In the vast field of modern manufacturing,Metal stampingAs a core processing technology, it plays a crucial role. With its high efficiency, accuracy and low cost, it is widely used in many industries such as automobiles, aerospace, electronic equipment, household appliances, medical equipment, etc., and has become one of the key technologies to achieve lightweight, precise production in these industries. one. So, what exactly is metal stamping?
What is metal stamping?
Metal stamping refers to the process of processing metal plates into desired shapesSheet metal stamping mold. Its principle is mainly to use the mechanical force of the hole punch to process the material into the desired shape. The stamping machine is mainly composed of a frame, slider, mold and a gearbox. whenMetal stamping machineWorking, first place the sheet metal between the molds, and under the action of mechanical force, the sheet metal is processed into the desired shape. Different stamping dies can be processed into metalstampingDifferent shapes.
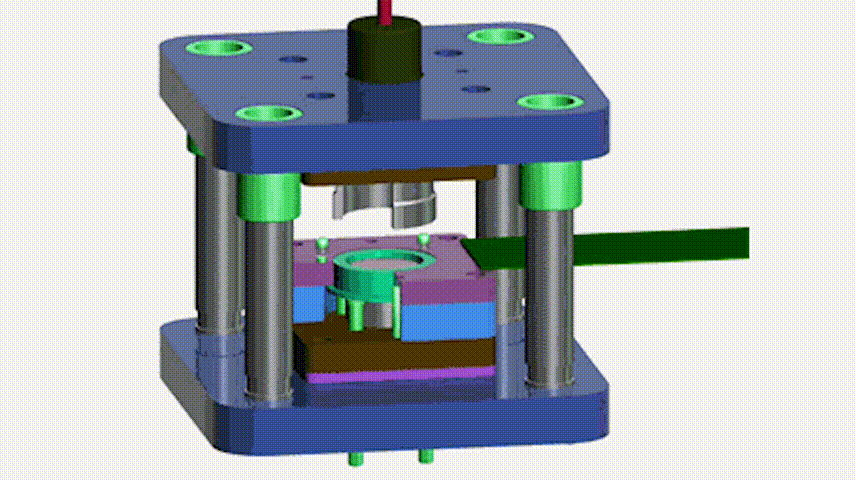
How does the metal stamping process work?
- Material preparation:Select the appropriate oneStamp metaland perform necessary pretreatment such as cutting, cleaning, degreasing, etc.
- Mold design and manufacturing:Design and manufacture stamp molds according to product drawings. The accuracy and rationality of the mold directly affect the quality and production efficiency of the product.
- Imprinting to form:The metal plate is placed between the molds and pressure is applied by pressure to cause the cardboard to plastically deform under the constraints of the mold to form the desired shape. The stamping process may include various deformation methods such as blanking, punching, bending and stretching.
- Subsequent processing:After stamping, the parts may require burring, trimming, cleaning, heat treatment, surface treatment and other subsequent treatments to meet the final requirements of the product.
- Quality inspection:Strictly check the size, shape, surface quality and other aspects of the finished product to ensure that the product meets the design requirements.
Advantages and disadvantages of metal stamping
Advantages of metal stamping | Disadvantages of metal stamping |
High efficiency and productivity | Initial investment |
Rapid production of large quantities results in higher productivity and lower unit costs. | The large initial cost of tools and machinery, which can be a barrier to smaller scale production. |
Accuracy and consistency | Limitations of design complexity |
Produce parts with stable quality and tight tolerance in many industries. | Some extremely complex designs may not be feasible or require additional processes. |
Multifunctional | Tool wear and maintenance |
Applicable to a range of complexities across industries, from simple to complex parts. | Regular maintenance and replacement of molds and holes is necessary, which increases costs and downtime. |
Cost-effective | Substance restrictions |
For mass production, especially the economy of waste and reduced economies of scale. | Some materials may not be suitable due to properties such as brittleness or low ductility. |
Material variety | The potential of quality issues |
Compatible with a variety of metals and alloys, with flexibility in material selection. | The risk of defects, such as warping or surface defects, requires strict quality control. |
What are the different types of stamping processes?
1.Blanking
BasicMetal stampprocessIt uses molds to separate materials that can be made directly into flat parts or prepare blanks for use in other stamping processes such as bending, painting, etc. The blank space is widely used in industrial sectors such as automobiles, household appliances, electronics, electronic equipment, instrumentation, machinery, machinery, railways, railways, communications, communications, chemical, chemical industry, textiles, textiles and aviation spaces.
2. Type
The punching is applied to the pressure on the metal plate through a specially designed mold to form the hole of the desired shape. It is commonly used to manufacture on parts through holes or specific functional holes to produce parts with various hole shapes, such as ventilation holes. , bracket or panel. Chibi and medium hardness metal suitable Stamped metal Avoid cracks during stamping.
3. Bending
Bending refers to the process of bending a metal plate into a desired shape or angle through a mold. This process applies bending force to the metal plate, causing the metal plate to bend and deform under the action of the mold. Bending is one of the common processes in metal stamping. It is widely used to manufacture a variety of parts and products such as boxes, shells, brackets, etc. to provide the shape and structure required for metal products.
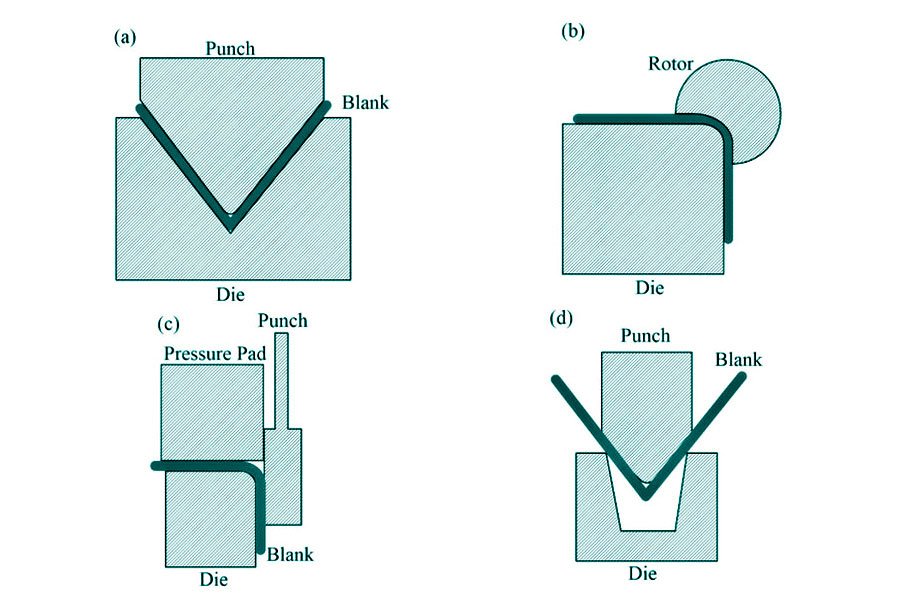
4. Extend
Also known as drawing or calendar, it is a stamping treatment that uses a mold to sprint into an open hollow part to a flat blank. Thin-walled parts can be made in cylindrical, stepped, conical, spherical, box-shaped and other irregular shapes.
5. Graphics
Brand is creationMetal stamps, pattern or texture on the hardware surface. For example, add decorative features, logos,Metal stamps, or the texture of components commonly found in coins and jewelry.
6. To-do Items
One of the most basic forms of metal stamping is to use machining tools to punch holes in metal plates to create multiple small hollow areas. The punching material produced during the entire processing process is discarded.
7. Transmission
This is a plastic processing method that bends the edges of the sheet blank, or material along a narrow area of the precast hole edge on the blank, along a curve or straight line along a vertical edge. It is mainly used to strengthen the edges of parts, remove the trimming edges, and assemble them with other parts. Connecting part.
8. Door
The main feature of the groove is to transfer a small V-shaped notch or groove fromMetal pedal. Usually, two pieces of metal need to be interlocked or connected, such as creating labels and notches for components.
What are some examples of metal stamping applications?
Automotive Industry
It plays a crucial role in the automotive manufacturing industry - producing components such as body panels, brackets, chassis parts, engine mounts, brackets and suspension components. This process ensures the production of lightweight, durable and structural acoustic parts to meet stringent safety and performance requirements.
Aerospace Department
Metal stamping also arrives at paradise through the aerospace department. This process can be used to manufacture key components such as aircraft structural parts, engine parts, brackets and accessories, ensuring lightweight parts with complex geometries while maintaining strength and durability, which helps improve fuel efficiency and performance.
Electronics Industry
In the electronics industry, electronic devices (connectors, terminals, radiators, shielding components and brackets) are widely used. Metal stamping enables precise manufacturing of complex parts required for electronic components while ensuring proper conductivity and durability.
Household appliances
The process is also widely used to manufacture household appliances such as refrigerators, washing machines, ovens and HVAC systems. It produces components such as panels, housings, brackets and handles, providing aesthetic appeal and structural integrity.
Medical and health industry
In the medical field, devices such as surgical instruments, orthopedic implants, stents and connectors also have components that undergo a metal stamping process, ensuring the production of precise, sterile and biocompatible parts is critical for medical applications.
Construction Industry
Metal stamping products are widely used in structural and decorative components such as brackets, connectors, fasteners, hinges and cladding panels. Overall, the process produces long-lasting corrosion-resistant components that meet the industry's strict requirements.

What is the type of metal stamping machine?
Mechanical brushing machine
Mechanical pressing mainly uses a motor connected to a mechanical flywheel to transmit and store energy. The rotation of the motor drives the flywheel to rotate, releasing the energy in the flywheel during the stamping process, driving the slider (or punching) to move upward, thereby realizing the stamping treatment of metal materials.
Mechanical stamping machines have the advantages of simple structure, low manufacturing cost and ease of maintenance. They come in a variety of punch sizes, ranging from a few millimeters to hundreds of millimeters, and at different pressure speeds, usually between 20 and 1,500 rods per minute. These presses range in size from 20 to 6,000 tons and are suitable for progressive and transfer stamping in high-volume production.
Hydraulic Publishing House
Hydraulic presses use hydraulic systems to apply pressure to the material. The hydraulic system converts the pressure of liquid (usually oil) into mechanical energy through a hydraulic pump, which drives the slider to move up and down. The hydraulic piston replaces the fluid with a force level proportional to the diameter of the piston head, allowing advanced control of the pressure amount.
Hydraulic presses have the advantages of stable pressure, adjustable stroke and speed, and can provide full power at any time during a stroke. These presses usually range in size from 20 to 10,000 tonnes, with stroke sizes ranging from about 10 to 800mm. Hydraulic presses are often used in smaller production operations to create more complex, deeper stamped parts than mechanical presses.
Mechanical servo stamping machine
Mechanical servo stamping machines use high-capacity motors instead of flywheels and precisely control the motor's speed and torque through a servo control system to accurately control sliding motion.
Mechanical servo presses have the advantages of stroke, sliding position and movement, and the speed can all be controlled and programmed. They can be made at a more complex stamping speed faster than hydraulic presses and are the most expensive pressure of the three types.
What are common metal stamping materials?
Aluminum and aluminum alloys
Aluminum is a non-productive metal that is relatively cheap and has an excellent strength to weight ratio, making the parts durable, sturdy and lightweight. At the same time, aluminum is corrosion resistant and non-toxic, and does not require coating during finishing, although it can smoke oxidize to enhance its appearance and increase its corrosion resistance. Usually used as a device component during stamping.
Carbon steel/stainless steel
Stainless steel is a ferrous metal that contains a lot of chromium, molybdenum and nickel. It is corrosion-resistant, non-magnetic, has good wear resistance, does not require electroplating, and can be heat-treated. Carbon steel and stainless steel stamping processes are usually used to manufacture equipment casing, structural parts, casing, etc. However, due to their strong rigidity, imprint oils are often used to improve the process.
Titanium alloy
Titanium alloy stamps are mainly used in large equipment, aircraft, ships and other products that require high strength and light weight. Due to the difficulty of the process, special stamping oil must be used to improve the process.
Copper and copper alloys
Copper is easy to form and is ideal for rapid production of one-piece, seamless components and is compatible with the cold formation process. Copper is a low-maintenance and durable metal that resists corrosion and has natural hygiene properties. Brass alloys retain many of the beneficial properties of copper, such as smooth surfaces, corrosion resistance and electrical conductivity. Therefore, it is often used as a device component during stamping.
Why choose Longsheng to provide metal stamping service?
1. Metal stamp service
Our custom metal stamping and molding services are suitable for a variety of industries, including automotive, aerospace, manufacturing and more, to meet the different needs of our customers. Our team has extensive experience and expertise to provide customers with high-quality metal stamping forming services and technical support. Our metal stamping service can provide prototype solutions for custom metal parts, contact us today to start your project.
2. Metal stamping parts production base
Longsheng has a professional team with strong skills and rich experience, and can provide customers with professional technical support and after-sales service. We abide by the principle of "first, customer first" and provide our services to our customers wholeheartedly. If you have any processing needs or questions, please feel free to contact us. We look forward to working with you!
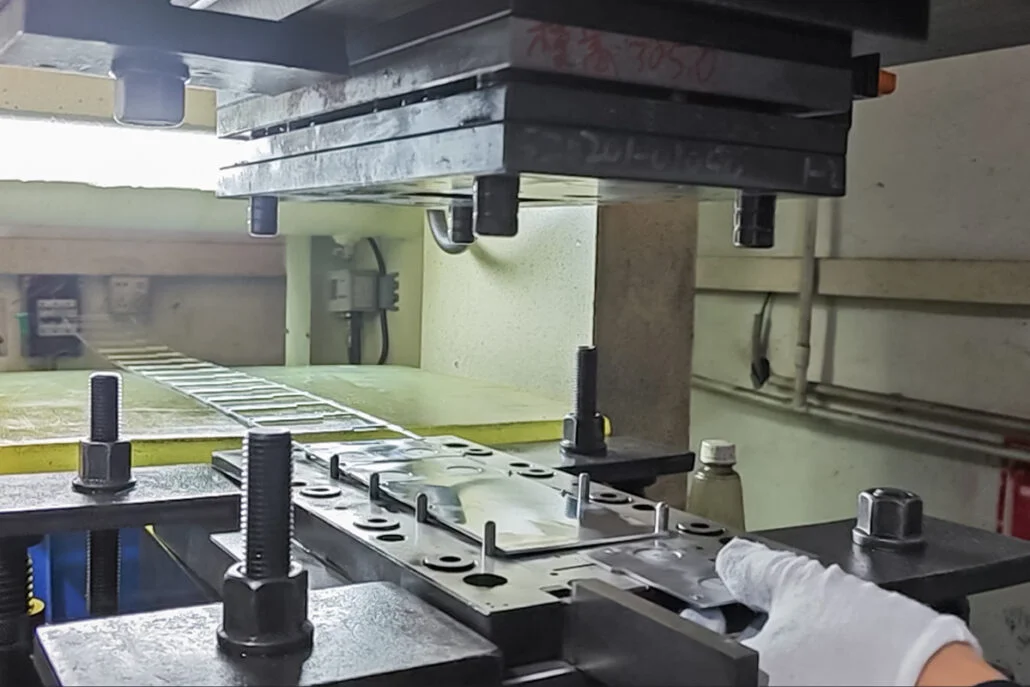
FAQ
1. Where is the metal stamping?
Metal stamping is widely used in many industries such as automobiles, aerospace, electronics, household appliances and medical equipment. In the automotive industry, stamping parts are an important part of human body manufacturing. In the aerospace field, stamping technology is used to manufacture compositesMetal sealParts and components; in the electronics and household appliances industry,Metal stampingUsed to manufacture a variety of sleeves, brackets and other parts.
2. What is metal paper stamping?
Sheet metal stamping parts are a common component in modern industrial manufacturing. They mainlyStamping on metal, bend on metal plates, form and other processes.
3. What is the difference between stamping and manufacturing?
There are certain differences between stamping and manufacturing in terms of concepts, application areas and characteristics. As a specific treatment method, stamping plays an important role in the manufacturing process. Manufacturing is a broader concept covering a variety of processing methods and process routes, including stamping.
4. What is the meaning of metal stamping?
Metal stamping is of great significance in industrial production. It not only improves production efficiency, reduces costs and improves product quality, but also promotes technological innovation and industrial upgrading. Therefore, in future industrial production, metal stamping will continue to play an important role and make greater contributions to economic development and social progress.
Summary
Metal stamping is an effective, precise and low-cost metal processing method that plays an important role in modern manufacturing. With the continuous development of technology and the continuous growth of market demand, metal stamping technology is also constantly innovating and improving. Automation, intelligence and precision have become important trends in the future development of metal stamping technology. At the same time, with the rise of new energy vehicles, 5G communications, intelligent manufacturing and other emerging industries, the demand for metal stamping products is also growing, providing a wider space and opportunity for the development of metal stamping technology.
Disclaimer
The content on this page is for reference only.LSThere is no representation or warranty of any express or implied representation or warranty as to the accuracy, completeness or validity of the information. What a third-party supplier or manufacturer should not be inferred through the Longsheng Network, so any performance parameters, geometric tolerances, specific design characteristics, material quality and type or workmanship should not be inferred. It's the buyer's responsibilitySeeking a part quoteIdentify specific requirements for these parts.pleaseContact UsMoreinformation.
LS Team
This article is written by multiple LS contributors. LS is a leading resource in manufacturing.CNC processing,Sheet metal manufacturing,3D printing,Injection molding,Metal stamping, and more.