Welding techniques have evolved significantly over the years, offering various methods to bond materials effectively, which are indispensable in numerous industrial applications today. From automotive assembly lines to bridges, the need for strong and reliable welds is paramount. The types of welding vary, each with unique benefits and requirements. Understanding these techniques, along with welding safety tips and the appropriate equipment, ensures both quality and safety in any welding endeavor.
At the forefront of innovation, our company is excited to introduce a groundbreaking solution in structural mounting—our latest metallic component, engineered with high precision. This product exemplifies durability and merger of utility with aesthetics, making it ideal for rigorous industrial applications.
**Types of Welding and Their Applications**
In the world of welding, there are several types that professionals rely on, each suited for different materials and purposes. Some of the most common welding techniques include MIG welding, TIG welding, and Arc welding. **MIG welding** (Metal Inert Gas) is popular due to its ease of use and speed, making it ideal for projects that require rapid completion. It is commonly used in the automotive industry and in small to large shop fabrication.
**TIG welding** (Tungsten Inert Gas) requires more skill but allows for cleaner, precise welds suitable for thinner materials. It is ideal for projects where aesthetics and detail are important, like metal sculptures and automotive bodywork. **Arc welding**, on the other hand, covers processes in which an electric arc is struck between an electrode and the base material. It is versatile and essential for heavy-duty metal applications such as pipeline welding and structural steel.
**Safety Should Come First**
Understanding and implementing welding safety tips is crucial. Always wearing appropriate protective gear such as gloves and helmets is a must. Ensuring a clean and organized workspace free of flammable materials can prevent accidents. It's also crucial to have appropriate ventilation to avoid inhaling harmful fumes.
**Welding Equipment Essentials**
To achieve the best results in welding, having the right welding equipment and supplies is essential. Quality welding machines and torches, alongside high-grade welding rods and wires, can make a noticeable difference in the final product's integrity and appearance.
When used in conjunction with our newly designed metallic component, these techniques can create more reliable and efficient structures. Our product's design includes intelligently placed mounting holes for easy installation and adaptability. This versatility is what makes it perfect for automotive assembly, machinery, and large infrastructure projects.
**Innovating with Durability and Aesthetics**
Our metallic component is not only built for strength but its corrosion-resistant finish ensures longevity despite harsh industrial environments. This makes it ideal for engineers and builders who demand performance alongside durability.
Moreover, the seamless, contoured lines of the component distribute loads evenly, minimizing stress on welds. This functional yet decorative aspect allows for enhanced engineering possibilities while maintaining elegance in design.
**A Versatile Addition to Your Industrial Arsenal**
As industries advance, the demand for components that marry functionality with design is on the rise. Our state-of-the-art bracket exemplifies this fusion, appealing to engineers who value efficiency as well as innovative aesthetics.
This new component stands out by offering superior performance and flexibility across various applications. Whether affixed to machinery, boosting automotive assembly reliability, or formulating a central piece of infrastructure, it is engineered to excel.
In summary, welding remains an indispensable skill in the industrial sector, enhanced greatly by high-quality equipment and materials. By integrating advanced welding techniques and modern tools, you ensure stronger, more resilient bonds that can withstand the test of time.
Innovation is at our core, and with our new metallic component, we aim to elevate the standard and push the boundaries of what’s possible in engineering projects. Experience the future of mounting solutions today.
Mastering Welding Techniques: Types, Safety, and Equipment
Get Latest Price >
Label | Value |
---|---|
Brand | LS Custom Parts Manufacturers |
Customization Service | Sheet Metal Fabrication, Bending, Laser Cutting, Stamping, Welding |
Drawing format | 2D/(PDF/CAD)、3D(IGES/STEP/GLB) |
Material Capabilities | Aluminum、Brass、Bronze、Copper、Hardened Metals、Precious Metals、Stainless Steel、Alloys、TPR |
Sample | Free |
Supply Ability | 100000 Pieces Per Day |
Surface Finish | Customized Finishing |
Thickness | Customized Thickness |
Type | Broaching/Drilling/Etching / Chemical Machining/Laser Machining/Milling/Turning/Wire EDM/Rapid Prototyping/Other Machining Services |
Services | CNC Machining,Metal Casting,Injection Molding,Sheet Metal Fabrication,Rapid Prototyping,3D Printing |
Find Similar Products
Contact
Ready to start your next project with LS Manufacturing?
Contact us today to learn more about our services and how we can help you achieve your goals.
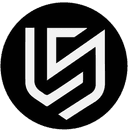
Rapid lead times starting from just 1 business day.
ISO 9001,ISO 14001,IATF 16949 and AS9100D Certification.
Over 100 materials available, with 50+ surface finish options.
Cost-effective mass production.
Order as low as 1 piece.
People who viewed this also viewed
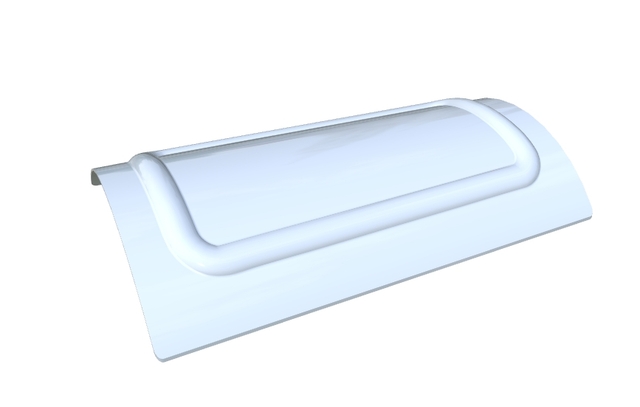
Mastering Welding Techniques for Industrial Excellence
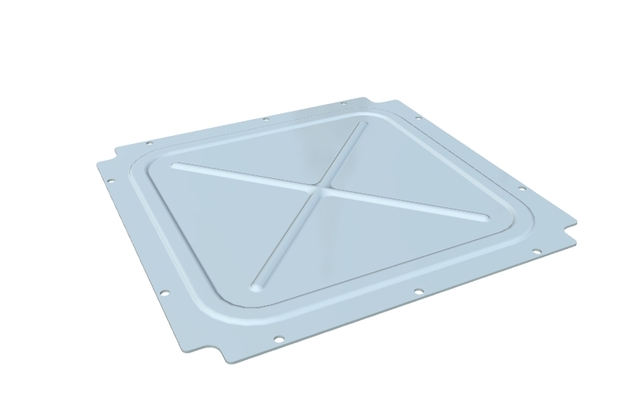
Exploring Types of Welding: Techniques, Safety, and More
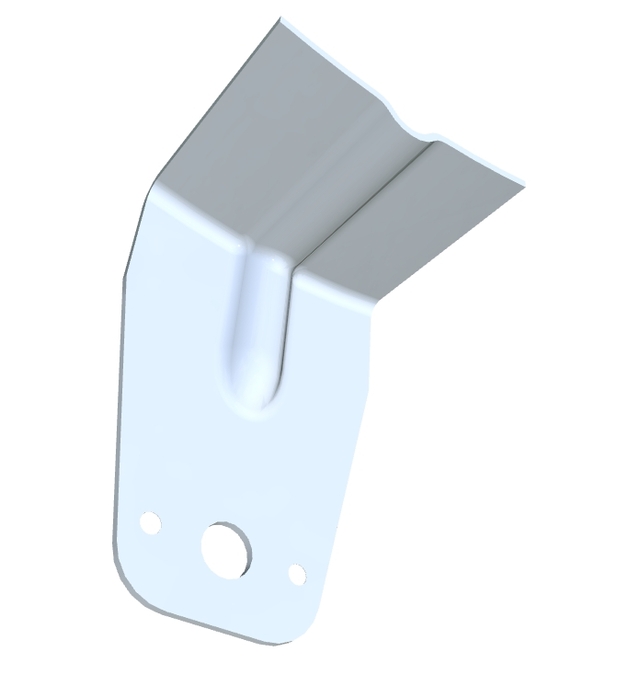
Welding Safety: Ensuring Safe Welding Practices
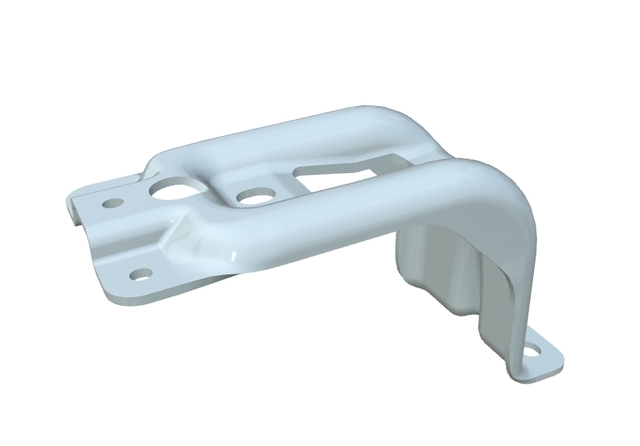
Mastering Welding Techniques: Types, Safety, and Equipment
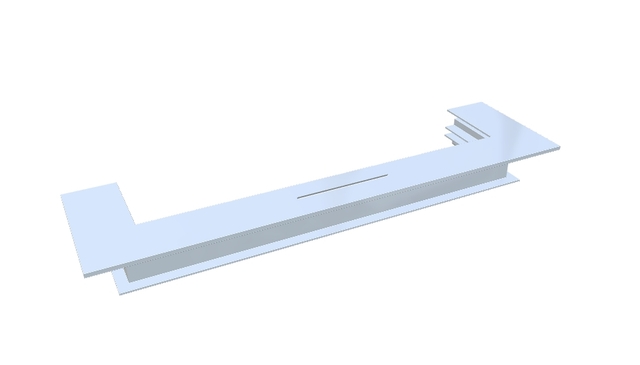
Master Welding Techniques for Architectural Brackets
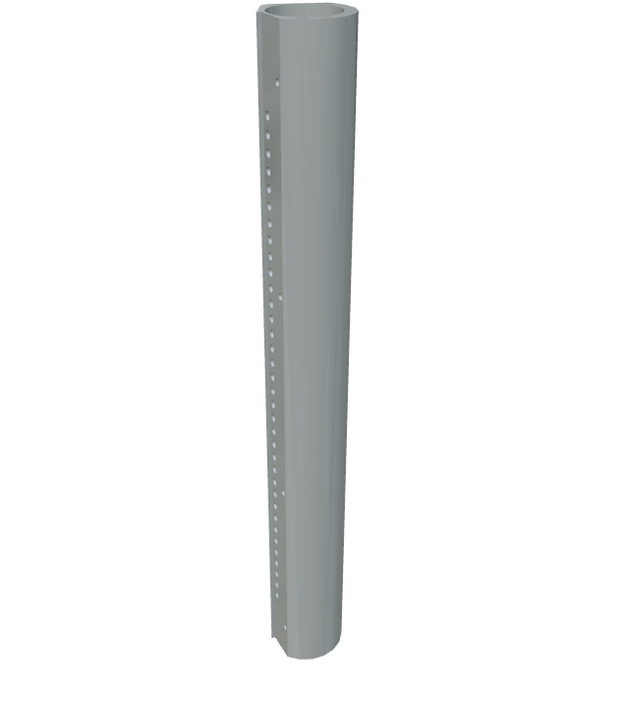
Mastering Welding Techniques: Elevate Your Projects
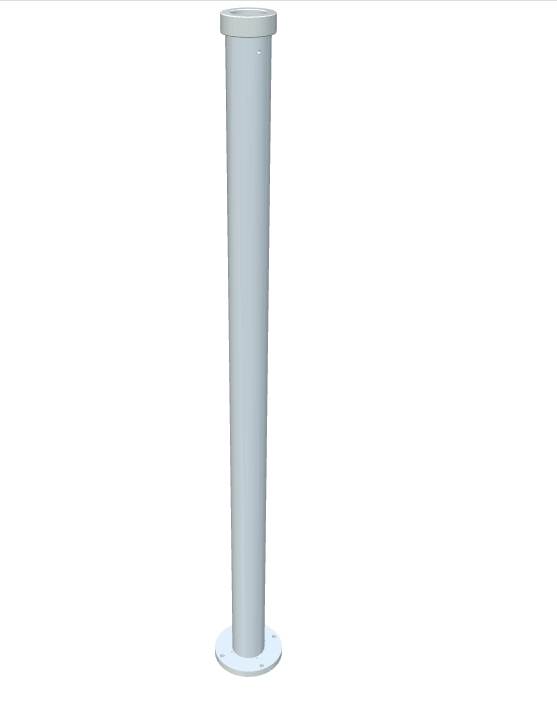
Mastering Welding Techniques for Modern Urban Safety
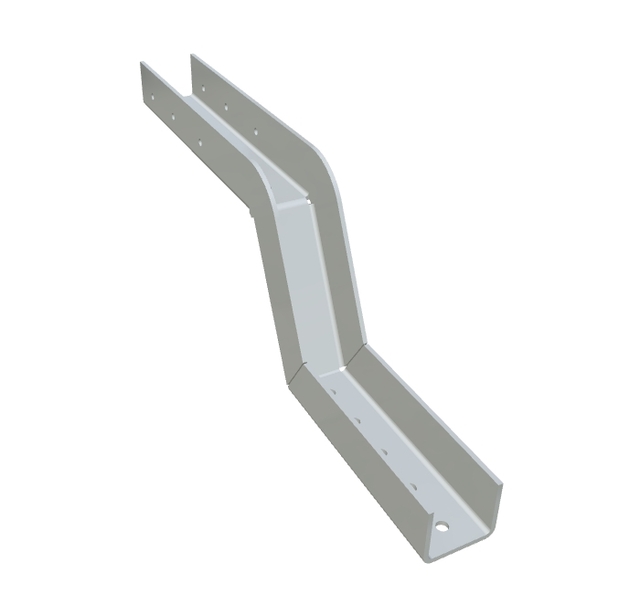
Mastering Welding Techniques: Weld Safely with Innovation