In the realm of modern manufacturing, the blanking process holds a pivotal role, with its precision and efficiency setting the foundation for numerous applications across different industries. As a key phase in metal fabrication, the blanking process involves cutting flat pieces from larger sheets of material, crucially shaping components that go on to form parts of complex assemblies.
One company that has mastered this intricate process is LS Hardware Tech Co., Ltd. Established by Mr. Nick Zhang and a team of highly skilled engineers, LS Hardware Tech Co., Ltd. boasts over 20 years of rich experience in the manufacturing of hardware and plastic parts. As a stalwart in the industry, LS is renowned for its dedication to delivering only the highest quality products, servicing over 5,000 clients with an array of demands and restoring trust in precision engineering time and again.
At its core, the blanking manufacturing process is about creating blanks that are then utilized in further production phases. This process makes use of high-end, precise machinery—a specialty of LS Hardware Tech Co., Ltd. The company’s advanced machining centers enable the implementation of sophisticated blanking technology that caters to varied client specifications, from automotive to aerospace. LS’s influence is notably global, providing high-precision parts to over 150 countries, a testament to their robust international presence and mastery in metal blanking services.
Moreover, the leap from traditional methods to automated blanking systems represents a significant advancement, heralding benefits such as enhanced efficiency and reduced production time. LS Hardware Tech Co., Ltd.’s commitment to innovation and quality improvement is demonstrated through its ISO 9001:2015 certification. Their expertise in blanking die design and precision blanking ensures supreme accuracy, producing parts that are integral to the assembly and functionality of the final product.
In light of the modern demand for sustainable and efficient manufacturing practices, LS Hardware Tech Co., Ltd. not only delivers state-of-the-art blanking services but also integrates environmentally conscious practices in their operations. Advanced automated blanking systems require less energy and reduce waste, aligning with growing global sustainability initiatives. Moreover, LS’s dedication extends to building partnerships with major factories in China, further cementing its role as an industry leader that prioritizes innovation and client-centric solutions.
In conjunction with their precision engineering services, LS Hardware Tech Co., Ltd. has ventured into consumer products, with their manufacture of the AirPod+ Capsule being a prime example of their expertise in marrying high function with aesthetic appeal. This device reflects the company's innovative spirit, characterized by its refined design and eco-friendly build. Moreover, the AirPod+ Capsule’s streamlined design demonstrates the precision and care that go into blanking technology, with each component crafted using cutting-edge techniques that ensure durability, sustainability, and impeccable quality.
The AirPod+ Capsule is a manifestation of LS’s commitment to transcend mere manufacturing, showcasing what can be achieved when attention to detail meets advanced technology. The blanking and punching process is undoubtedly pivotal in this venture, enabling the precision cutting necessary to create components that perfectly align to complete the Capsule’s structure. Such a sophisticated item not only exemplifies LS’s engineering prowess but also represents a deeper commitment to style, functionality, and environmental responsibility.
In summary, the art and science of the blanking process are integral to modern manufacturing, and LS Hardware Tech Co., Ltd. proudly stands at the forefront as it champions this technique. From its core metal blanking services that shape industries globally, to innovative consumer products like the AirPod+ Capsule, LS is unwavering in its mission to deliver high-quality, precision-engineered solutions. The blend of traditional expertise in blanking manufacturing with cutting-edge automated systems and a sustainability ethos highlights LS’s role as both a leader and visionary in the ever-evolving landscape of industrial production.
Exploring the Precision of Blanking Process in Modern Manufacturing
Get Latest Price >
Label | Value |
---|---|
Brand | LS Custom Parts Manufacturers |
Customization Service | Blanking, Hydroforming, Deep Draw Stamping, Progressive Die Stamping, Metal Stamping |
Drawing format | 2D/(PDF/CAD)、3D(IGES/STEP/GLB) |
Material Capabilities | Aluminum、Brass、Bronze、Copper、Hardened Metals、Precious Metals、Stainless Steel、Alloys、TPR |
Sample | Free |
Supply Ability | 100000 Pieces Per Day |
Surface Finish | Customized Finishing |
Thickness | Customized Thickness |
Type | Broaching/Drilling/Etching / Chemical Machining/Laser Machining/Milling/Turning/Wire EDM/Rapid Prototyping/Other Machining Services |
Services | CNC Machining,Metal Casting,Injection Molding,Sheet Metal Fabrication,Rapid Prototyping,3D Printing |
Find Similar Products
Contact
Ready to start your next project with LS Manufacturing?
Contact us today to learn more about our services and how we can help you achieve your goals.
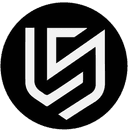
Rapid lead times starting from just 1 business day.
ISO 9001,ISO 14001,IATF 16949 and AS9100D Certification.
Over 100 materials available, with 50+ surface finish options.
Cost-effective mass production.
Order as low as 1 piece.
People who viewed this also viewed
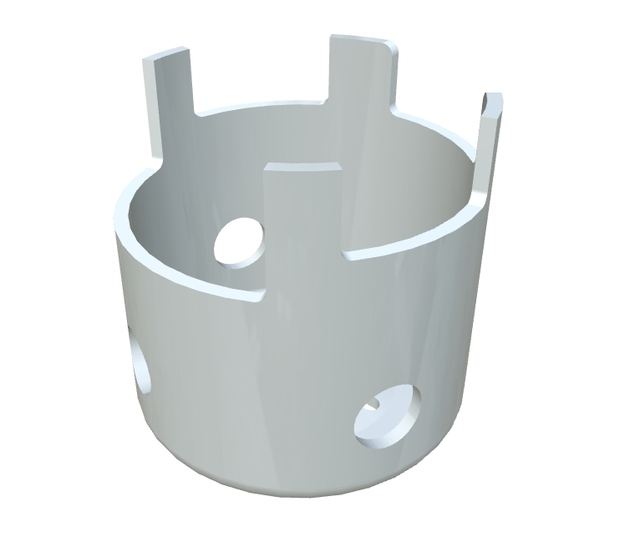
Mastering the Blanking Process: Precision in Metal Blanking
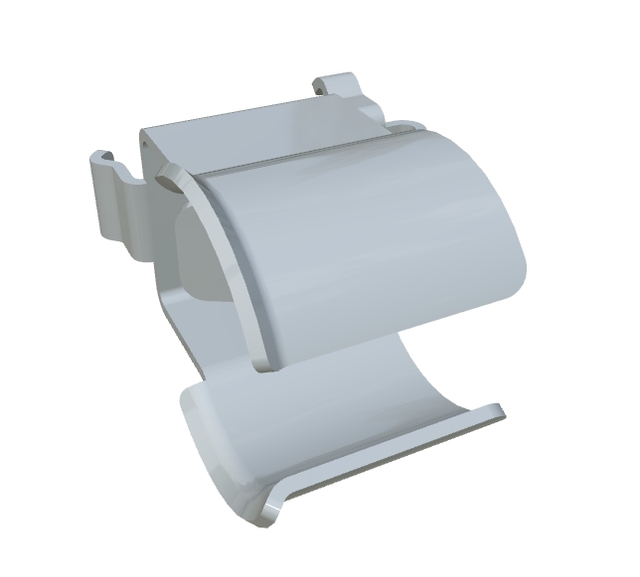
Blanking Process: Mastering Metal Blanking and Tool Design
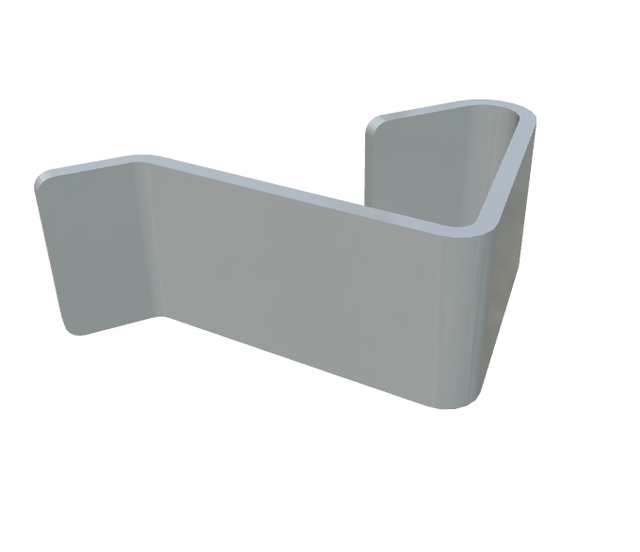
Understanding the Blanking Process in Modern Manufacturing
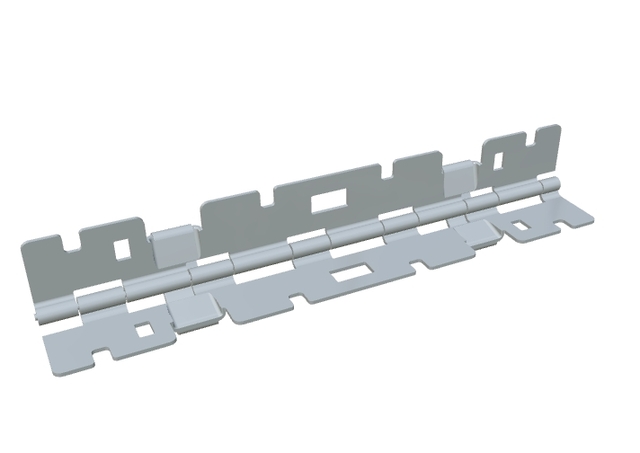
Exploring the Blanking Process: Key to Modern Manufacturing
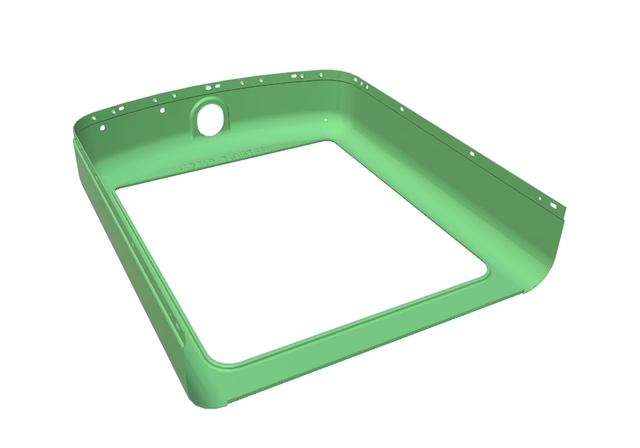
Exploring the Blanking Process: Efficiency and Innovation
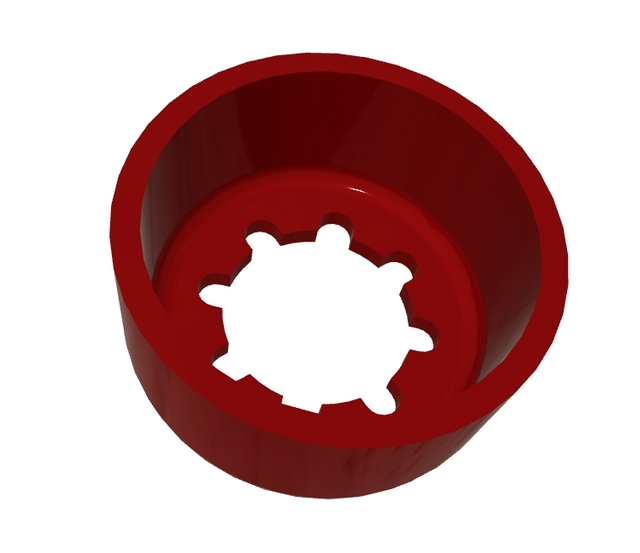
Mastering the Blanking Process: Manufacturing Excellence
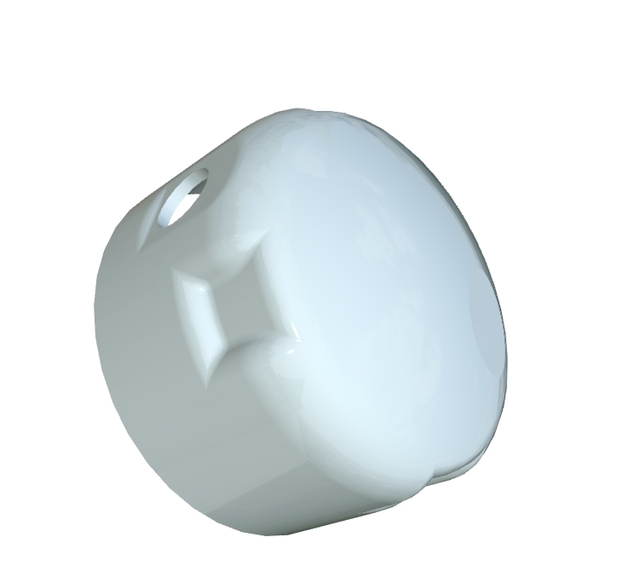
Exploring the Precision of Blanking Process in Modern Manufacturing
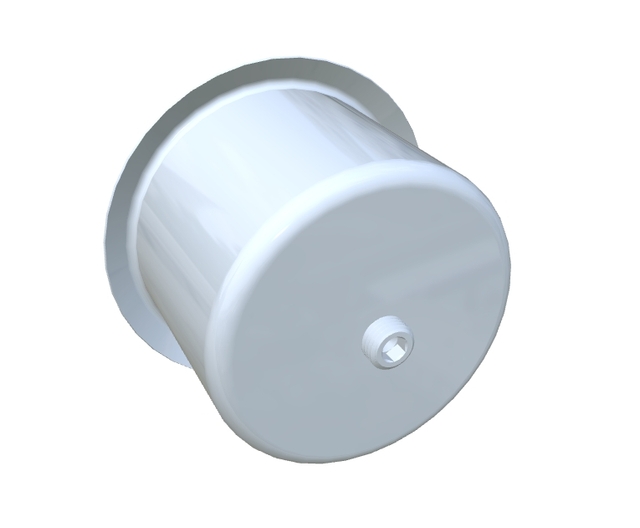
Mastering the Blanking Process in Metal Fabrication