밀링은 어떻게 작동합니까?
Peripheral Milling은 회전을 사용합니다. 및 밀링 커터의 원주 절단 가장자리의 피드 동작을 위해 공작물 자재를 점차적으로 제거하여 원하는 윤곽 또는 그루브를 형성합니다.
.주변 밀링의 기본 작업 과정
- 도구 설치 : 엔드 밀이 밀링 머신 또는 가공 센터의 스핀들에 설치되어 도구의 방사형 런아웃이 최소화되도록합니다.
- 공작물 고정 : 공작물이 작업대에 단단히 고정되어 처리 중 진동 또는 변위를 방지합니다.
- 절단 모션 : 스핀들 회전 (절단 동작) : 밀링 커터는 고속으로 회전하고 원주 절단 가장자리는 공작물을 절단합니다.
- 칩 형성 : 원주 가장자리는 재료를 지속적으로 절단하고 칩이 공구의 나선형 홈을 따라 배출됩니다.
- 윤곽선 형성 : 원하는 모양과 크기는 공구 경로를 정확하게 제어하여 얻습니다.
말초 밀링의 절단 방법
<테이블 스타일 = "너비 : 100%; 높이 : 413.984px; 경계-콜라 랩스 : 붕괴; 경계 컬러 : #000000;" Border = "1">부분 원주 밀링
얼굴 밀링 대 주변 밀링 : 차이점은 무엇입니까?
아래는 6 가지 주요 영역에서 얼굴 밀링과 주변 밀링의 자세한 비교입니다 :
<공구 방향 차이
<테이블 스타일 = "Border-Collapse : 붕괴; 너비 : 100%; 경계 색상 : #000000;" Border = "1"> 기술적 설명 :
말초 밀링의 방사형 힘은 도구 처짐을 쉽게 유발할 수 있으며, 강화 공구 홀더 (예 : 유압 도구 홀더)가 필요합니다. 페이스 밀링의 축 방향 힘은 공작 기계 가이드 레일에 더 균일 한 하중을 가지고 있습니다.
<재료 제거 메커니즘
<테이블 스타일 = "너비 : 100%; 높이 : 167.078px; 테두리-콜라 랩스 : 붕괴; 경계 컬러 : #000000;" Border = "1"> 사례 데이터 :
45# 스틸을 처리 할 때 φ50mm 페이스 밀링 커터 (8 블레이드)의 금속 제거 속도는 φ20mm 엔드 밀링 커터 (4 블레이드)의 4-6 배입니다.
<일반적인 응용 시나리오
<테이블 스타일 = "너비 : 100%; 높이 : 167.078px; 테두리-콜라 랩스 : 붕괴; 경계 컬러 : #000000;" Border = "1"> 산업 분배 :
얼굴 밀링은 자동차 산업에서 60%를 차지합니다.
<표면 처리 능력
<테이블 스타일 = "Border-Collapse : 붕괴; 너비 : 100%; 경계 색상 : #000000;" Border = "1"> 측정 데이터 :
마무리를 위해 φ12mm 볼 엔드 밀링 커터를 사용할 때 주변 밀링은 RA 0.2μm 미러 효과를 얻을 수 있습니다.
<공구 마모 및 설정
<테이블 스타일 = "Border-Collapse : 붕괴; 너비 : 100%; 경계 색상 : #000000;" Border = "1"> 유지 보수 팁 :
처리 시간마다 주변 밀링 도구의 방사형 런아웃을 확인하는 것이 좋습니다 (<0.01mm이어야 함)
<도구 설계 차이
<테이블 스타일 = "Border-Collapse : 붕괴; 너비 : 100%; 경계 색상 : #000000;" Border = "1"> 프론티어 기술 :
최신 주변 장치 밀링 커터는 5 축 그라인딩 및 형성 기술을 채택하여 ± 2μm 의 최첨단 프로파일 정확도를 달성합니다. 페이스 밀링 커터는 내부 냉각 오일 구멍이있는 세라믹 블레이드를 개발했습니다.
페이스 밀링을 선택할 때?
다음 점은 얼굴 밀링을 선택할 때를 이해하는 데 도움이됩니다 . 다음으로, 우리는 이러한 측면들을 자세하게 논의 할 것입니다.
1. 평면 가공을위한 선호되는 솔루션
고밀도 평면을 만들 때 얼굴 밀링은 대체 할 수없는 기술적 이점을 제공합니다 . 공구 축의 가공 된 표면에 수직 특성은 큰 판금 및 블록 워크 피스를 처리하는 데 특히 적합합니다. 멀티 엣지 도구의 공동 작업 절단을 통해 공작물 표면의 불균일성을 효과적으로 제거 할 수 있으며 전형적인 가공 정확도는 평평성이 0.02mm/m에 도달 할 수 있습니다. 이 처리 방법은 특히 기계 공구 와 같은 주요 구성 요소의 평면 가공에서 특히 두드러집니다. 가이드 레일 표면 및 유압 밸브 블록.
2. 효율적인 재료 제거 기능
Face Milling은 고유 한 절단 형상으로 인해 재료 제거 속도 (MRR) 측면에서 상당한 이점을 제공합니다.
- 접촉 영역은 주변 밀링의 접촉 영역보다 3-5 배 더 클 수 있습니다
- 전형적인 거친 매개 변수 : 컷 3-5mm의 축 깊이, 도구 직경의 50-80% 컷의 방사형 깊이
- 주철 가공의 금속 제거 속도는 800 cm³/min 에 도달 할 수 있습니다.
이 고효율은 빈 청소, 용접 정렬 및 거친 작업을 주조하여 후속 마무리를위한 토대를 마련하는 데 이상적입니다.
3. 간단한 프로세스 구현
페이스 밀링 공정의 단순성은 다음에 반영됩니다.
- 클램핑 포지셔닝은 도구가 공작물 표면에 수직이어야합니다
- 복잡한 각도 조정이 필요하지 않습니다
- 전형적인 Makeready 시간은 주변 밀링보다 40% 짧습니다
이 기능은 자동차 엔진 블록의 평평한 가공과 같은 대량 생산 시나리오에 특히 적합하며, 이는 생산 라인의 사이클 시간 효율을 크게 향상시킬 수 있습니다.
4. 우수한 표면 일관성
페이스 밀링의 표면 품질 관리 이점 :
- 멀티 엣지 시너지 효과는 전체 가공 된 표면에 걸쳐 균일 성을 보장합니다
- 옵션 와이퍼 삽입 설계는 RA0.8μm 마감 처리를 달성합니다
- 크로스 컷 텍스처는 표면 하중 기반 성능을 향상시킵니다
이 특성은 정밀 플랫 플레이트 및 광학 테이블과 같은 균일 한 표면 특성이 필요한 워크 피스 가공에 특히 가치가 있습니다.
기술의 확장 된 적용
- Modern Face Milling Technology는 다양한 고급 응용 프로그램을 개발했습니다.
- 높은 피드 밀링 (HFR) : 최대 3000mm/min 피드 속도
- 컷 밀링의 가변 깊이 : 공작물 변형을 보상하기 위해 컷 깊이를 자동으로 조정합니다
- 지능형 페이스 밀링 : 통합 진동 모니터링은 매개 변수를 실시간으로 최적화합니다
선택에 대한 제안 :
주변 밀링을 선택할 때?
기계식 처리 의 필드에서는 주변 밀링 공정을 언제 사용 해야하는지 아는 것이 매우 중요합니다. 다음은 관련 영향 요인을 깊이 탐색 할 것입니다.
1. 복잡한 윤곽 처리의 유의미한 장점
CNC-Milling은 복잡한 윤곽 처리 작업에 특히 적합하며 . 이 도구는 원형 절단 방법을 사용합니다. 일반적으로 금속 부분의 표면에서 180 도의 각도로 사용됩니다. 이 고유 한 절단 각도는 복잡한 부분의 처리에 더 높은 정밀도와 정확도를 가져오고 기어 절단 및 스레드 밀링과 같은 많은 응용 시나리오에서 중요한 역할을합니다.
2. 깊은 그루브 및 복잡한 윤곽선의 효율적인 처리
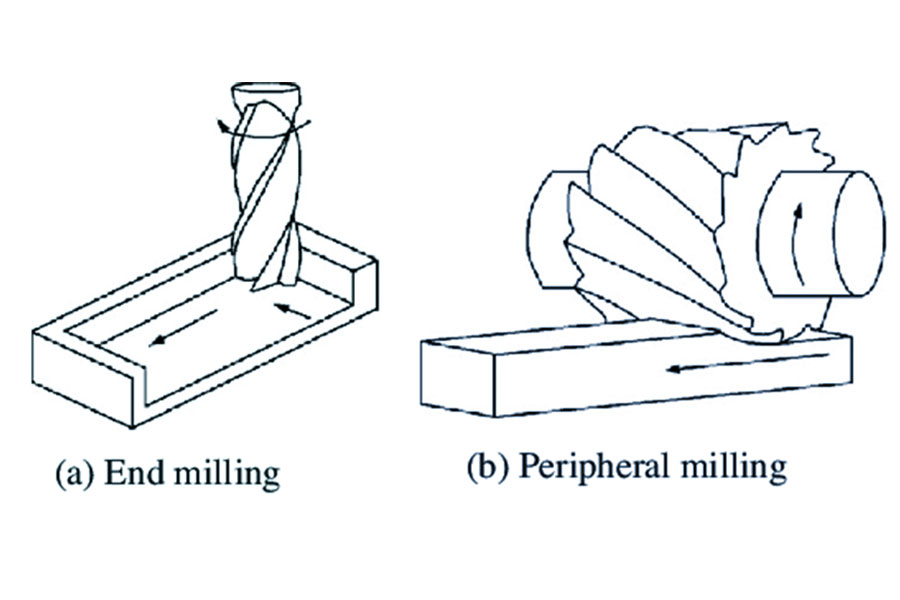
얼굴 및 주변 밀링에 대한 정밀 제조를 선택하는 이유는 무엇입니까?
공장에서는 모든 종류의 고급 기술 및 장비를 사용할 수 있습니다. 소규모 배치 맞춤형 생산이든 대규모 배치 생산이든, 우리는이를 침착하게 다루고 처리 작업을 정확하고 효율적으로 완료 할 수 있습니다. 생산 공정 전반에 걸쳐, 우리는 항상 품질의 결론을 준수하고 품질을 희생하지 않습니다. 동시에, 우리는 또한 각 프로젝트의 특정 요구에 따라 경제적이고 효율적인 솔루션을 조정하여 고객이 제품의 품질을 보장하면서 비용을 합리적으로 통제 할 수 있도록 도와줍니다.
요약
기계식 처리 분야에서 정확한 기술 선택은 제품 품질 및 생산 효율과 직접 관련이 있습니다. 매끄럽거나 평평한 표면에 집중해야 할 필요성에 직면 할 때 얼굴 밀링은 의심 할 여지없이 최선의 선택입니다 ; 프로젝트에 깊은 절단, 그루브 및 기타 작업이 포함되면 주변 밀링은 필수 불가결합니다. 의사 결정 프로세스에서 재료 유형, 원하는 표면 품질, 공구 가용성, 생산 규모, 처리 속도 및 비용과 같은 많은 요소를 완전히 고려해야합니다.
기계식 처리 산업의 지속적인 혁신으로, 최첨단 정보를 적시에 파악하고 실용적인 기술을 적용하는 것은 생산 효율성을 향상시키는 데 큰 의미가 있습니다. 예를 들어, 얼굴 밀링 기술을 예로 들어, 원칙과 응용 프로그램에 대한 깊은 이해는 기업에게 큰 이점을 가져올 수 있습니다. 이러한 프로세스를 깊이 파고 들고 신뢰할 수있는 장비를 찾고자하는 회사의 경우 ls 정밀 제조는 이상적인 파트너입니다.
페이스 밀링 및 주변 밀링 분야에 깊은 축적을 통해 ls는 업계의 최고 표준을 충족하는 고품질 제품을 제공 할뿐만 아니라 회사의 최고의 자원을 제공 할 수있는 귀중한 자원을 제공 할 수있을뿐만 아니라 기계 트랙에서 꾸준히 움직일 수 있도록 도와줍니다.
이 페이지의 내용은 정보 제공 목적으로 만 사용됩니다. ls series 어떤 종류의 표현 또는 보증도 명시 적 또는 묵시적에 대한 표현 또는 보증은 정보의 정확성, 완전성 또는 중요성에 대해 이루어지지 않습니다. 성능 매개 변수, 기하학적 공차, 특정 설계 기능, 재료 품질 및 유형 또는 유형 또는 제조업체가 Longsheng 네트워크를 통해 제공 할 것이라고 추론해서는 안됩니다. 이것은 구매자의 책임입니다 부품에 대한 견적을 요청하십시오 이 부분에 대한 특정 요구 사항을 결정하려면 더 많은 정보를 연락하십시오 면책 조항
LS 팀
ls는 업계 최고의 회사입니다 맞춤형 제조 솔루션에 중점을 둡니다. 우리는 5,000 명 이상의 고객에게 서비스를 제공 한 20 년이 넘는 경험을 통해 높은 정밀도 cnc machining , Seete Metal Fabrication , 3d printing , 주입 곰팡이 , 금속 스탬핑 "및 다른 하나의 스탬핑 서비스. 1. 얼굴 밀링 및 주변 밀링을 동시에 수행 할 수 있습니까? 예, 현대식 가공 밀링 커터 (예 : 어깨 밀링 커터 또는 모듈 식 밀링 커터)는 특수 설계를 통해 페이스 밀링 및 주변 밀링을 달성 할 수 있습니다. 이러한 절단기는 일반적으로 평면 밀링의 끝면에 마무리 인서트를, 윤곽 처리를 위해 둘레에 거친 인서트를 배열합니다. 예를 들어, Sandvik Coromant의 Coromill 390 시리즈는 하나의 클램핑에서 90 ° 어깨 얼굴 및 측면 벽 처리를 완료 할 수 있으며, 이는 전통적인 프로세스와 비교하여 처리 시간을 30% 이상 단축 할 수 있습니다. 배치 부품의 효율적인 처리에 특히 적합하지만, 두 개의 처리 모드의 기계적 특성에 따라 절단 매개 변수를 손상되고 최적화해야한다는 점에 유의해야합니다. 2. 얇은 벽 부품에 더 적합한 밀링 방법은 무엇입니까? 주변 밀링, 특히 다운 밀링은 방사형 절단력을 낮은 수준 (일반적으로 얼굴 밀링보다 40-60% 낮음) 및 작은 절단 깊이 (AE < 0.5mm)와 고속 전략에서 진동을 억제 할 수 있기 때문에 얇은 벽 부품 처리에 더 적합합니다. 예를 들어, 항공 알루미늄 합금의 얇은 벽 오두막을 가공 할 때, φ10mm 얇은 넥 엔드 밀로 말초 밀링은 ± 0.05mm 이내의 벽 두께 오차를 제어 할 수있는 반면, 얼굴 밀링의 축 방향 힘은 쉽게 0.1mm 이상의 탄성 변형으로 이어질 수 있습니다. 강성이 열악한 얇은 벽 티타늄 합금 부품의 경우 절단력을 더욱 줄이려면 축 층 주변 밀링 (zig-zag path)이 필요합니다. 3. 페이스 밀링으로 표면 마감이 얼마나 높은가? 이상적인 조건 에서면 페이스 밀링의 표면 마감은 최대 0.4μm에 도달 할 수 있으며, 이는 세 가지 주요 조건을 충족해야합니다. 와이퍼 모서리 (예 : ISCAR의 F3S 시리즈)가있는 미세한 밀링 삽입물 사용, 고도도 방사형 도구 (스핀들 방사형 런아웃 <0.005mm), 미니 론 피드 (피드 03.05mm)와 협력하는 것입니다. 예를 들어, 주철 기계 공구 가이드를 가공 할 때, PVD 코팅 인서트, 0.2mm 와이퍼 가장자리 중첩 및 800m/분 절단 속도의 조합은 RA 0.5μm의 미러 효과를 달성 할 수 있지만,이 높은 유리한 처리는 공구 수명의 약 25%를 희생한다는 점에 유의해야합니다. 4. 말초 밀링의 도구 수명은 일반적으로 얼굴 밀링의 도구 수명입니까? 도구 수명 비교는 단순히 결론을 내릴 수 없습니다. 예를 들어, 경화 강철 (HRC55) 가공 할 때, 주변 밀링의 작은 절단 너비 (AE = 0.1D) 전략은 공구 수명이 120 분에 도달 할 수 있으며, 40 분의 페이스 밀링 커터를 초과 할 수 있습니다. 그러나 알루미늄 합금의 고속 가공에서, 얼굴 밀링 커터의 수명은 절단 하중의 멀티 엣지 공유로 인해 주변 밀링 커터보다 2-3 배 높다. 주요 영향 요인은 다음과 같습니다. 절단 열 분포 (말초 밀링의 도구 팁 온도가 높음), 칩 제거의 어려움 (얼굴 밀링의 닫힌 칩은 보조 절단이 발생하기 쉽습니다) 및 최신 코팅 기술 (얼굴 밀링 삽입의 Alcrn 코팅이 더 나은 내열성이 향상됨). 실제 생산에서는 절단력 모니터링 및 공구 마모 분석을 통해 동적 최적화가 필요합니다.
우리의 공장에는 100 개가 넘는 최첨단 5 축 가공 센터가 장착되어 있으며 ISO 9001 : 2015 인증이 있습니다. 우리는 전 세계 150 개국 이상의 고객에게 빠르고 효율적이며 고품질 제조 솔루션을 제공합니다. 볼륨 저용량이 적거나 대량 사용자 정의이든 24 시간 이내에 가장 빠른 배송으로 귀하의 요구를 충족시킬 수 있습니다. ls 기술을 선택하십시오.
FAQS
자원