Plastic injection molding has become a cornerstone in the manufacturing industry, offering a versatile and efficient process for producing high-quality plastic components. With its ability to create intricate designs and precise measurements, injection molding has revolutionized the way products are crafted, especially in the realm of electronics.
The injection molding process involves injecting molten plastic into a mold where it cools and solidifies into the desired shape. This method is particularly advantageous for producing custom injection molding projects, allowing for bespoke designs tailored to specific needs. The accuracy and consistency of the process make it ideal for creating delicate components like electronics cases, which must fit their contents perfectly while remaining robust enough to withstand daily use.
Investing in plastic manufacturing through injection molding services offers numerous benefits. For instance, our latest innovation in enclosures, the sleek and modern electronics case, exemplifies the potential of injection molded products. Designed with precision and functionality in mind, these cases protect essential electronic components within a durable and lightweight structure. The minimalist, angular design ensures a low profile, while rounded corners prevent snagging and ease handling.
The interior of this custom electronics case is designed with practicality, featuring spacious accommodation for various circuit boards or modules. Thoughtful cutouts exist for cable management and ventilation, ensuring optimal device performance and longevity. Additionally, strategically placed mounting holes facilitate quick and secure installation in industrial applications or DIY custom projects alike.
Moreover, plastic mold design plays a crucial role in the success of plastic manufacturing, impacting not only the aesthetic appeal but also the longevity and durability of the product. The subtle, elegant finish of our electronics case enhances its mechanical resistance and overall durability, ensuring it withstands environmental wear. The thermoplastic injection molding process used creates a sturdy yet flexible enclosure, making it an ideal choice for reliable housing of electronic components.
In conclusion, the evolution of plastic injection molding continues to influence the manufacturing landscape by providing precise, efficient, and customizable solutions. Whether it's for high-volume production or specialized custom projects, injection molding stands as a critical technology driving innovation. As manufacturers and consumers alike embrace the qualities of injection molded products, such as our innovative electronics case, the future of plastic manufacturing only looks brighter.
Plastic Injection Molding: Innovation in Electronics Cases
Get Latest Price >
Label | Value |
---|---|
Brand | LS Custom Parts Manufacturers |
Customization Service | Injection Molding, Plastic Injection Molding, Plastic Injection Molds, Insert Molding, Overmolding |
Drawing format | 2D/(PDF/CAD)、3D(IGES/STEP/GLB) |
Material Capabilities | Aluminum、Brass、Bronze、Copper、Hardened Metals、Precious Metals、Stainless Steel、Alloys、TPR |
Sample | Free |
Supply Ability | 100000 Pieces Per Day |
Surface Finish | Customized Finishing |
Thickness | Customized Thickness |
Type | Broaching/Drilling/Etching / Chemical Machining/Laser Machining/Milling/Turning/Wire EDM/Rapid Prototyping/Other Machining Services |
Services | CNC Machining,Metal Casting,Injection Molding,Sheet Metal Fabrication,Rapid Prototyping,3D Printing |
Contact
Ready to start your next project with LS Manufacturing?
Contact us today to learn more about our services and how we can help you achieve your goals.
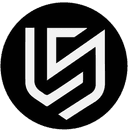
Rapid lead times starting from just 1 business day.
ISO 9001,ISO 14001,IATF 16949 and AS9100D Certification.
Over 100 materials available, with 50+ surface finish options.
Cost-effective mass production.
Order as low as 1 piece.