The **injection molding process** stands as a cornerstone in modern manufacturing, especially when it comes to creating complex, precise, and durable plastic components. At the heart of this process is the meticulous art of plastic injection molding, a technique that enables manufacturers to produce custom plastic injection molding parts with high efficiency and at scale. Whether you're in need of thermoplastic injection molding for consumer electronics or automotive parts, this method ensures a seamless production cycle from conception to completion.
One of the key advantages of plastic molding services is their ability to fashion injection molded parts that meet the exact specifications required by diverse industries. Companies across the globe capitalize on this to design and develop products that boast high performance and aesthetic appeal. A prime example is the sleek new smart sensor, which embodies the engineering excellence achievable through this process. Featuring a smooth, rounded form factor, this sensor is not only visually striking but also equipped with revolutionary technology that ensures precision and functionality.
The design of the injection molding process involves intricate steps, from rapid prototyping injection molding to injection mold design. This detailed approach allows manufacturers to perfect their products, such as the smart sensor, within a durable and minimalistic casing. The advanced sensor technology, enshrined in a matte finish, is a testament to the harmonious blend of form and function achievable through injection molding. Moreover, strategic design elements like a discreet indicator light and optimized sensitivity and performance slots make it ideal for seamless integration into home or office environments. Such innovative products revolutionize how people interact with their surroundings, promoting efficiency and enhancing style with unparalleled ease.
Understanding Injection Molding Process in Modern Manufacturing
Get Latest Price >
Label | Value |
---|---|
Brand | LS Custom Parts Manufacturers |
Customization Service | Injection Molding, Plastic Injection Molding, Plastic Injection Molds, Insert Molding, Overmolding |
Drawing format | 2D/(PDF/CAD)、3D(IGES/STEP/GLB) |
Material Capabilities | Aluminum、Brass、Bronze、Copper、Hardened Metals、Precious Metals、Stainless Steel、Alloys、TPR |
Sample | Free |
Supply Ability | 100000 Pieces Per Day |
Surface Finish | Customized Finishing |
Thickness | Customized Thickness |
Type | Broaching/Drilling/Etching / Chemical Machining/Laser Machining/Milling/Turning/Wire EDM/Rapid Prototyping/Other Machining Services |
Services | CNC Machining,Metal Casting,Injection Molding,Sheet Metal Fabrication,Rapid Prototyping,3D Printing |
Find Similar Products
Contact
Ready to start your next project with LS Manufacturing?
Contact us today to learn more about our services and how we can help you achieve your goals.
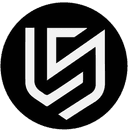
Rapid lead times starting from just 1 business day.
ISO 9001,ISO 14001,IATF 16949 and AS9100D Certification.
Over 100 materials available, with 50+ surface finish options.
Cost-effective mass production.
Order as low as 1 piece.
People who viewed this also viewed
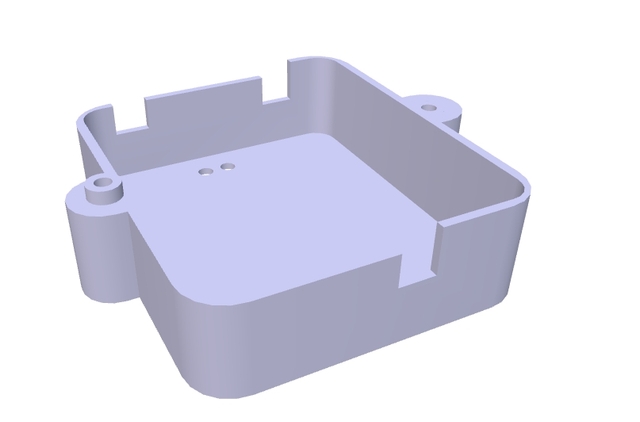
Plastic Injection Molding: Innovation in Electronics Cases
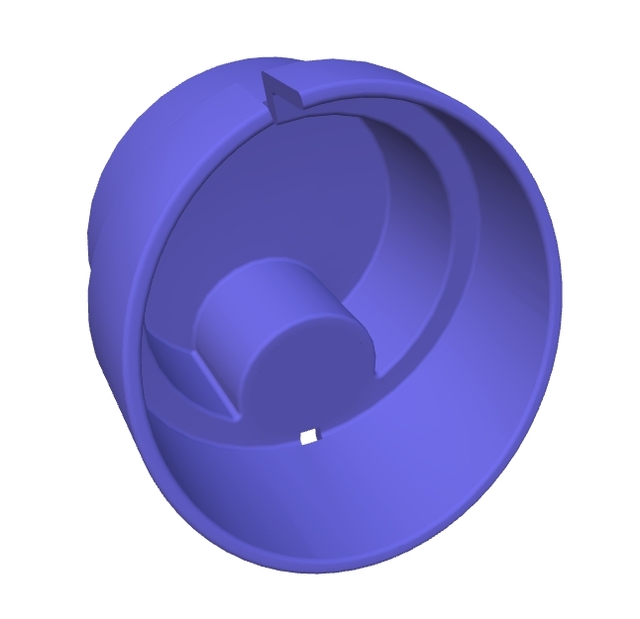
Innovations in Plastic Injection Molding: A Deep Dive into Modern Techniques
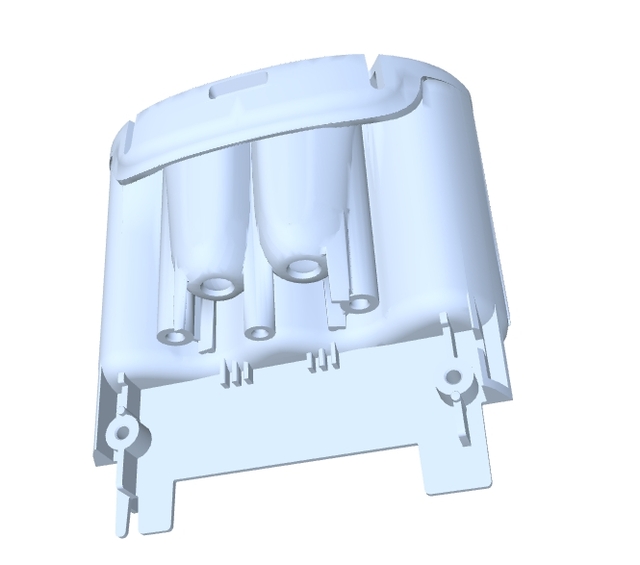
Exploring Plastic Injection Molding in Modern Manufacturing
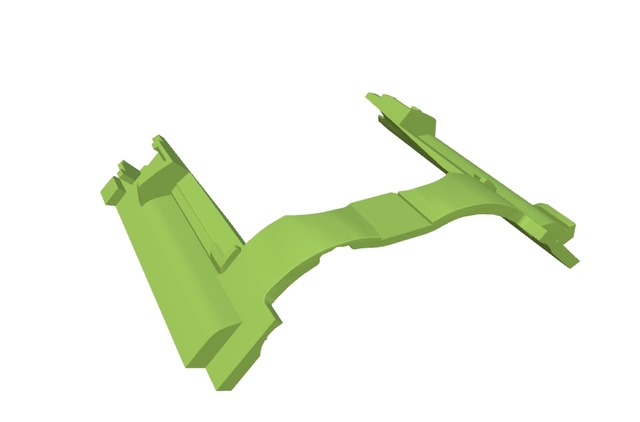
Plastic Injection Molding: Revolutionizing Automotive Components
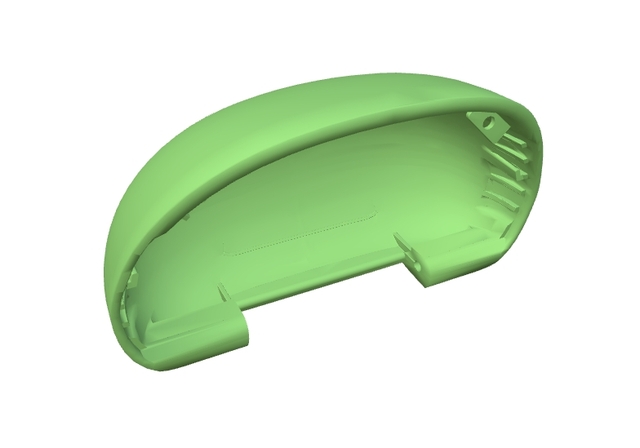
Plastic Injection Molding: The Key to Quality GreenArc Shell
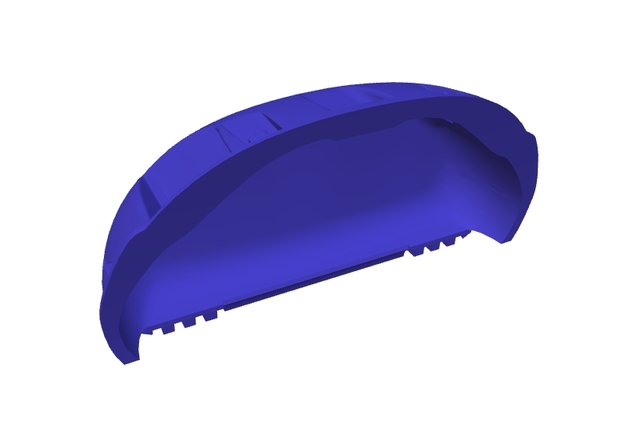
The Future of Plastic Injection Molding: Innovation & Precision
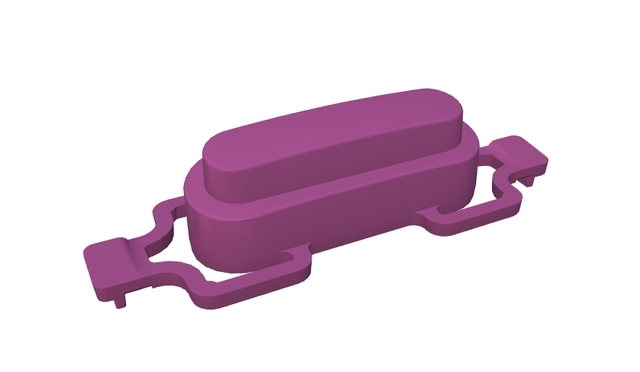
Revolutionizing Production: Plastic Injection Molding Techniques
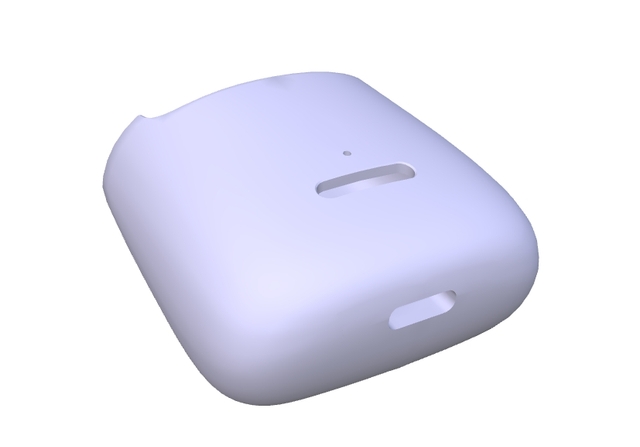
Understanding Injection Molding Process in Modern Manufacturing