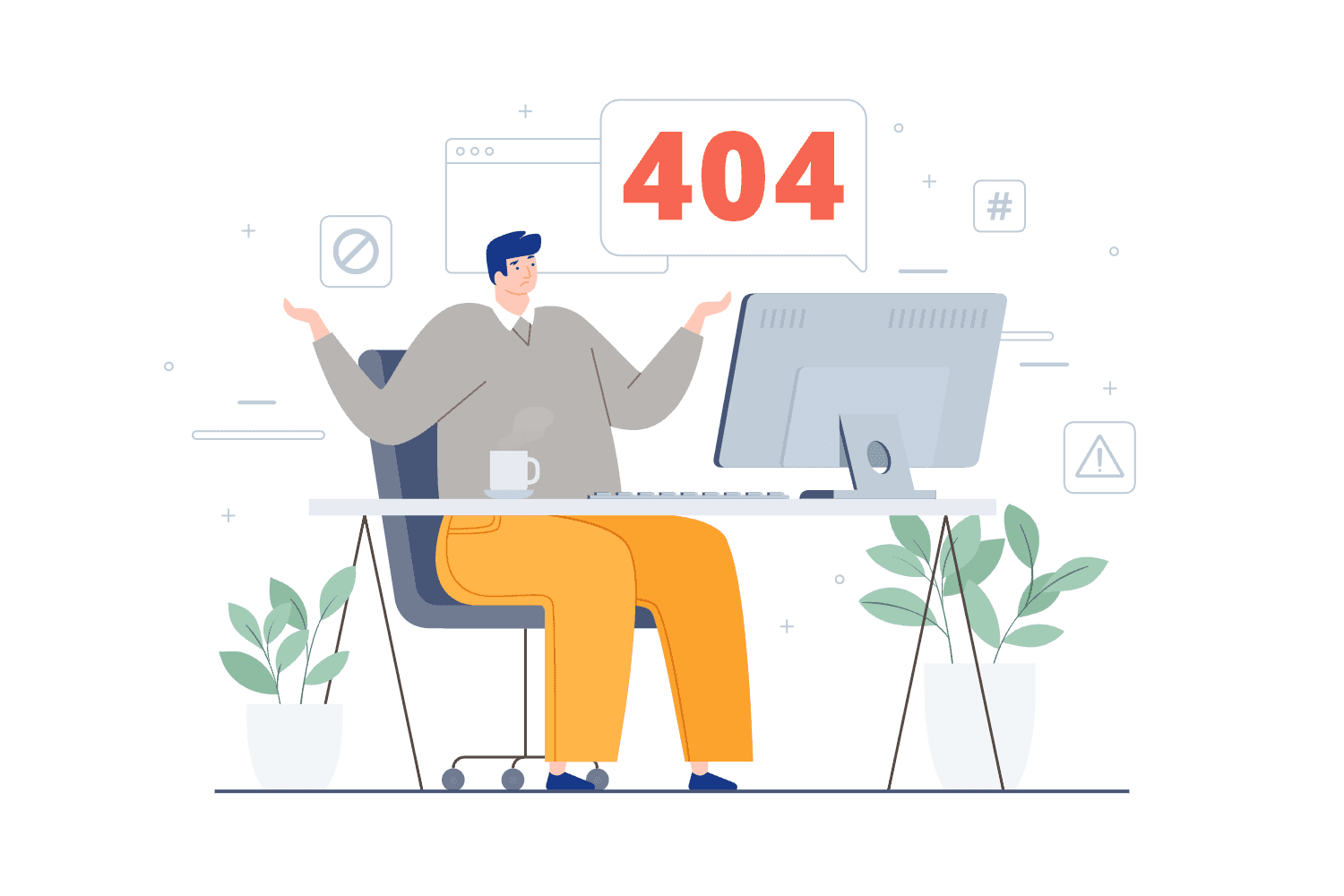
Sorry,The page you are visiting does not exist.
ReturnReady to start your next project with LS Manufacturing?
Contact us today to learn more about our services and how we can help you achieve your goals.
Sorry,The page you are visiting does not exist.
Return