El mundo de la fabricación ha sido testigo de numerosos avances que han simplificado los procesos de producción y mejorado las capacidades de los productos. Una de estas técnicas innovadoras es el moldeo por inserción, un proceso que ha encontrado diversas aplicaciones en todas las industrias. El moldeo por inserción implica incrustar componentes en el plástico durante el proceso de moldeo, lo que da como resultado una sola unidad con mayor durabilidad y funcionalidad. Esta técnica innovadora no solo se limita al ámbito de los plásticos, sino que ha extendido su versatilidad a la fabricación de equipos sofisticados como las tecnologías ópticas.
Al explorar el **proceso de moldeo por inserción**, se hace evidente que es una parte esencial de la producción de piezas complejas con componentes integrados. Este método permite a los fabricantes incorporar diferentes materiales, como metales y cerámicas, en cuerpos de plástico, lo que reduce efectivamente el tiempo de ensamblaje y aumenta la resistencia del producto. La simplicidad y eficiencia de este proceso lo convierten en una opción popular en diversas industrias, incluida la producción de productos como los binoculares CompactZoom Ultra.
Las implicaciones del **moldeo por inserción de plástico** son profundas, particularmente en el campo de la tecnología óptica. Estas aplicaciones implican el diseño de equipos como binoculares, donde la alineación precisa y la construcción duradera son primordiales. Los prismáticos CompactZoom Ultra muestran las ventajas del moldeo por inserción. Utilizan un diseño aerodinámico y ligero sin sacrificar el rendimiento. Con el moldeo por inserción, los binoculares pueden presentar componentes que son robustos y resistentes, críticos para soportar condiciones climáticas variables y terrenos accidentados. El diseño ergonómico, con el dial de enfoque de precisión, enfatiza las intrincadas posibilidades que permite el diseño de moldeo por inserción.
Además, las **aplicaciones de moldeo por inserción** se extienden a la creación de productos con características avanzadas, que incluyen texturas de agarre mejoradas, sellos integrados para resistencia a la intemperie y colocación confiable de componentes, que son vitales para los binoculares destinados a la observación de la naturaleza y eventos deportivos. La fabricación de insertos a medida para aplicaciones específicas garantiza que cada aspecto del producto contribuya a su rendimiento de alta calidad y a la satisfacción del usuario.
**Las ventajas del moldeo por inserto** lo dicen todo. Al minimizar los posibles errores de montaje y reforzar la fiabilidad de los componentes, los fabricantes pueden ofrecer productos que prometen longevidad y alto rendimiento. Los prismáticos CompactZoom Ultra, con su **carcasa duradera y resistente a la intemperie**, son un testimonio de estas ventajas. Esta durabilidad garantiza que los usuarios puedan confiar en su tecnología para brindar una claridad y un detalle asombrosos, ya sea explorando las complejidades de la naturaleza o disfrutando de un evento deportivo de ritmo rápido.
Para concluir, el **equipo de moldeo por inserto** y los procesos utilizados para crear una tecnología tan intrincada son parte integral del crecimiento continuo del sector manufacturero. Los prismáticos CompactZoom Ultra ilustran cómo el moldeo por inserción ha trascendido las aplicaciones tradicionales, marcando el comienzo de una nueva era de innovación de productos caracterizada por un diseño elegante, un rendimiento superior y una adaptabilidad sin igual. A medida que esta tecnología evoluciona, su papel en la producción de equipos y productos de primer nivel se vuelve más pronunciado, lo que lo convierte en un aspecto invaluable de la fabricación moderna
Moldeo por inserción: revolucionando la fabricación de plástico
Obtener el último precio >
Label | Value |
---|---|
Marca | Fabricantes de piezas personalizadas LS |
Servicio de personalización | Moldeo por inyección, Moldeo por inyección de plástico, Moldes de inyección de plástico, Moldeo por inserción, Sobremoldeo |
Formato de dibujo | 2D/(PDF/CAD)、3D(IGES/STEP/GLB) |
Capacidades de los materiales | Aluminio, Latón, Bronce, Cobre, Metales endurecidos, Metales preciosos, Acero inoxidable, Aleaciones, TPR |
Muestra | Gratis |
Capacidad de suministro | 100000 piezas por día |
Acabado superficial | Acabado personalizado |
Espesor | Espesor personalizado |
Tipo | Brochado / Taladrado / Grabado / Mecanizado químico / Mecanizado láser / Fresado / Torneado / Electroerosión por hilo / Prototipado rápido / Otros servicios de mecanizado |
Servicios | Mecanizado CNC, fundición de metales, moldeo por inyección, fabricación de chapa, creación rápida de prototipos, impresión 3D |
Encuentra productos similares
Contacto
¿Listo para comenzar su próximo proyecto con LS Manufacturing?
Contáctenos hoy para obtener más información sobre nuestros servicios y cómo podemos ayudarlo a alcanzar sus objetivos.
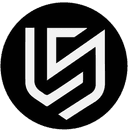
Los tiempos de entrega rápidos a partir de solo 1 día hábil.
ISO 9001, ISO 14001, IATF 16949 y AS9100D Certificación.
Más de 100 materiales disponibles, con más de 50 opciones de acabado superficial.
Producción en masa rentable.
Ordene tan bajo como 1 pieza.
Las personas que vieron esto también vieron
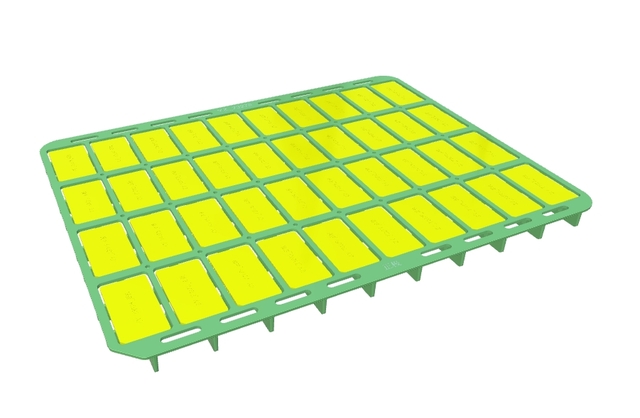
Comprender el proceso de moldeo por inserción: ventajas y aplicaciones
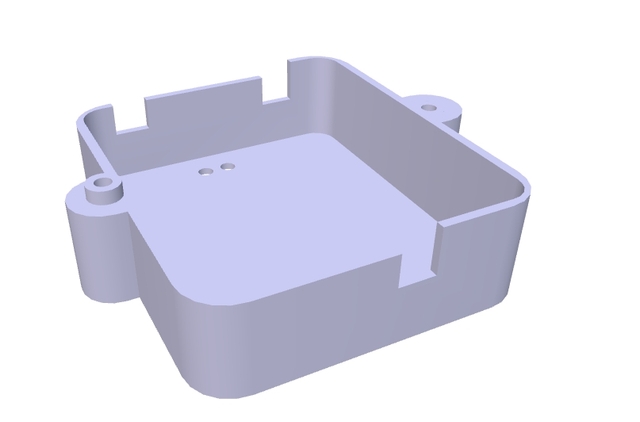
Moldeo por inserción: revolucionando las carcasas electrónicas
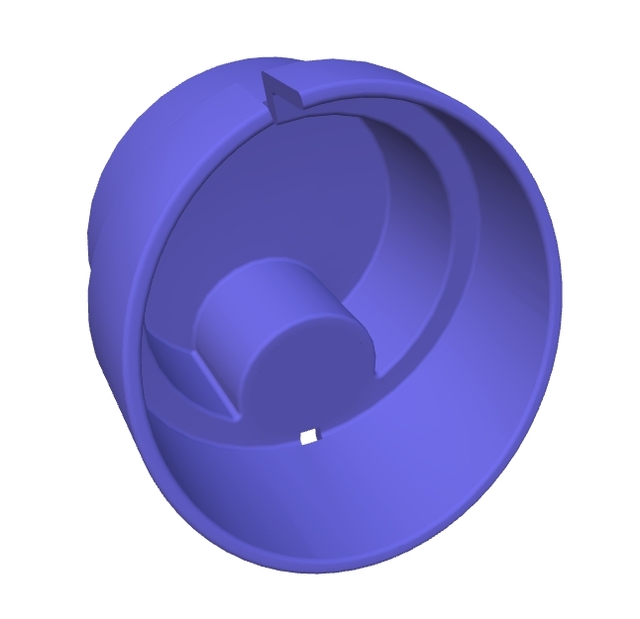
Revolucionando los productos con técnicas de moldeo por inserción
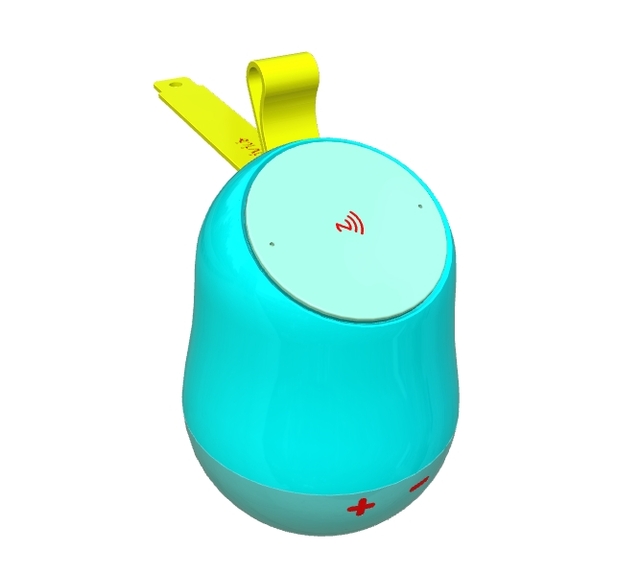
Moldeo por inserción: revolucionando la fabricación moderna
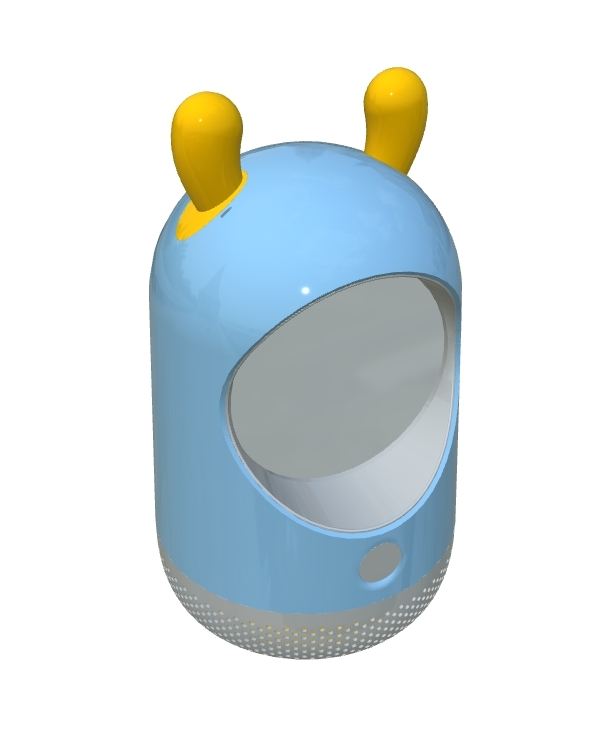
Moldeo de inserción: revolucionando el amigo interactivo inteligente
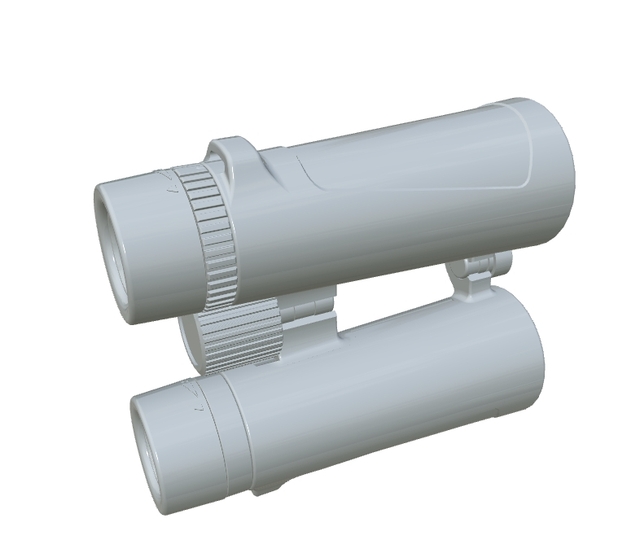
Moldeo por inserción: revolucionando la fabricación de plástico
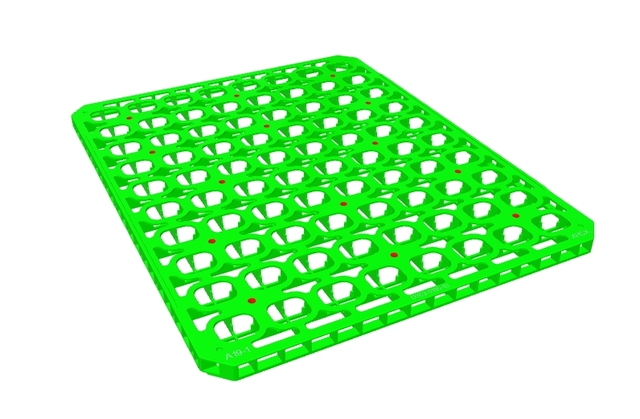
Moldeo por inserción: técnicas, ventajas y aplicaciones
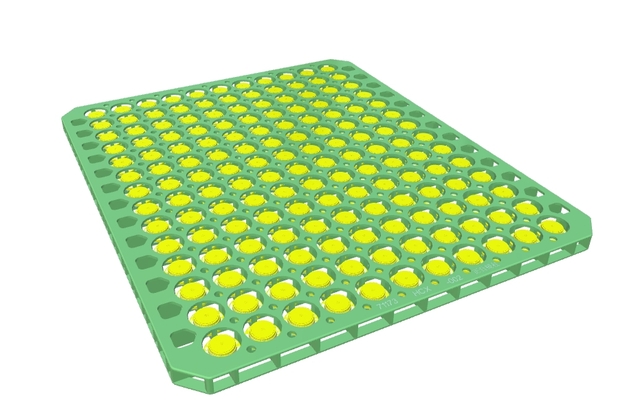
Revolucionando la fabricación con la tecnología de moldeo por inserción