In the ever-evolving world of manufacturing, one technology stands out as a game changer: **Fused Deposition Modeling (FDM)**. This pioneering 3D printing technique has become a cornerstone in the field of additive manufacturing, providing an unparalleled method for creating complex designs with precision and efficiency. By focusing on the FDM 3D printing process, industries across the globe are transforming their production capabilities, opening up new possibilities in innovation and design.
The benefits of FDM 3D printing are vast, particularly in materials like thermoplastic, which are used extensively due to their flexibility and strength. FDM involves filament extrusion, where the filament is fed through a heated nozzle, melted, and deposited layer by layer to build up the desired object. This method is ideal for industries requiring tailored, high-strength components, such as automotive, aerospace, and even medical devices. **FDM printers** have become integral tools in these industries, allowing companies to design intricate parts that meet specific performance criteria.
The versatility of FDM is further evidenced by its compatibility with a wide variety of thermoplastic materials, each offering unique properties that meet specific industry requirements. LS Hardware Tech Co., Ltd exemplifies the cutting-edge application of FDM technology. As a leading provider of precision-engineered parts, LS combines its decades of expertise with advanced manufacturing processes to power ground-breaking product solutions like the Structural Support Plate.
The Structural Support Plate is an embodiment of innovation and efficiency. Manufactured from high-grade aluminum alloy, this component integrates modern engineering with practical application. Addressing critical needs across sectors ranging from aerospace to heavy machinery, it boasts an optimized strength-to-weight ratio—thanks to its minimalist design. Such a design approach not only reduces unnecessary bulk but also maintains strong structural integrity. This makes it ideal for demanding environments where every gram of weight is crucial, such as in aerospace applications.
Adding to its functionality, the Structural Support Plate comes with strategically placed cut-outs to further reduce weight without compromising on its supporting capabilities. Furthermore, its sleek metallic finish enhances both its durability and aesthetic appeal, ensuring it seamlessly integrates into multiple assembly configurations. With pre-drilled holes, the plate offers versatile installation options, adding to its adaptability across numerous industrial applications.
Founded by Mr. Nick Zhang, LS Hardware Tech Co., Ltd leverages over two decades of industry experience to deliver products that meet and exceed the highest standards. The company's standout promise stems from the expertise of Nick and his skilled team of engineers, who have consistently delivered efficient solutions to a diverse clientele exceeding 5,000. Together, they have built a state-of-the-art facility equipped with over 100 high-end machining centers. This infrastructure positions LS at the forefront of 3D printing technology, making them a trusted partner for industries globally.
Moreover, LS is ISO 9001:2015 certified, underscoring its commitment to quality and reliability. Their extensive suite of services caters to the production of high-precision parts, from prototypes to mass production. The company serves industries like automotive, consumer electronics, and industrial equipment, maintaining a continuous thrust towards innovation and enhancement of their manufacturing processes.
By utilizing FDM technology and their seasoned expertise, LS Hardware Tech Co., Ltd epitomizes the marriage of form and function, enabling businesses to meet the challenges of modern engineering head-on. Their mission, as envisioned by Mr. Zhang, is to empower clients to bring their ideas to fruition with innovative manufacturing solutions, continuously adapting to the ever-changing technological landscape. Through meticulous craftsmanship and visionary foresight, they are paving the way for the manufacturing industry of tomorrow.
In essence, fused deposition modeling is more than just a printing method; it is a catalyst for innovation. As FDM aligns with the broader spectrum of 3D printing technologies, the opportunities it offers are immense. From reducing costs and production times to advancing the functional capabilities of products, the ripple effects of this technology are felt across the spectrum of modern manufacturing, influencing how companies like LS Hardware Tech Co., Ltd shape future solutions to meet emerging demands.
Exploring Fused Deposition Modeling in Modern Manufacturing
Get Latest Price >
Label | Value |
---|---|
Brand | LS Custom Parts Manufacturers |
Customization Service | 3D Printing Services, Stereolithography, Selective Laser Sintering, Fused Deposition Modeling, Multi Jet Fusion |
Drawing format | 2D/(PDF/CAD)、3D(IGES/STEP/GLB) |
Material Capabilities | Aluminum、Brass、Bronze、Copper、Hardened Metals、Precious Metals、Stainless Steel、Alloys、TPR |
Sample | Free |
Supply Ability | 100000 Pieces Per Day |
Surface Finish | Customized Finishing |
Thickness | Customized Thickness |
Type | Broaching/Drilling/Etching / Chemical Machining/Laser Machining/Milling/Turning/Wire EDM/Rapid Prototyping/Other Machining Services |
Services | CNC Machining,Metal Casting,Injection Molding,Sheet Metal Fabrication,Rapid Prototyping,3D Printing |
Find Similar Products
Contact
Ready to start your next project with LS Manufacturing?
Contact us today to learn more about our services and how we can help you achieve your goals.
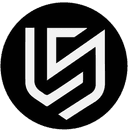
Rapid lead times starting from just 1 business day.
ISO 9001,ISO 14001,IATF 16949 and AS9100D Certification.
Over 100 materials available, with 50+ surface finish options.
Cost-effective mass production.
Order as low as 1 piece.
People who viewed this also viewed
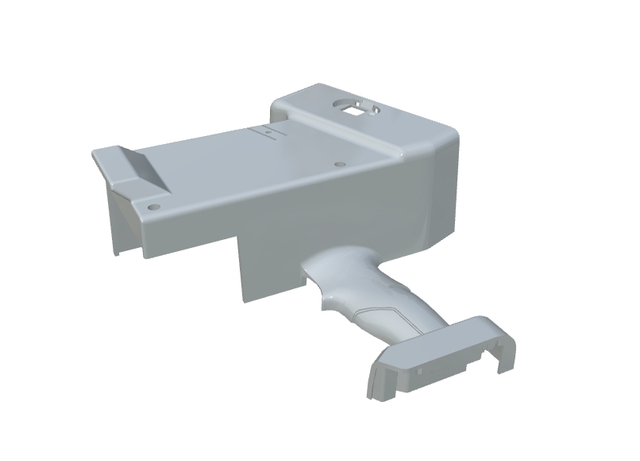
Fused Deposition Modeling: Revolutionizing 3D Printing with FDM Technology
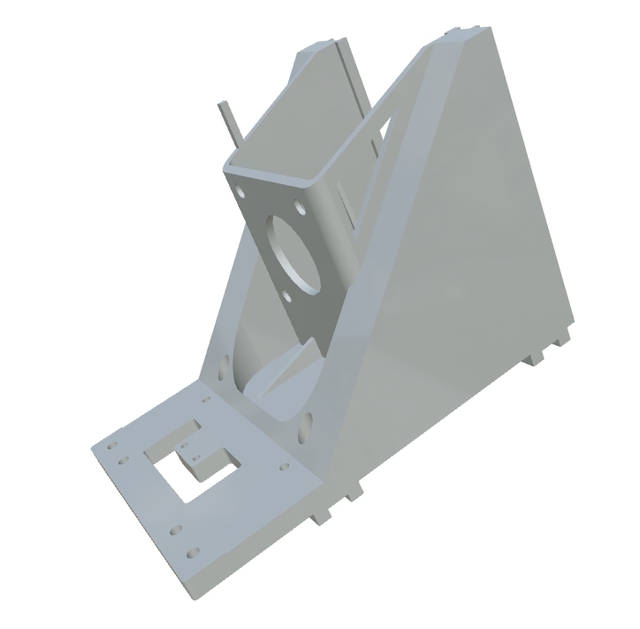
Fused Deposition Modeling: Revolutionizing 3D Printing with FDM Technology
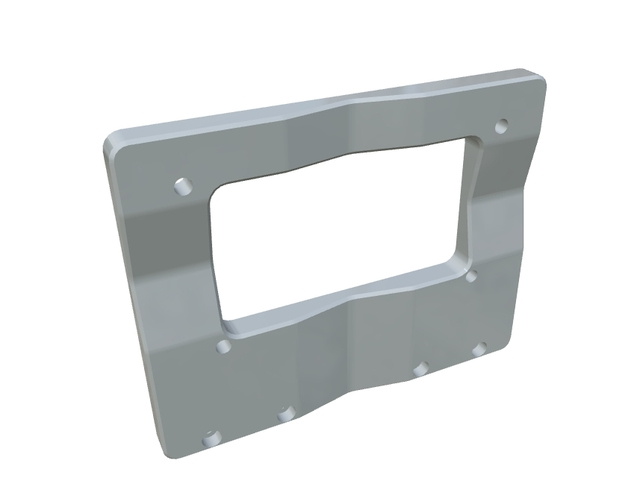
Exploring Fused Deposition Modeling in Modern Manufacturing
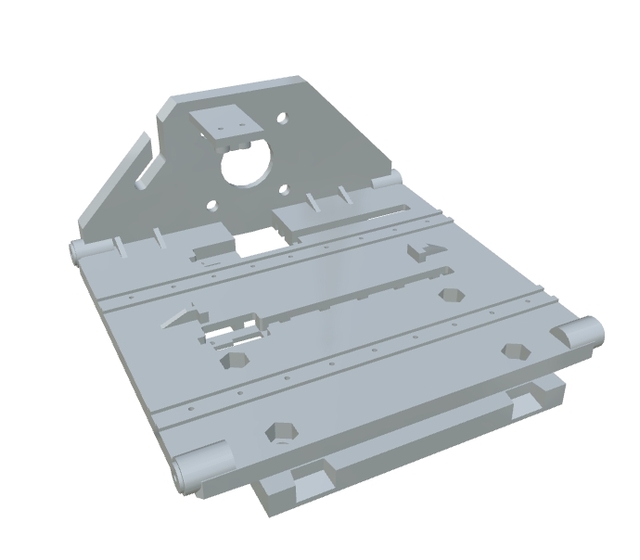
Fused Deposition Modeling: Transforming Additive Manufacturing
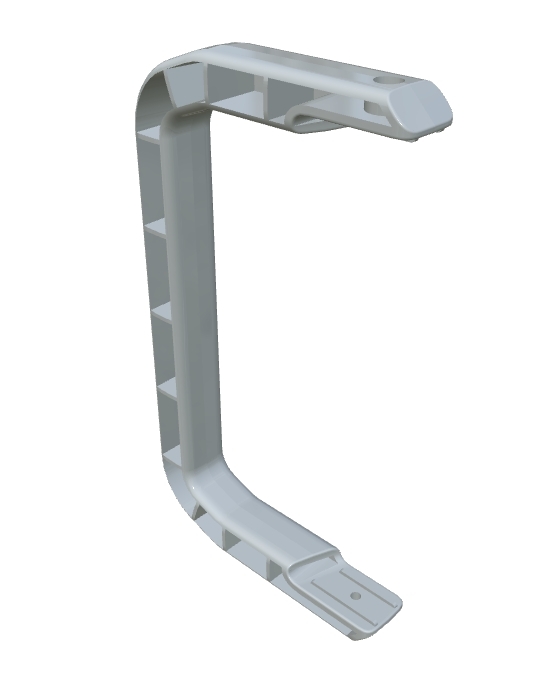
Fused Deposition Modeling: Pioneering 3D Printing Advances
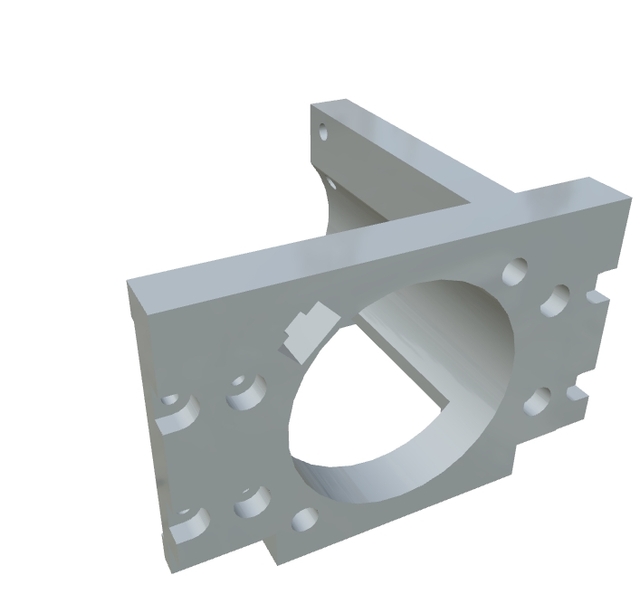
Fused Deposition Modeling: Transforming Manufacturing with LS Hardware Tech Co., Ltd
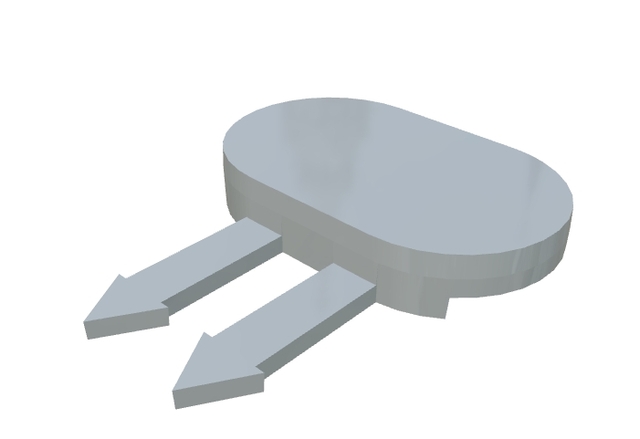
The Future of Connectivity: Fused Deposition Modeling Transforming Streamline Data Relayer
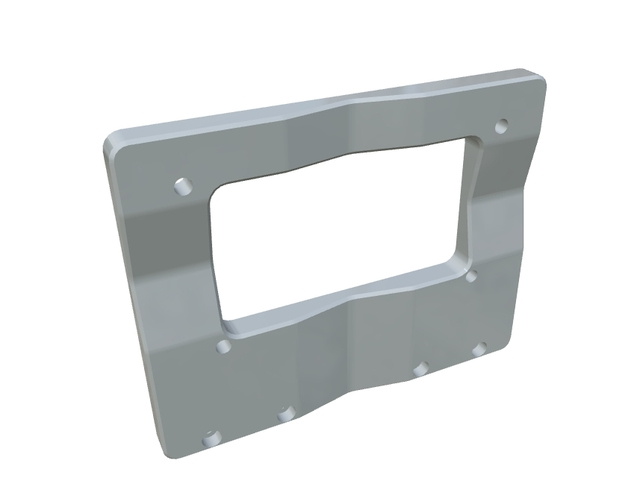
Exploring Additive Manufacturing FDM: Innovation & Applications