In the ever-evolving landscape of modern industry and innovation, "SLA technology" stands as a beacon of precision and possibility. At the forefront of this technological revolution is LS Hardware Tech Co., Ltd, a leading name in manufacturing hardware and plastic parts, embracing the nuances and advantages of Stereolithography (SLA) to cater to a broad spectrum of industries. With over two decades of experience under the belt of its founder, Mr. Nick Zhang, LS envisions and actively executes a future where innovation meets efficient, high-quality manufacturing.
The term SLA technology, or Stereolithography, refers to a pioneering method of 3D printing that uses light to cure liquid resin into hardened plastic in a layer-by-layer fashion. This process, known for producing exceptionally detailed and accurate parts, has become an indispensable tool in various sectors including automotive, medical devices, consumer electronics, aerospace, and industrial equipment. The ability of SLA 3D printing to create complex structures that are lightweight yet durable is unmatched, making it an attractive choice for prototyping and production.
Stereolithography methods rely heavily on the quality and adaptability of SLA printers and SLA resin types. At LS Hardware Tech Co., Ltd, our commitment to top-tier technology is evident in the seamless crafting of our products, such as the Multi-Functional Mounting Bracket. This innovative creation, designed with precision and flexibility in mind, exemplifies the perfect synthesis of stereolithography applications in modern manufacturing. Using high-quality, lightweight materials, our mounting brackets ensure exceptional durability while maintaining a minimalist design. The bracket features six pre-drilled holes for effortless installation across various surfaces, embodying LS’s dedication to form and function.
Our mounting bracket further highlights the "Advantages of SLA," offering not only functional benefits but also an aesthetic appeal with its sleek, rounded edges. The strategic design, complete with a central, rectangular cut-out, optimizes cable management and the integration of additional components, aligning with cutting-edge infrastructure needs and advanced setups. This level of customization and refinement in design underscores the intrinsic values of SLA technology: precision, efficiency, and innovation.
LS Hardware Tech Co., Ltd has long recognized the profound potential of Stereolithography materials in creating high-precision parts. Our factory boasts over 100 high-end machining centers and operates under the stringent quality standards of ISO 9001:2015 certification. The breadth of our service extends to more than 150 countries and regions globally, proving our capacity to deliver high production efficiency coupled with top-quality performance. Our extensive experience allows us to cater to a wide variety of client needs—from prototyping to mass production—ensuring our solutions are tailor-made to bring client visions to life.
Venturing into SLA printing not only necessitates expertise in the machinery and materials but also a keen understanding of SLA printing tips. These include maintaining optimal resin viscosity, ensuring precise calibration and alignment of printers, and meticulous post-processing for finished parts. These nuances, mastered by LS’s team of skilled engineers, are critical in harnessing the full potential of SLA to produce components that are intricate in design yet robust enough to withstand demanding applications.
In summary, the incorporation of SLA technology into LS Hardware Tech Co., Ltd's suite of manufacturing solutions exemplifies a harmonious blend of experience, innovation, and quality. Our Multi-Functional Mounting Bracket is a testament to what can be achieved through cutting-edge stereolithography methods. As a cornerstone of our manufacturing prowess, Stereolithography enables us to deliver products that not only meet but exceed the expectations of our international clientele. We proudly stand at the intersection of technology and creativity, committed to pushing the boundaries and setting new standards in the world of high-precision part manufacturing.
SLA Technology: Innovating Precision with Stereolithography
Get Latest Price >
Label | Value |
---|---|
Brand | LS Custom Parts Manufacturers |
Customization Service | Stereolithography, 3D Printing Services, Selective Laser Sintering, Fused Deposition Modeling, Multi Jet Fusion |
Drawing format | 2D/(PDF/CAD)、3D(IGES/STEP/GLB) |
Material Capabilities | Aluminum、Brass、Bronze、Copper、Hardened Metals、Precious Metals、Stainless Steel、Alloys、TPR |
Sample | Free |
Supply Ability | 100000 Pieces Per Day |
Surface Finish | Customized Finishing |
Thickness | Customized Thickness |
Type | Broaching/Drilling/Etching / Chemical Machining/Laser Machining/Milling/Turning/Wire EDM/Rapid Prototyping/Other Machining Services |
Services | CNC Machining,Metal Casting,Injection Molding,Sheet Metal Fabrication,Rapid Prototyping,3D Printing |
Find Similar Products
Contact
Ready to start your next project with LS Manufacturing?
Contact us today to learn more about our services and how we can help you achieve your goals.
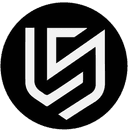
Rapid lead times starting from just 1 business day.
ISO 9001,ISO 14001,IATF 16949 and AS9100D Certification.
Over 100 materials available, with 50+ surface finish options.
Cost-effective mass production.
Order as low as 1 piece.
People who viewed this also viewed
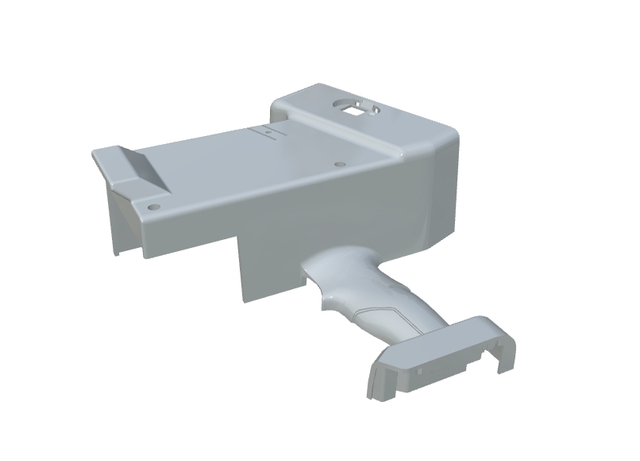
Exploring SLA Printing: Precision and Innovation in 3D Manufacturing
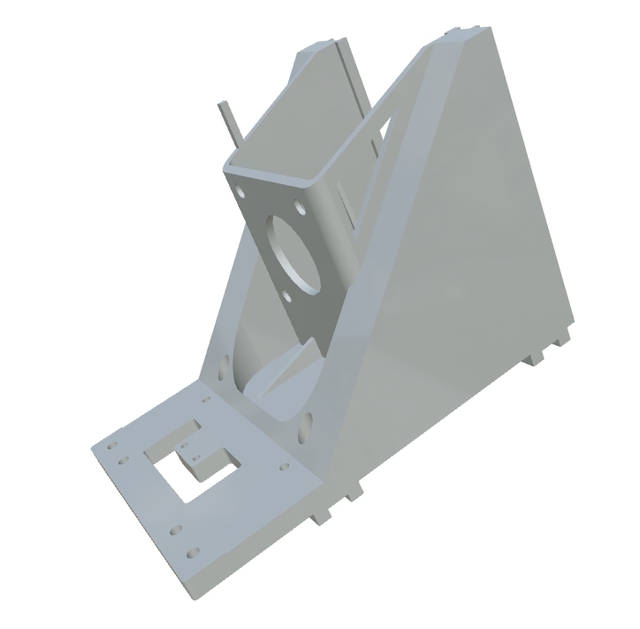
SLA 3D Printing: Revolutionizing Industrial Design and Manufacturing
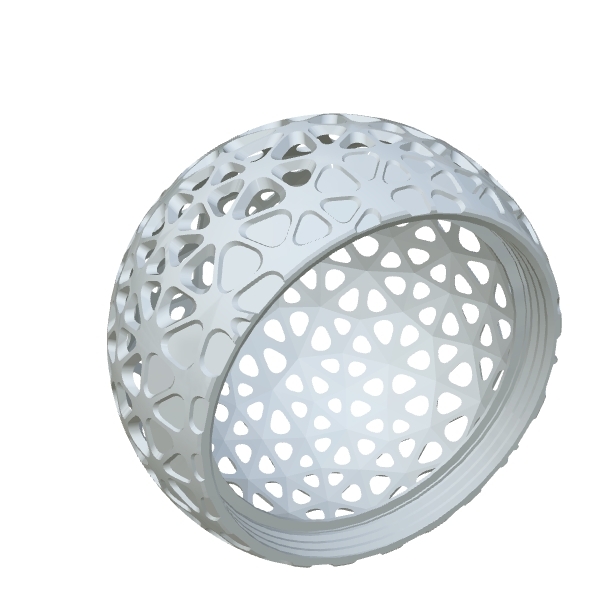
Mastering SLA Technology: Revolutionizing 3D Printing
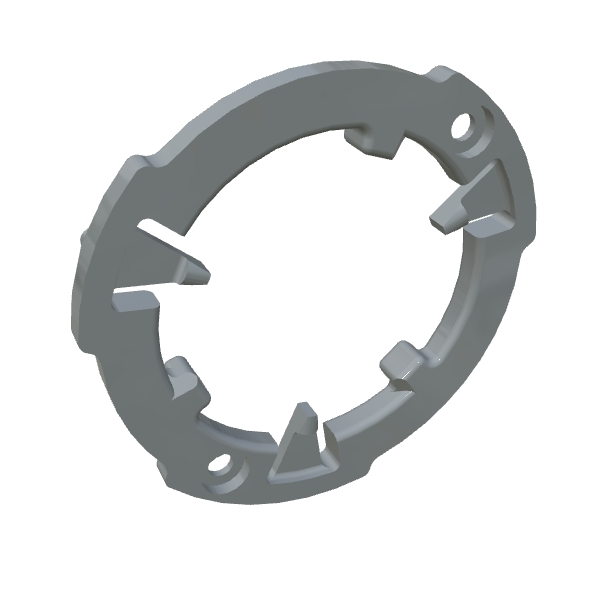
SLA Printing: Revolutionizing Precision Manufacturing
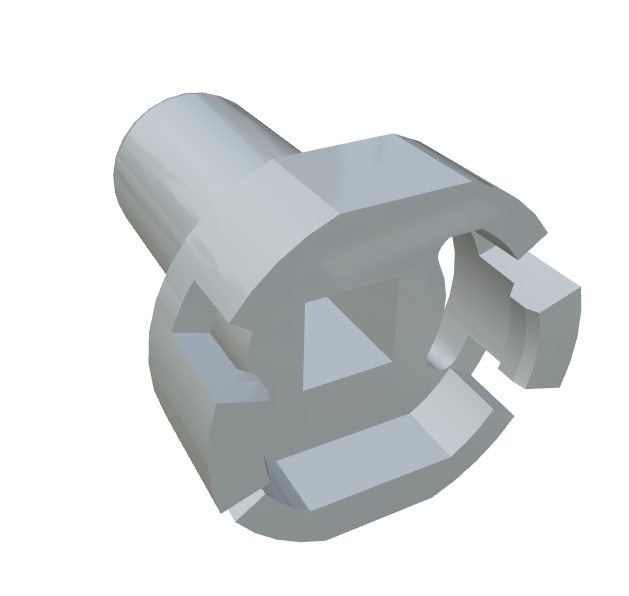
Revolutionizing Manufacturing with SLA Printing Technology
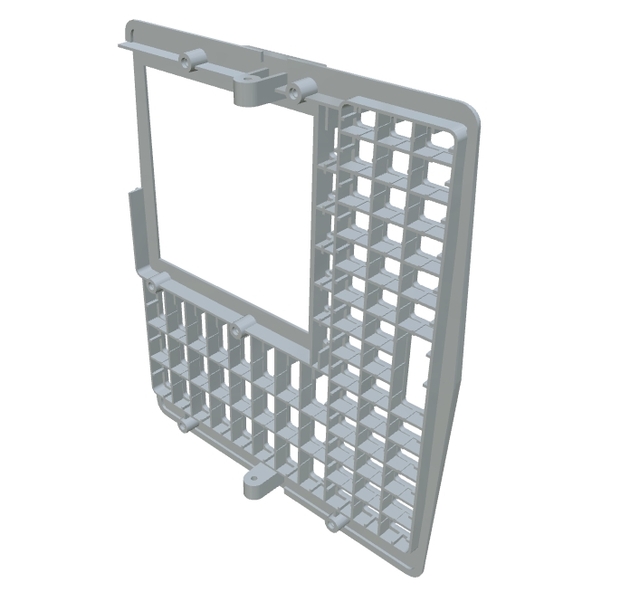
SLA 3D Printing: Transforming Modern Manufacturing
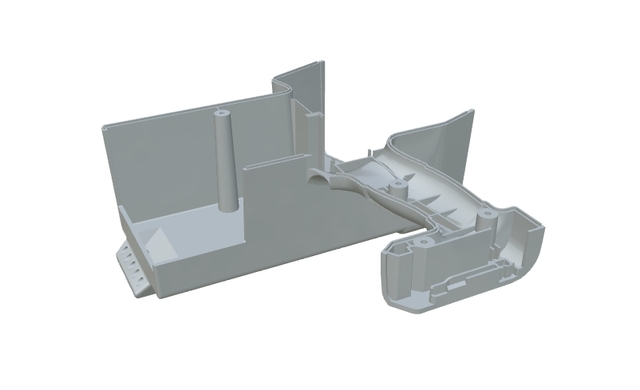
Unlock Precision Manufacturing with SLA Printing: A Guide
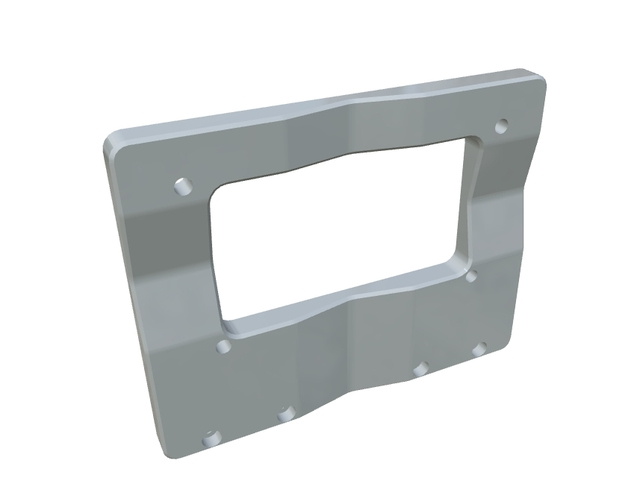
SLA Technology: Innovating Precision with Stereolithography