The world of manufacturing and design has been revolutionized by innovations in **medical device components**, offering solutions that blend precision, functionality, and durability to meet the demands of various industries. Whether it's the creation of seat parts for prosthetics or the advent of modular designs like the EvoArc Wall Light, the modern approach to production and engineering reflects the dynamic interplay between technology and usability.
At the heart of medical device manufacturing lies the integration of **precision CNC machining**—a method that ensures accuracy in the production of intricate components. For example, seat parts manufacturing for prosthetics requires not only the finest materials but also the highest level of design precision to accommodate the unique needs of individuals. These components must balance factors such as weight, durability, and comfort, all while adhering to strict medical standards. Thanks to advancements in CNC machining services, manufacturers can now deliver these bespoke solutions with unparalleled precision.
Take for instance the **AxisFlow-90 Modular Connector**, a standout example of design meeting functionality. While not explicitly designed for medical uses, its minimalist yet robust design embodies the kind of engineering suitable for applications such as medical device prototypes. Its streamlined curved profile helps reduce material stress, and its precision threaded base ensures secure connections—a vital feature for devices that require stability and reliability under variable conditions. Whether used in medical device machining or as a component in broader industrial solutions, the AxisFlow-90 exemplifies the potential of meticulous design.
Similarly, the **PrecisionFit™ Duct Elbow Adapter** mirrors the principles of efficiency and innovation characteristic of high-quality medical device components. Designed for optimizing airflow systems, it boasts a seamless integration mechanism, corrosion resistance, and noise reduction. While primarily designed for HVAC systems, its attributes could easily translate into medical device prototypes that require controlled airflow or sterile environments. It’s a product that showcases how innovations in one sector can provide inspiration and benchmarks for others.
In addition, seat parts for prosthetics highlight the importance of integrating cutting-edge technology with human-centered design. Prosthetic components must align with the user's body dynamics, requiring expertise in both seat parts design and manufacturing. This is where medical device machining shines, combining precision engineering with adaptable designs to create prosthetics that are not only functional but life-enhancing. From the initial prototype to the final product, every step of the process is enhanced by advancements in precision CNC machining.
Lastly, let's not overlook innovations in aesthetic and functional design, as seen in the **EvoArc Modular Wall Light**. While its primary role is as a lighting fixture, its geometric perfection and smart connectivity could inspire similar approaches in the design of modern medical devices. Imagine devices that seamlessly integrate technology, aesthetic appeal, and user-centric features—this is the future of medical device components.
In conclusion, the evolution of medical device manufacturing is driven by advanced methods like CNC machining, coupled with innovative designs that cater to both form and function. Whether it's seat parts for prosthetics, modular connectors, or duct adapters, these components reflect a dedication to improving both individual lives and industrial efficiencies. As technology continues to evolve, the boundaries of what can be achieved in the realm of medical device components are being redefined, offering exciting possibilities for the future.
Innovations in Medical Device Components: Precision & Design
Get Latest Price >
Label | Value |
---|---|
Brand | LS Custom Parts Manufacturers |
Customization Service | CNC Machining, CNC Milling, CNC Turning, 5-Axis CNC Machining, Gear Machining |
Drawing format | 2D/(PDF/CAD)、3D(IGES/STEP/GLB) |
Material Capabilities | Aluminum、Brass、Bronze、Copper、Hardened Metals、Precious Metals、Stainless Steel、Alloys、TPR |
Sample | Free |
Supply Ability | 100000 Pieces Per Day |
Surface Finish | Customized Finishing |
Thickness | Customized Thickness |
Type | Broaching/Drilling/Etching / Chemical Machining/Laser Machining/Milling/Turning/Wire EDM/Rapid Prototyping/Other Machining Services |
Services | CNC Machining,Metal Casting,Injection Molding,Sheet Metal Fabrication,Rapid Prototyping,3D Printing |
Contact
Ready to start your next project with LS Manufacturing?
Contact us today to learn more about our services and how we can help you achieve your goals.
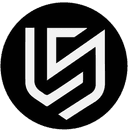
Rapid lead times starting from just 1 business day.
ISO 9001,ISO 14001,IATF 16949 and AS9100D Certification.
Over 100 materials available, with 50+ surface finish options.
Cost-effective mass production.
Order as low as 1 piece.
People who viewed this also viewed
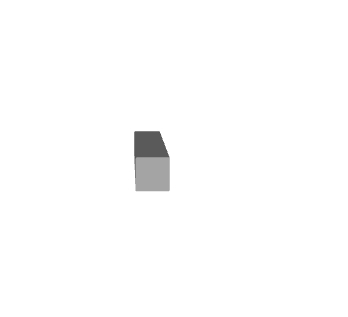
CNC Machining: Transforming Industries with Precision and Innovation
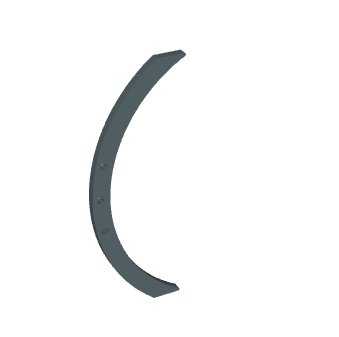
CNC Machining: Revolutionizing Lift Equipment Manufacturing
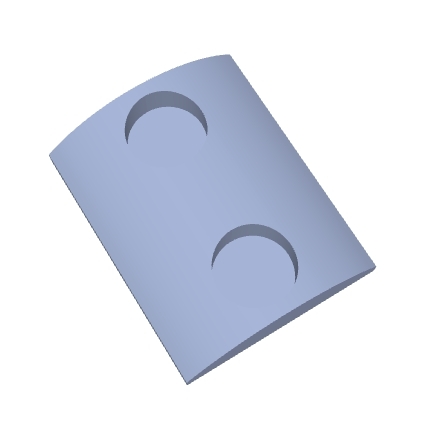
CNC Machining: Revolutionizing Security Systems with Precision Engineering
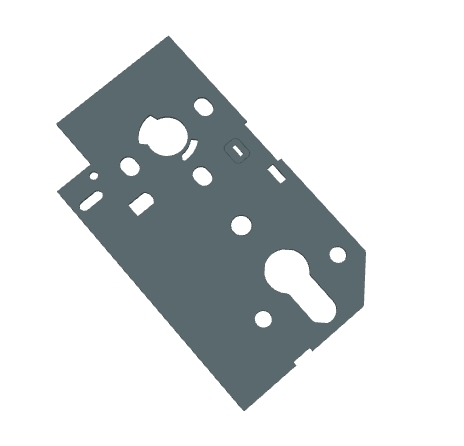
CNC Machining: Revolutionizing Secure & Stylish Lock Plates
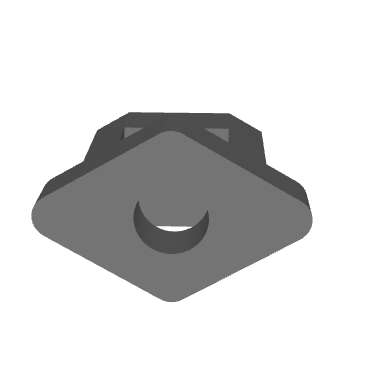
CNC Machining: Revolutionizing Precision with Cutting-Edge Components
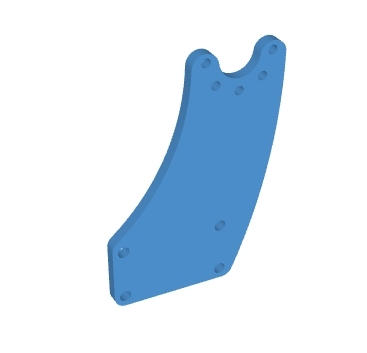
CNC Machining: Precision and Innovation in Rotating Parts

Explore Revolutionary CNC Machining with Precision Mounting Bracket
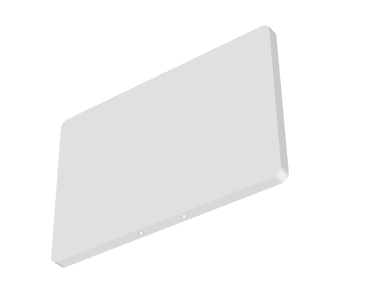
CNC Machining: Precision for Hoisting Systems & Modern Devices
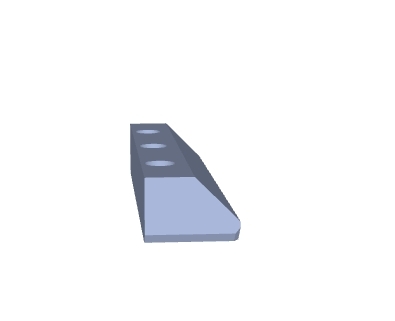
CNC Machining: Bespoke Solutions for Modern Metal Fabrication
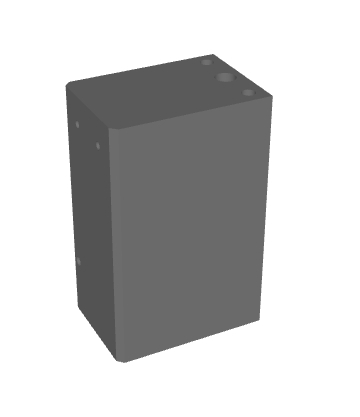
CNC Machining: Revolutionizing Machinery & Parking Systems