Selective laser sintering (SLS) has emerged as a groundbreaking technology in the realm of additive manufacturing. Often referred to as SLS technology, this method relies on a high-powered laser to fuse small particles of plastic, metal, ceramic, or glass powder into a solid, three-dimensional shape. Selective laser sintering is a compelling advancement because it allows for the creation of complex and intricate designs without the need for traditional machining or tooling.
The laser sintering process begins with a 3D design, set up in a computer-aided design (CAD) program, which is then translated into the SLS machine. The material — typically in powder form — is spread evenly across a build platform, and a CO2 laser selectively fuses each layer into a cross-section of the object. Successive layers are stacked and bonded until the final product emerges. This layer-by-layer approach provides not only unparalleled precision but also the flexibility to experiment with innovative geometries that were previously impossible.
One of the major advantages of selective laser sintering is its applicability to a wide range of SLS materials, enabling its use in diverse industries. Automotive and aerospace entities often utilize SLS for producing lightweight parts that boast remarkable strength and stability. Medical sectors also benefit from this process by creating customized implants and prosthetics. Meanwhile, consumer electronics manufacturers find value in the precision and reliability SLS offers in crafting complex internal components. Thus, SLS applications stretch across various fields, advancing the capabilities and efficiencies of modern manufacturing.
LS Hardware Tech Co., Ltd is renowned for its innovative manufacturing solutions, standing at the forefront of industries that require high-precision parts. With over 20 years of expertise led by founder Nick Zhang and his adept team of engineers, LS is well-versed in employing cutting-edge technologies like selective laser sintering to meet the versatile demands of their clients. Their commitment to quality and efficiency is evident in their partnerships, which span more than 150 countries worldwide.
In their continuous pursuit of excellence, LS Hardware Tech Co., Ltd introduces the Enhanced Flow Adapter, a testament to their ingenuity and craftsmanship. This product, carefully crafted with durability in mind, offers seamless compatibility across various pipe systems. Characterized by its sleek, white finish, the adapter resists corrosion and wear, ensuring long-lasting reliability for both residential and commercial plumbing applications. One of its standout features is the specialized threading design, which simplifies attachment and ensures a secure fit, reducing the chance of leaks. Additionally, the inset of the adapter optimizes flow rate management, thus improving the plumbing system's overall efficiency.
Such innovations by LS are examples of practical applications of additive manufacturing SLS. The versatility of SLS technology empowers businesses to enhance product functionality while simultaneously achieving modern aesthetics. The ease of making prototypes and quick-cycling iterations with 3D printing SLS continues to change the game for manufacturers who aim to meet elevated consumer demands.
Beyond product development, LS Hardware Tech Co., Ltd's dedication to sustainability is illustrated by their strategic use of resources. By minimizing material waste and optimizing production lines, the company maximizes not only the efficiency of the laser sintering process but also the positive impacts on the environment. This aligns with LS's broader mission to transform the landscape of manufacturing by continuously integrating state-of-the-art methods with environmentally responsible practices.
In sum, selective laser sintering remains a pivotal tool for companies like LS Hardware Tech Co., Ltd as they forge ahead in precision component manufacturing. The technology's ability to swiftly and accurately produce complex, robust parts positions businesses to meet the perpetual pace of industrial innovation. Through leveraging the flexibility and strength of SLS applications, enterprises can propel their offerings from mere concepts to tangible products efficiently and sustainably, championing new standards in the realms of additive manufacturing.
Selective Laser Sintering: Revolutionizing Additive Manufacturing
Get Latest Price >
Label | Value |
---|---|
Brand | LS Custom Parts Manufacturers |
Customization Service | 3D Printing Services, Stereolithography, Selective Laser Sintering, Fused Deposition Modeling, Multi Jet Fusion |
Drawing format | 2D/(PDF/CAD)、3D(IGES/STEP/GLB) |
Material Capabilities | Aluminum、Brass、Bronze、Copper、Hardened Metals、Precious Metals、Stainless Steel、Alloys、TPR |
Sample | Free |
Supply Ability | 100000 Pieces Per Day |
Surface Finish | Customized Finishing |
Thickness | Customized Thickness |
Type | Broaching/Drilling/Etching / Chemical Machining/Laser Machining/Milling/Turning/Wire EDM/Rapid Prototyping/Other Machining Services |
Services | CNC Machining,Metal Casting,Injection Molding,Sheet Metal Fabrication,Rapid Prototyping,3D Printing |
Find Similar Products
Contact
Ready to start your next project with LS Manufacturing?
Contact us today to learn more about our services and how we can help you achieve your goals.
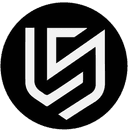
Rapid lead times starting from just 1 business day.
ISO 9001,ISO 14001,IATF 16949 and AS9100D Certification.
Over 100 materials available, with 50+ surface finish options.
Cost-effective mass production.
Order as low as 1 piece.
People who viewed this also viewed
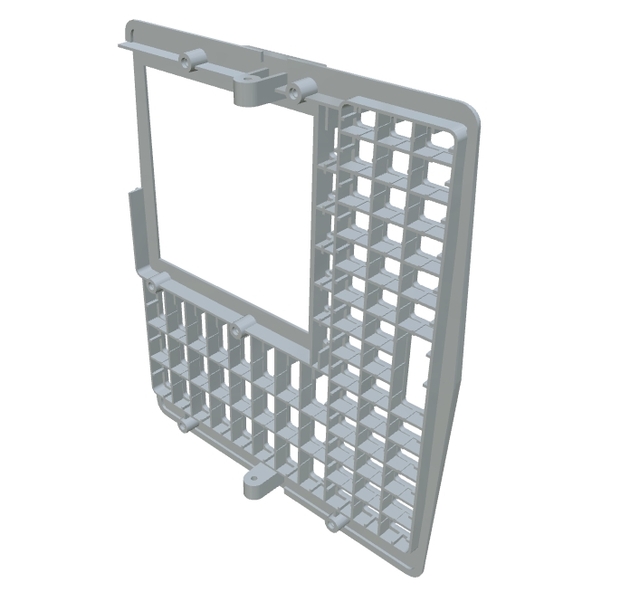
SLS Technology Advancements: Future, Safety, Applications
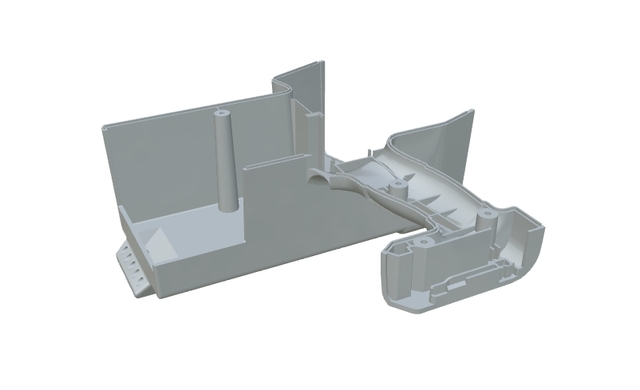
Selective Laser Sintering: Revolutionizing Industrial 3D Printing
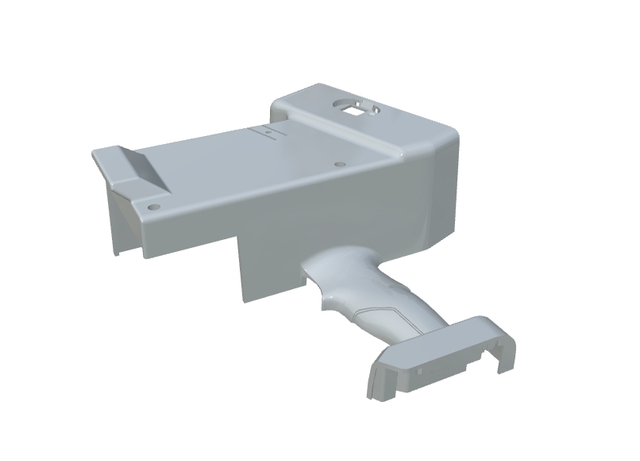
Exploring the Impact of SLS Technology in Modern Manufacturing
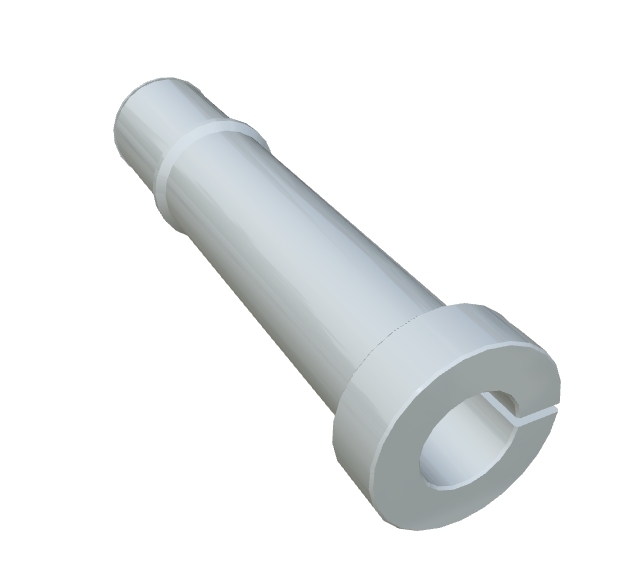
Selective Laser Sintering: Revolutionizing Additive Manufacturing with SLS Technology
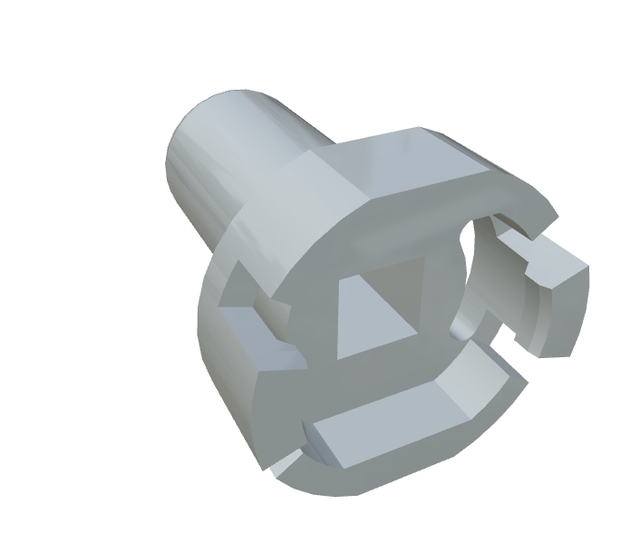
Exploring Selective Laser Sintering: Revolutionizing 3D Printing and Beyond
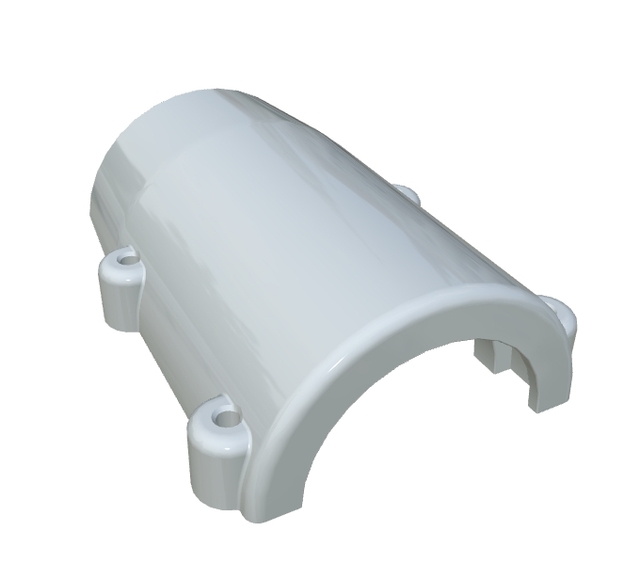
Selective Laser Sintering in Modern Manufacturing
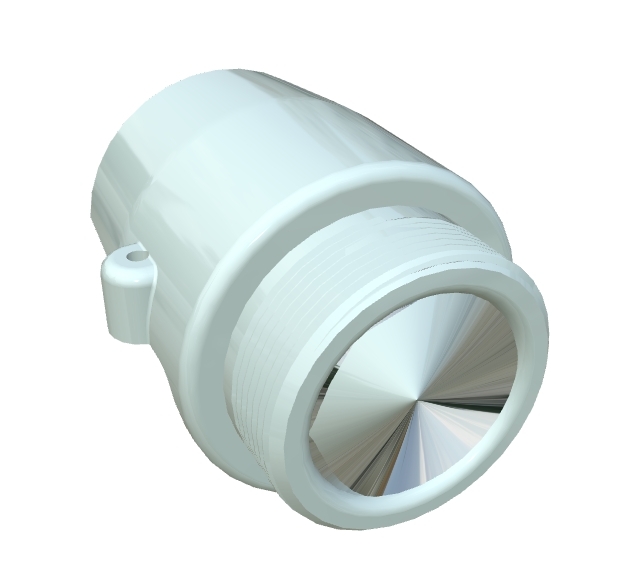
Selective Laser Sintering: Revolutionizing Additive Manufacturing
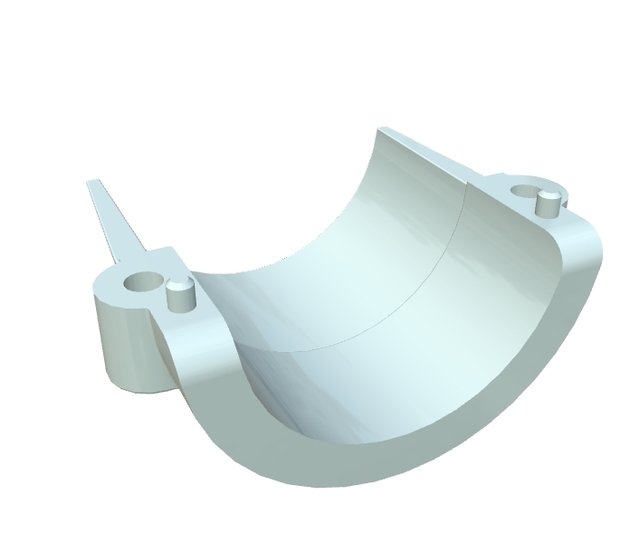
The Innovations of Selective Laser Sintering Process