Gearis a widely used transmission component inmechanical equipment, and the performance of gear is closely related to the materials selected. When customizing gears, the choice of materials is crucial because it not only determines the mechanical performance and service life of the gears, but also directly affects the overall performance and operational efficiency of the equipment.
Therefore, we must not only meet the basic requirements of high strength, high wear resistance and high fatigue resistance, but also consider the machinability and economy of the material. Therefore, it is important to explore the most suitable materials for custom gears to optimize equipment performance, reduce costs, and improve production efficiency.
What are the gear materials?
1.steel
- Forged steel: Carbon or alloy steels are typically used, with a carbon content of between 0.15% and 0.6%. For gears that require less strength, speed, and accuracy, use a soft tooth surface (hardness ≤ 350HBS) for convenienceGear cuttingGears that require precision machining are usually made of alloy steel to improve the hardness and wear resistance of the tooth surface.
- Cast steel: good wear resistance and strength. When the gear structure is larger, cast steel is usually used.
2.cast iron
Cast iron gears are mainly used in situations where strength and wear resistance are not required. Grey cast iron has good adhesion and corrosion resistance. Gray cast iron or ductile iron is a common choice for open, low-speed drive gears.
3.Copper alloys
- Brass (H62): Good electrical conductivity, moderate wear resistance, low cost.
- Beryllium Bronze (C17000): Ultra-high modulus of elasticity (125GPa) with excellent fatigue resistance.
For high-speed, light-load, and low-precision gearing, pinions are usually made of non-metallic materials such as cloth, plastic, and nylon to reduce noise.
What are the properties of gear materials?
1. Mechanical properties
- Strength: The gear needs to bear a large load during use, so the material needs to have high strength, including tensile strength, yield strength, etc., to ensure that the gear is not easy to deform and break during long-term use.
- Hardness: The surface hardness of the teeth is a key factor affecting the wear resistance and service life of the gear. Proper hardness can improve wear resistance and prolong the service life of gears.
- Resilience: The ability of a material to resist fracture when subjected to impact. The gears can be subjected to various shocksLoad during use, so the material needs to be flexible to ensure that the gear is not prone to cracking under impact.
2. Process performance
Good processing performance can reduce manufacturing costs and improve production efficiency. For example, gray cast iron is easy to cast and cut, so it is commonly usedGear that does not require high strength is required to manufacture.
3. Environmental performance
- Abrasion resistance: Abrasion resistance isGear materialGears are often worn in pairs during use, so the material needs to be wear-resistant to reduce wear and extend service life. For example, polyamide (nylon) gears have wear resistance, and only 1/5-1/10 metal gears have good wear resistance after long runs.
- Corrosion resistance: It can maintain good working performance under high temperature, high humidity and other conditions, and has excellent chemical corrosion resistance, which is suitable for transmission systems in corrosive medium environments.
4. Heat treatment characteristics
Heat treatment improves the mechanical properties and hardness of the tooth surface hardness. heat treatmentIncluding quenching, tempering, carburizing, and nitriding.
What Industries Need Custom Gears?
- Industrial Machinery & Equipment:Machine tools, cranes, printing machinery and other industrial equipment. Equipment has different requirements for the accuracy, wear resistance and load carrying capacity of the gears, so the gears need to be customized according to the specific requirements.
-
In the automotive sector:In order to achieve power transmission and speed regulation, high-precision gears must be used for transmission and differential speeds. Custom gear solutions can provide gears that meet specific requirements to improve vehicle transmission efficiency and driving stability.
-
Aerospace field:There are extremely high requirements for the accuracy, material, surface treatment and so on of the gear. Customized gear solutions can meet these special needs and ensure the stability and reliability of the aircraft drivetrain system.
-
Robotics & Automation:Robot joints, drivetrains, and other components require high-precision gears for precise motion control. Customized gears can meet the special requirements of the robot in terms of gear size, weight and precision.
What processing techniques are involved in the manufacturing process of gears?
Preparation of raw materials
1. Forging/casting
- Forging: It is used for high-load gears (such as automobile transmission gears) to extrude metal blanks through a die to increase material density.
- Sand Casting:Economically suitable for small and medium-sized cast iron gears (e.g. gearbox gears).
- Precision casting (e.g. EPC casting): Used for gears with complex structures or thin walls to reduce post-processing.
2. Rolling/extrusion
- Hot Rolling Gear Rough: Rough machining of long shaft gears (e.g. train wheels) is produced by continuous rolling.
- Cold Extrusion: Suitable for:Aluminum alloy gears, which can increase the strength of the material and reduce the amount of cut.
3. Powder metallurgy
Compression sintering: used for processing refractory materials (such as titanium alloy gears) or gears with complex shapes, with a material utilization rate of more than 95%.
Tooth machining (roughing and semi-precision machining)
1. Molding and processing
- Hob: The rotary hob continuously engages with the workpiece to cut the involute tooth shape. High efficiency (for mass production), accuracy IT7~IT9, surface roughness Ra 3.2~6.3 μ m.
- Figuration:Reciprocating gear hobbing tool for meshing the workpiece, suitable for machining internal gears or non-standard tooth profiles. High flexibility, but less efficient than gear hobbing.
- Milling:The multi-edge cutter cuts according to the tooth profile and is suitable for one-off or low-volume production. However, it vibrates easily and is not very accurate (IT9~IT10).
2 Special Handling
- Discharge wires: Complex internal holes or irregular gears used to machine high-hardness materials such as hardened steel.
- 3D printing(Additive Manufacturing): Powder Bed Melting (SLS/DLP) or Metal Binder Jetting. Ability to quickly produce lightweight prototypes (more than 50% reduction in lattice structure).
Precision machining and surface treatment
1. Precision machining technology
- Grinding: Grinding the workpiece with a grinding wheel to correct the heat treatment deformation and improve the surface smoothness.
- Honing: The soft honing wheel is in slight contact with a hard surface to eliminate micro-roughness and reduce noise. Improve tooth contact by 10-15 decibels.
- Shavers: Thin blade shavers micro-cut unquenched gears to correct tooth flank clearance. However, it is only suitable for soft tooth surfaces (e.g. quenched and tempered steels).
- heat treatment
Carburizing and quenching: Increases surface hardness (HRC58-62) and prolongs wear resistance.
Nitrogen: low temperature treatment (500-550°C), surface hardness is HV800-1000.
Quenching and tempering: Quenching + high temperature tempering to improve the toughness of the core.
- Coating technology
Physical vapor deposition (PVD): For example, TiN coatings, the coefficient of friction is reduced to 0.1-0.15.
Thermal spraying: WC Co coating increases abrasion resistance by 5-10 times.
- Chemical treatment
Phosphating/Bluing: Enhances the corrosion resistance of light load gears.
Post-processing and inspection
1. Finishing and polishing
Use a brush or chemical solvent to remove processing residues and improve surface smoothness.
2. Vibration detection and dynamic balancing
- Dynamic balance test: Correction of high-speed rotating gears, such as the imbalance of hub gears.
- Toothcheck: UseCMM or Gear Tester.
3. Painting and packaging
Anti-rust treatment: painting, plating or phosphating to prolong the service life.
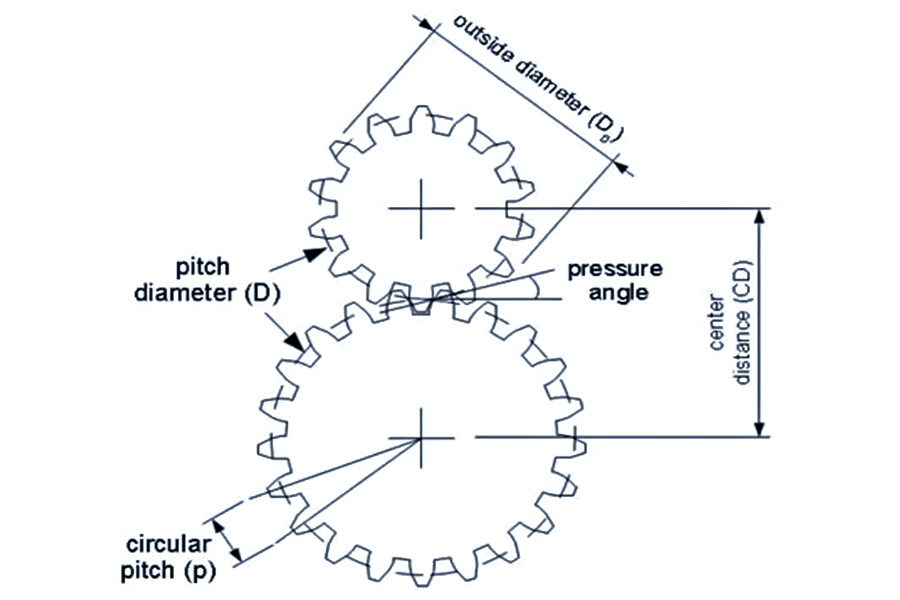
What factors should be considered when choosing a material for a custom gear?
1. Core technical factors
Performance requirements
- Mechanical properties: tensile strength, yield strength, fatigue limit (e.g., carburized steel for heavy loads,nylonfor light loads), impact resistance (e.g. mining machinery that requires high-toughness materials).
- Abrasion resistance: Surface hardness (HRC58 or above) and coatings (e.g. WC Co) can extend service life.
- Corrosion Resistance: Corrosion-resistant materials such as stainless steel (316L) or PEEK are required in wet/chemical environments.
Processing compatibility
- Processing difficulties: steel can beRolling/grinding, but the deformation needs to be controlled by heat treatment. Nylon needs to be injection molded and shrinkage controlled.
- Surface treatment: carburizing and quenching, PVD coating and other technologies have high requirements for materials.
2. Economic and cost factors
- Cost: The cost of different materials varies greatly, and you need to choose the right material according to your actual needs and budget. Minimize material costs while ensuring performance.
- Productivity: Different materials have different processing difficulties and efficiency. For example, the machining accuracy of hard gears is very high, and precision machining methods such as:Grinding teeth, which will increase production costs and cycles. Therefore, when choosing materials, it is necessary to consider their impact on productivity.
3. Application scenario factors
Scenario type | Critical material selectionprinciple | Typical materials |
High-speed precision transmission | High hardness and low coefficient of friction | Breathable carbon steel, POM+ coating |
Heavy load shock conditions | High toughness and fatigue resistance | Alloy steel (38CrMoAl), cast iron |
Lightweight requirements | Low density, high modulus | Aluminum alloy, carbon fiber composite materials |
Low-cost mass production | Simple processes and a stable supply chain | HT250 gray cast iron PA6 |
Case Studies.
Background: Gear customization of RV reducers for industrial robots.
An industrial robot company needs to customize planetsRV reducer gear set(module 2mm, outer diameter Φ 12mm, mass production of 10,000 pieces) has the following core requirements:
- High precision: The meshing clearance of the gear pair is ≤ 5 μ m (IT5 level tolerance).
- Lightweight: Single gear ≤ 8 grams.
- Low cost: $500,000 total cost ≤ (including materials, processing, and testing).
Material Selection:
1. Core material comparison
material
|
Density (g/cm ³) | Tensile Strength (MPa) | Cost ($/kg) | Difficulty of processing |
20CrMnTi carburized steel |
7.85 |
1080 |
120 |
★★★ |
7075-T6 aluminum alloy |
2.8 |
570 |
60 |
★★★★ |
POM-CF30 reinforced plastic |
1.4 |
160 |
80 |
★★ |
2. Final material selection plan
- Main materials:7075-T6 aluminum alloy(It has obvious lightweight advantages, and the density is only 1/3 of steel);
- Surface Treatment: Carbon steel coating (0.05mm thick, improve wear resistance and contact hardness to HRC60).
- Selection criteria: aluminum alloy meets the requirements of lightweight (single weight ≤ 7.5g), carburizing layer to ensure wear resistance, material cost is 40% lower than pure steel, CNC machining efficiency is higher (cutting speed increased by 30%).
1. Structural design
- Topological weight reduction: production of honeycomb hollow structures with 20% reduction in material usage and weight reduction from 12 grams to 7.5 grams;
- Tolerance chain control: The tooth shape error is controlled to ± 1.2 μm through multi-axis simultaneous programming.
2. CNC machining process
process | equipment | Key parameters | function |
rough machining | Five-axis CNC milling machine | Cutting speed 800m/min, feed rate 0.1mm/rev. | Quickly remove excess parts to ensure dimensional stability. |
Semi-precision machining | Internal and external cylindrical grinding machines | Accuracy IT7, surface roughness Ra0.8 μ m. | Improve the accuracy of the gear base. |
Precision machining | Gear hobbing machine + gear grinding machine | Hobbing pitch error ≤ 0.5 μ m, grinding correction clearance reaches 4.8 μ m. | Achieve IT5 level meshing accuracy. |
Surface treatment | Vacuum carburizing furnace + sandblasting | The depth of the carburized layer is 0.08mm, and the surface hardness is HRC62. | Improves abrasion and fatigue resistance. |
- By embedding a temperature sensor in the hobbing process to monitor the tool temperature in real time (with an accuracy of ± 0.5 °C), the cumulative error of the pitch is reduced from 1.8 μ m to 0.9 μ m.
- Using a transfer fixture to machine 4 gears in a single clamping process reduces tool change time by 30%.
Cost control:
1. Material cost management
- Centralized procurement: long-term agreement with aluminum suppliers, the unit price is reduced from US$60/kg to US$53/kg;
- Scrap recycling: The powder metallurgy process increases the recovery rate to 95%.
2. Control of processing costs
Cost items | processing |
Single-piece processing time |
8 mins |
Tooling costs |
$8,000 |
Scrap |
1.5% |
3. Testing costs
- In-line measurement system: laser interferometer is used for detectionGap in grinding teethAvoid bulk scrap in real time.
- Statistical process control: Analyze the distribution of key dimensions with relevant data software to reduce the frequency of comprehensive inspections by 20%.
4. Total cost accounting
project | measure | proportion |
Material costs |
$265,000 |
53% |
Processing costs |
$155,000 |
31% |
Testing and tooling |
$45,000 |
9% |
Contingency reserves |
$35,000 |
7% |
total |
$500,000 |
100% |
This case shows that through the combination of material innovation and process optimization,Industrial robot gear customizationIt can achieve cost control goals while meeting the requirements of high precision and lightweight, and provide reusable solutions for high-end equipment manufacturing.
Why CollaborateLS?
- Worth:The company provides the design documents, we select the best materials and processes, and send you a competitive quotation.
- Precision Quality:We have state-of-the-art equipment and strict quality control measures to ensure that every component meets the highest standards. We are ISO 9001 certified to ensure consistent quality and reliability.
- Fast Delivery:With efficient production processes and advanced logistics systems, we can ship to you in the shortest possible time.
Summary
whenCustom gearsThe best material selection should be based on the specific application, performance requirements, and cost budget. Steel, especially forged steel, is preferred for a wide range of applications due to its high strength, impact resistance, and heat treatability. However, under special conditions such as high-speed optical load transmission, non-metallic materials such as nylon and laminated wood are also favored due to their lightweight and low-noise properties. In addition, for high-temperature and corrosive environments, special materials that are resistant to high temperatures and corrosion should be selected. In short, the optimization of gear materials needs to be considered according to actual needs.
Disclaimer
The content of this page is for informational purposes only.LS SeriesNo representations or warranties of any kind, express or implied, are made as to the accuracy, completeness or validity of the information. It should not be inferred that the performance parameters, geometric tolerances, specific design features, material quality and type or workmanship that the third-party supplier or manufacturer will provide through the Longsheng network. This is the responsibility of the buyerAsk for a quote for partsto determine the specific requirements for these parts.pleaseContact usLearn moreEFOrmation.
LS Team
LS is an industry-leading companyFocus on custom manufacturing solutions. With over 20 years of experience serving more than 5,000 customers, we focus on high precisionCNC machining,Sheet metal fabrication,3D printing,Injection molding,metal stamping,and other one-stop manufacturing services.
Our factory is equipped with more than 100 state-of-the-art 5-axis machining centers and is ISO 9001:2015 certified. We provide fast, efficient and high-quality manufacturing solutions to customers in more than 150 countries around the world. Whether it's low-volume production or mass customization, we can meet your needs with the fastest delivery within 24 hours. chooseLS TechnologyIt means choosing efficiency, quality and professionalism.
To learn more, please visit our website:www.lsrpf.com
FAQs
1. Can plastic gears replace metal?
Plastic gears can partially replace metal gears under certain conditions, but not in all cases. Plastic gears have the advantages of light weight, low noise, no lubrication, and strong corrosion resistance. However, plastic gears are generally not as strong, heat-resistant, and durable as metal gears.
2. Which gear materials meet the environmental requirements?
Nylon gears are considered an eco-friendly material due to their non-toxic, odorless, and recyclable properties. Nylon gears are widely used in a wide range of industrial fields because they not only have excellent heat resistance, toughness, and chemical resistance, but also can maintain stability in various harsh environments.
3. How to prevent gear pitting?
Choose high-strength, high-hardness gear materials, use appropriate lubricating oils, and control their temperature to reduce friction and wear. By improving machining accuracy and surface smoothness, the concentration of tooth surface stress and the generation of micro-cracks can be reduced.
4. Which gear material has the longest service life?
Carburized steel is generally considered to have the longest service life among gear materials, especially in high-precision, high-load industrial environments. For extreme environments such as high temperature and strong corrosion, special materials such as ceramics and titanium alloys can be considered. The choice of actual materials needs to be balanced against specific operating conditions, cost budgets, and lightweighting requirements.
Resource