Themolding material for resin sand castingis a blend of quartz sand and resin sand. When resin sand is mixed and heated, it hardens into a solid, smooth mold. A solid mold produces fewer faulty castings, but it comes at a greater cost and a slower production rate. Resin sand molds take longer to make because each one must be mixed and burned individually.
What are the advantages and disadvantages of sand casting?
Theadvantages and disadvantages of sand castingare as follows:
Advantage:
- Adaptable:Sand casting can cast castings of almost any shape and size, from simple geometries to complex mechanical components.
- Low cost:Compared with other casting methods, the cost of sand casting equipment and molds is relatively low, and raw materials are easy to obtain, making the overall production cost low.
- Flexible process:The process of sand casting is relatively simple and easy to adjust and improve. At the same time, it allows certain modifications and adjustments during the casting process to adapt to different casting needs.
- High material utilization:Through reasonable process design and operation,sand casting can make full use of casting materials, reduce waste, and improve material utilization.
- Recyclable:Although the sand mold needs to be discarded after each casting, the sand itself can be processed and reused, helping to reduce resource waste.
Disadvantages
- Low production efficiency:The mold making and pouring process of sand casting is relatively cumbersome and requires a certain amount of time and manpower, resulting in relatively low production efficiency.
- Limited casting accuracy and surface quality:Since the tightness and uniformity of the sand mold are difficult to fully control, the dimensional accuracy and surface quality of the casting may be affected to a certain extent.
- Environmental pollution:Pollutants such as dust, exhaust gas and waste water may be produced during the sand casting process, causing certain pollution to the environment. Although it can be managed through environmental protection measures, attention still needs to be paid to its environmental impact.
- High energy consumption:Sand casting requires a large amount of energy to heat metal and maintain the temperature of thecasting workshop, which increases production costs and energy consumption.
- Labor intensity and safety hazards:Sand casting is highly labor intensive and requires operators to perform heavy physical labor.At the same time, there are safety hazards such as high temperature, dust, and noise during the casting process, and effective protective measures need to be taken to ensure the safety of operators.
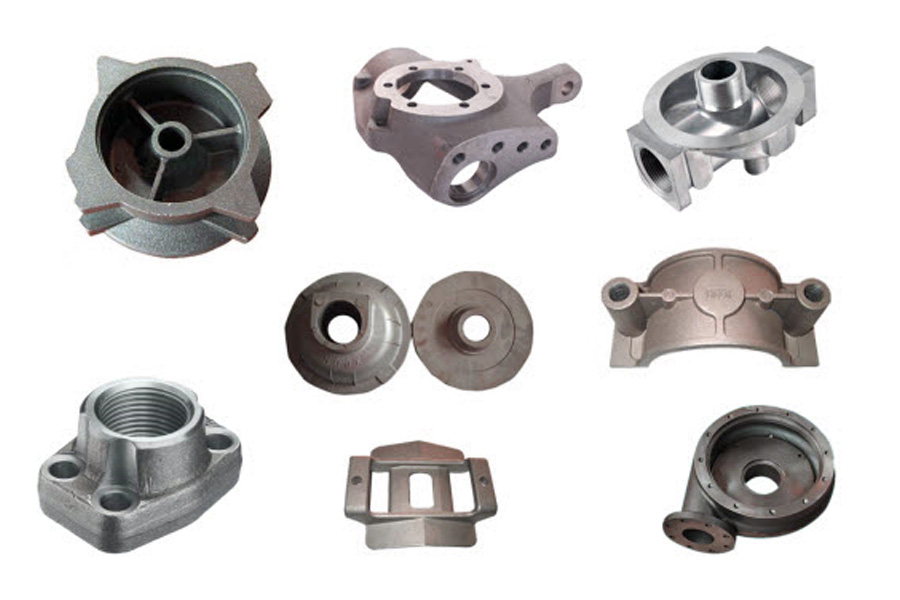
What Are the Applications of Sand Casting?
As a manufacturing process with a long history,sand casting still plays an important role in modern manufacturing. It has wide applications in many fields, including:
Auto industry
In the field of automobile manufacturing,sand casting is an important means of producing automobile parts with complex designs. For example, key components such as engine blocks and gearbox housings are often manufactured using sand casting technology.
Aerospace industry
Sand casting is also popular in the aerospace industry. It is often used to manufacture aircraft engine components and structural components that require extremely high strength and precision. Specifically, turbine blades, casings, brackets and various accessories can be accurately manufactured through sand casting technology.
Build the app
In the construction industry,sand casting technology is often used to produce key products such as pipe fittings and manhole covers. The sand casting process gives these products exceptional durability and sturdiness, ensuring their long life in construction applications.
Piping system components
In the field of piping systems,sand casting technology shows its unique advantages. It is widely used in the manufacture of core components such as valve bodies, pipe connectors and couplings, which play a vital role in pipeline systems.
Extensive manufacturing of metal products
Globally, thesand casting process occupies an important position in the manufacture of metal products. From cold weapons like swords to everyday items like pots and cauldrons, sand casting plays a key role. Although other manufacturing methods have gradually come to prominence as technology develops, sand casting has maintained its irreplaceable status due to its high cost-effectiveness and suitability for mass production.
How Does Sand Casting Compare to Investment Casting?
Sand casting and investment casting are significantly different in many aspects. The following table is a detailed summary of the main differences between the two:
Features/Methods |
Sand casting |
Investment casting |
Process |
Making models (wood, plastic, etc.→), modeling→ modeling→ pouring→ sand removal → cleaning inspection |
Making wax molds→ dipping the slurry many times to form a shell→ dewaxing→ roasting shells→ pouring → cooling→ cleaning inspection |
Finish |
Generally, Ra is about 6.3μm, which is affected by a variety of factors |
Higher, because the mold precision is high and the surface quality of the shell is good |
Applicable Materials |
A variety of metal materials, such as iron, steel, aluminum alloy, etc |
It is suitable for metals with high precision and high surface requirements, such as stainless steel, titanium alloys, etc |
Cost |
For large and heavy parts, the cost is relatively low |
The cost can be higher, especially for complex and delicate designs |
Yield |
Suitable for mass production, but also for lower production volumes |
It can be adapted to different production volumes, but is generally more suitable for mass production with high precision requirements |
Flexibility |
Mold making is relatively simple, and design modification is relatively easy |
The mold is complex to make and the design modification is difficult, but the mold precision is high |
Fields of application |
Automobile industry, machinery manufacturing, construction and other fields |
aerospace, medical devices, art and other fields |
What Are the Challenges of Sand Casting?
As a traditional casting process,sand casting does face a series of challengeswhen facing the transformation and upgrading of modern manufacturing and market competition. The following is a detailed summary of the main challenges faced by sand casting:
- Surface roughness issues:The surface of sand cast castings is often rough and requires additional post-processing steps to improve, which increases production costs and time.
- Dimensional accuracy limitations:Compared with other casting methods, sand casting may have certain disadvantages in dimensional accuracy, which limits its application in the manufacturing of castings requiring high precision.
- Environmental protection and waste disposal:Waste sand generated during the sand casting process needs to be properly disposed of to avoid negative impacts on the environment. At the same time, the waste gas and waste water that may be generated during the casting process also need to be effectively managed.
- Market competition and technological updates:With the development of the manufacturing industry, other advanced casting methods and manufacturing technologies continue to emerge, and sand casting faces challenges from market competition and technological updates. In order to remain competitive, sand casting companies need to continuously invest in R&D and innovation.
- Raw material and labor costs:Fluctuating raw material prices and rising labor costs pose challenges to the cost control of sand casting companies. Businesses need to find ways to reduce costs while maintaining product quality and production efficiency.
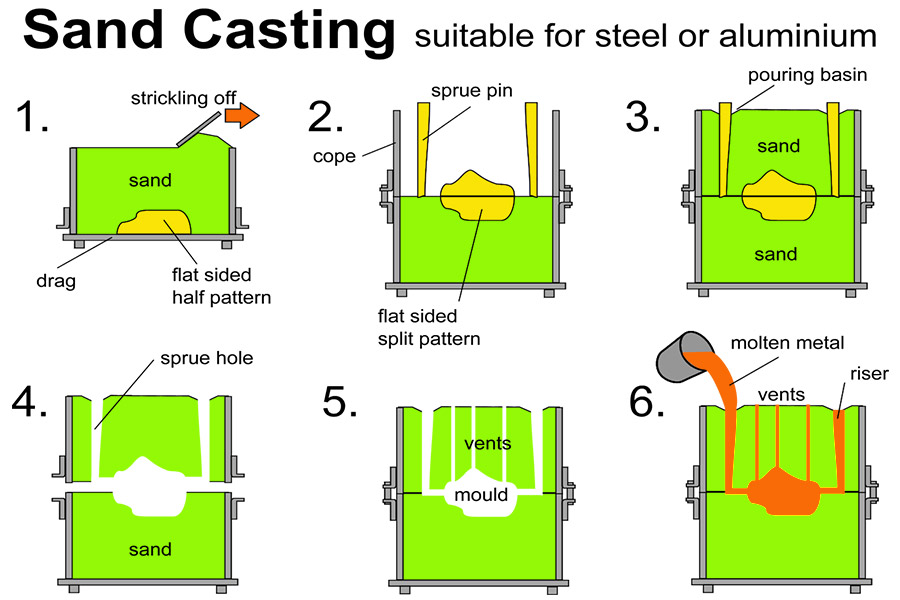
FAQs
1. What is the main process flow of sand casting?
The main process flow of sand casting is: ① Sand preparation: Preparing molding sand and core sand for modeling. ②Mold making: Make molds and core boxes according to part drawings. You can use wood molds, plastic molds or metal molds, etc. ③Molding and core making: Use molding sand to form the cavity of the casting and make the internal shape (core). ④Smelting: Distribute the chemical composition according to the required metal composition, select a suitable melting furnace to melt the alloy material, and form liquid metal. ⑤Pouring: Inject liquid metal into the sand mold, pay attention to controlling the pouring speed to ensure that the liquid metal fills the entire mold cavity. ⑥ Solidification and cooling: After the metal solidifies in the sand mold, it is cooled. ⑦ Demolding and cleaning: Remove gates, sand and other impurities, and sandblast and polish the castings. ⑧Inspection: Conduct quality inspection on castings to ensure that they meet design requirements.
2. What is the surface roughness of sand casting castings?
The surface roughness of sand casting castings varies depending on process conditions and materials, and can generally reach Ra12.5~6.3μm. This mainly depends on factors such as the quality of the sand mold, pouring temperature, alloy composition, and cooling rate. In order to improve the surface roughness, post-processing measures may be required, such as mechanical processing, chemical treatment, etc.
3. What are the advantages of sand casting compared to other casting methods?
Sand casting is widely used in industrial production due to its advantages such as simple process, low cost and strong flexibility. Compared to other casting methods such as investment casting and pressure casting, sand casting is more cost-effective in manufacturing large and heavy parts. At the same time, the sand casting mold is relatively simple to make, the design is easy to modify, and it can adapt to the production needs of castings of different shapes and sizes.
4. What is the dimensional accuracy of sand casting?
The dimensional accuracy of sand casting is usually between IT14-IT18, which means that there is a certain deviation between the size of the casting and the theoretical value. This is mainly due to the characteristics of the sand mold material and the complexity of the casting process. In order to improve dimensional accuracy, it is necessary to strictly control the sand mold manufacturing accuracy, pouring temperature, alloy type and casting process parameters.
Summary
As a traditional and important metal forming process, sand casting still plays an irreplaceable role in modern industrial manufacturing. By continuously improving and optimizing process processes to improve casting quality and production efficiency, sand casting will continue to contribute to industrial development. At the same time, strengthening environmental awareness and technological innovation are also important directions for the future development of sand casting companies.
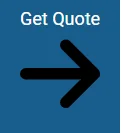
Disclaimer
The content on this page is for reference only.LSdoes not make any express or implied representation or warranty as to the accuracy, completeness or validity of the information. No performance parameters, geometric tolerances, specific design features, material quality and type or workmanship should be inferred as to what a third party supplier or manufacturer will deliver through the Longsheng Network. It is the responsibility of the buyerseeking a quote for partsto determine the specific requirements for those parts.Pleasecontact usfor moreinformation.
LS Team
LS is an industry-leading companyspecializing in custom manufacturing solutions. With over 20 years of experience serving more than 5,000 clients, we focus on high-precisionCNC machining,sheet metal fabrication,3D printing,injection molding,metal stamping,and other one-stop manufacturing services.
Our factory is equipped with more than 100 advanced 5-axis machining centers and is ISO 9001:2015 certified. We provide fast, efficient, and high-quality manufacturing solutions to customers in over 150 countries worldwide. Whether it’s low-volume production or large-scale customization, we can meet your needs with delivery as fast as 24 hours. ChoosingLS Technologymeans choosing efficiency, quality, and professionalism.
To learn more, please visit our website:www.lsrpf.com
